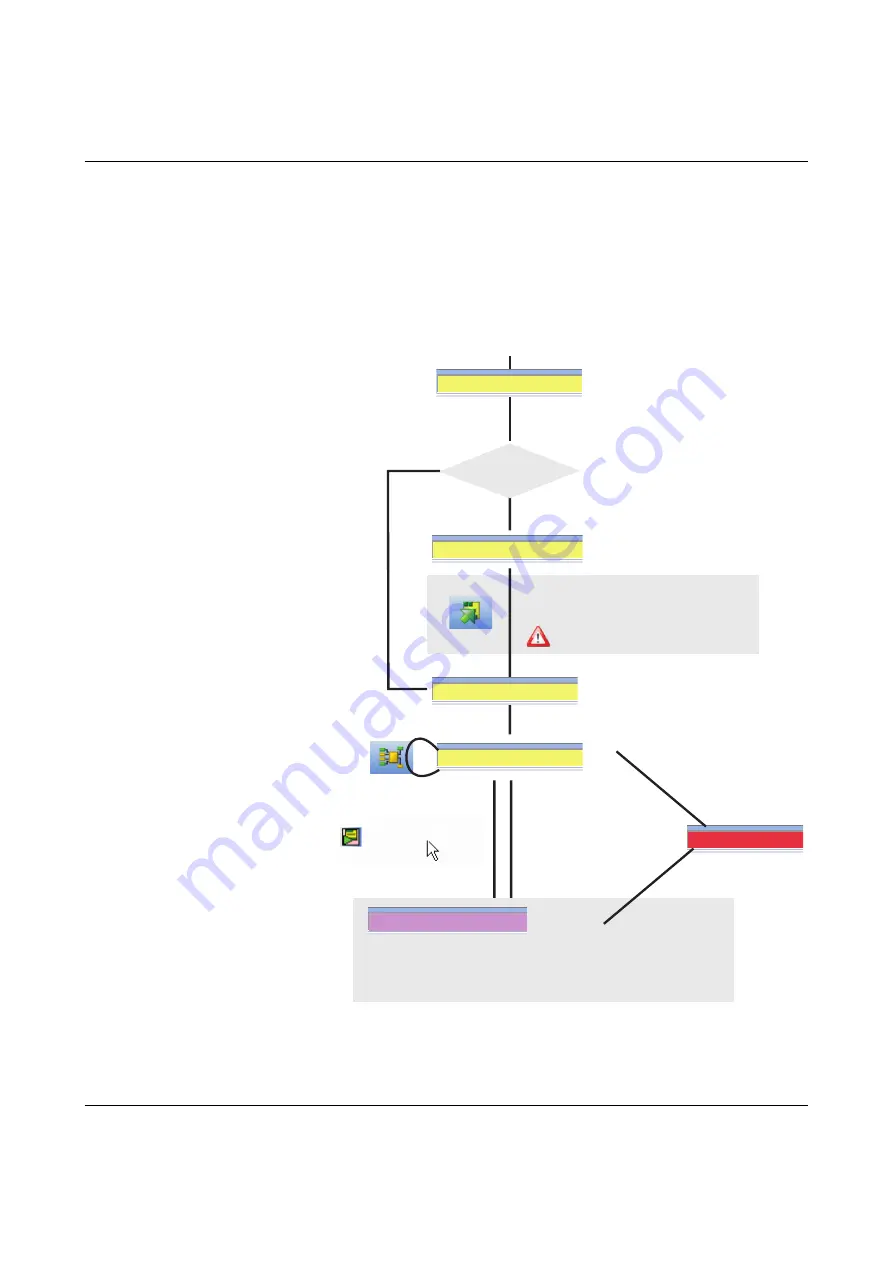
Hardware: PSR-TRISAFE-S safety module
103503_en_03
PHOENIX CONTACT
3-3
3.2
Operating modes (status) of PSR-TRISAFE-S
The diagram below illustrates the possible operating modes (status) of the PSR-TRISAFE-S
safety module and the possible status transitions. When there is a USB connection to the
PC, the module status is indicated on the far left in the status bar of the SAFECONF
configuration software.
Figure 3-3
Diagram: Possible operating modes (status) for the PSR-TRISAFE-S safety
module
Controller: Connected
Controller: Error
Safety module and PC
are connected via USB,
safety module
is switched on
Download project
Execution starts following
acknowledgment ("Confirm" button on the device)
Change between
safe online mode
and standard
startup mode
Error during execution
Error during execution
Connection editor
online or offline
USB connection (PC to safety module) must not be interrupted
and project in SAFECONF must not be changed.
Otherwise safety module is stopped and
changes to the safe state after 10 minutes.
Controller: No project
Controller: Startup
Startup
Controller: Timeout
Temporary state during:
- Saving process (during download)
- Initialization
- Safety module selftest
Yes
No
Temporary state during:
- Communication establishment
- Initialization
- Safety module selftest
Initial startup?
Controller: Timeout
Summary of Contents for 2986229
Page 2: ......
Page 32: ...PSR TRISAFE S 2 16 PHOENIX CONTACT 103503_en_03...
Page 50: ...PSR TRISAFE S 3 18 PHOENIX CONTACT 103503_en_03...
Page 74: ...PSR TRISAFE S 4 24 PHOENIX CONTACT 103503_en_03...
Page 88: ...PSR TRISAFE S 5 14 PHOENIX CONTACT 103503_en_03...
Page 90: ...PSR TRISAFE S 6 2 PHOENIX CONTACT 103503_en_03...
Page 96: ...PSR TRISAFE S 7 6 PHOENIX CONTACT 103503_en_03...