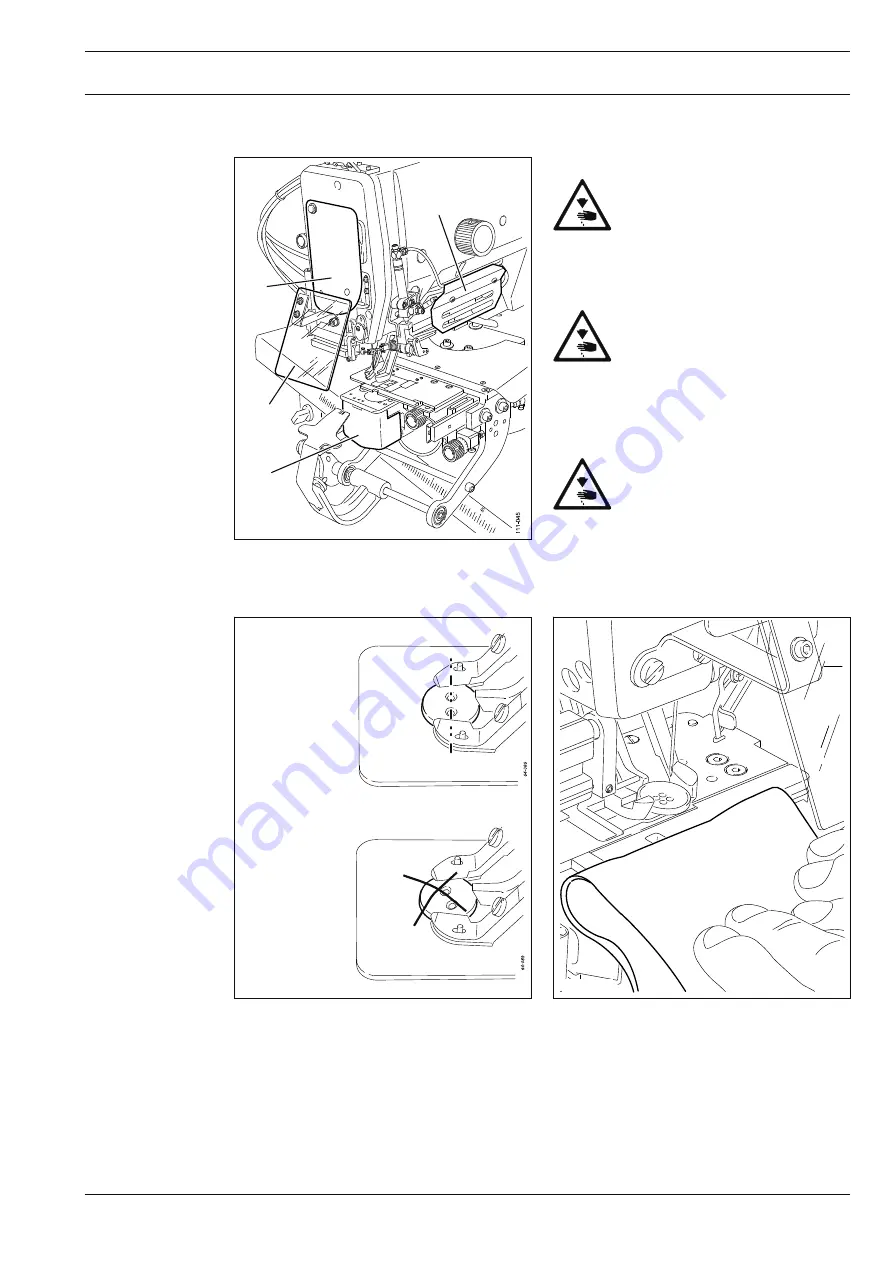
43
Sewing
Fig. 10 - 02
111-046
Switch on the machine, see Chapter
8
.
03
Switching the machine on/off
.
Setting up the machine, see Chapter
9
Setting up
.
Insert the button in the button clamp as shown in Fig.
10
.
02
, and position the workpiece
as shown in Fig.
10
-
03
.
Start the sewing operation, see Chapter
7
.
02
Pedal
.
●
●
●
●
10
.01
Sewing with the PFAFF 3307-3/..
Only operate the machine with
covers
1
and
2
closed!
Danger of injury from the mo-
vement of the take-up lever and
the hook!
Do not operate the machine wi-
thout eye shield
3
!
Danger of injury from fl ying
needle or button fragments!
Do not operate the machine
without protective cover
4
!
Danger of injury from clamp
drive!
Fig. 10 - 01
1
2
3
4
Fig. 10 - 03
Summary of Contents for 3307-3 Series
Page 139: ...139 91 191 513 95 Part 1 Version 14 11 06 Circuit diagrams ...
Page 140: ...140 Circuit diagrams Version 14 11 06 91 191 513 95 Part 2 ...
Page 141: ...141 91 191 513 95 Part 3 Version 14 11 06 Circuit diagrams ...
Page 142: ...142 Circuit diagrams Version 14 11 06 91 191 513 95 Part 4 ...
Page 143: ...143 91 191 513 95 Part 5 Version 14 11 06 Circuit diagrams ...
Page 145: ...145 91 191 514 95 Part 1 Version 14 11 06 Circuit diagrams ...
Page 146: ...146 Circuit diagrams Version 14 11 06 91 191 514 95 Part 2 ...
Page 147: ...147 91 191 514 95 Part 3 Version 14 11 06 Circuit diagrams ...
Page 148: ...148 Circuit diagrams Version 14 11 06 91 191 514 95 Part 4 ...
Page 149: ...149 91 191 514 95 Part 5 Version 14 11 06 Circuit diagrams ...