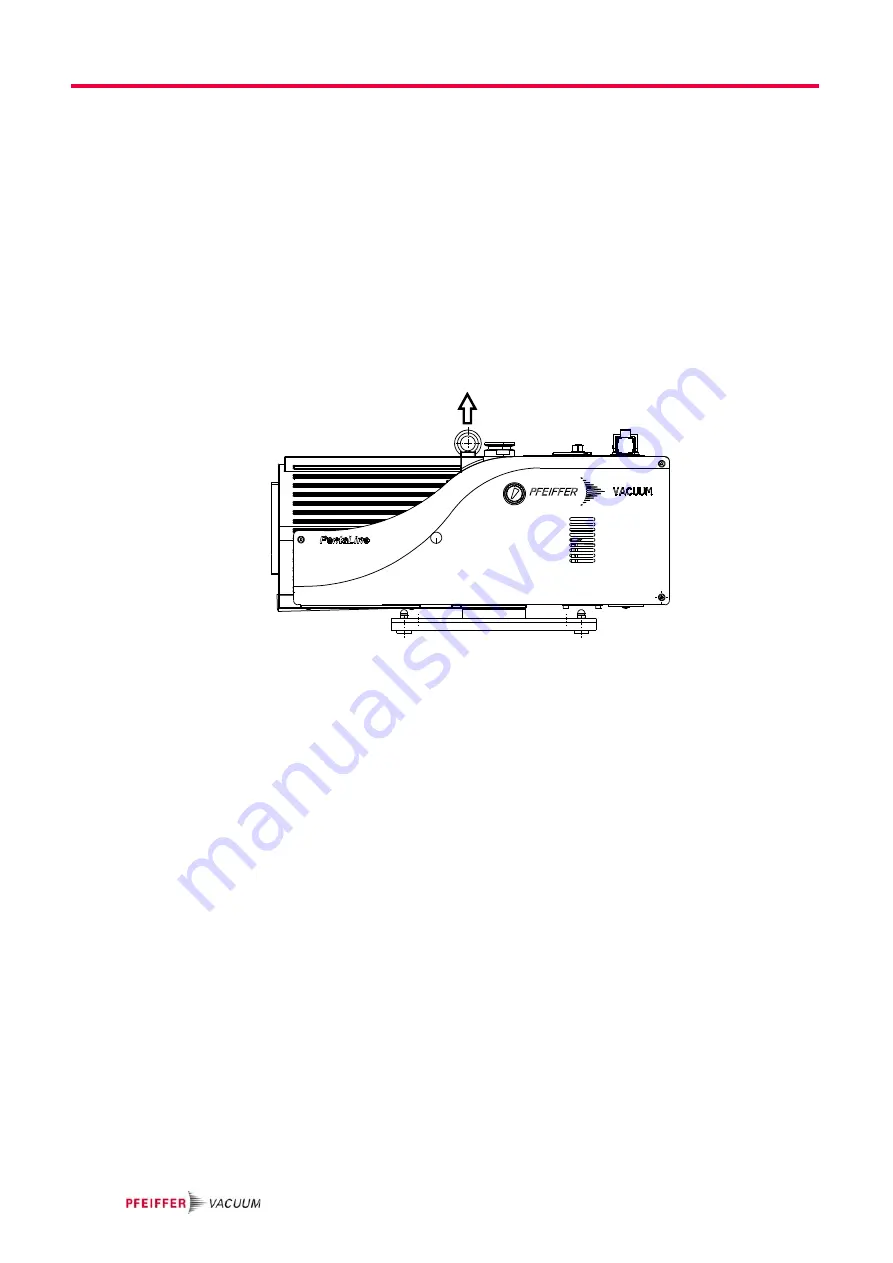
6
Transport and storage
• The operation of the devices in potentially radioactive areas.
3
Transport and storage
3.1 Transport
Remove the locking cap from the vacuum and exhaust flange immediately be-
fore connecting!
– Check the cone strainer, paying attention to the o-ring.
Use only the eye bolt on the top side of the pump to lift the pump.
Fig. 1: Transporting the pump
3.2 Storage
Check that all the openings on the pump are securely closed.
Store the pump in a cool, dry place; preferably at room temperature (approx.
20°C).
– For a longer period of storage, seal the pump in a PE bag with drying agents
enclosed.
– For a period of storage longer than one year, it is recommended to carry out
maintenance and change the operating fluid.
Summary of Contents for Penta 10
Page 31: ...31...