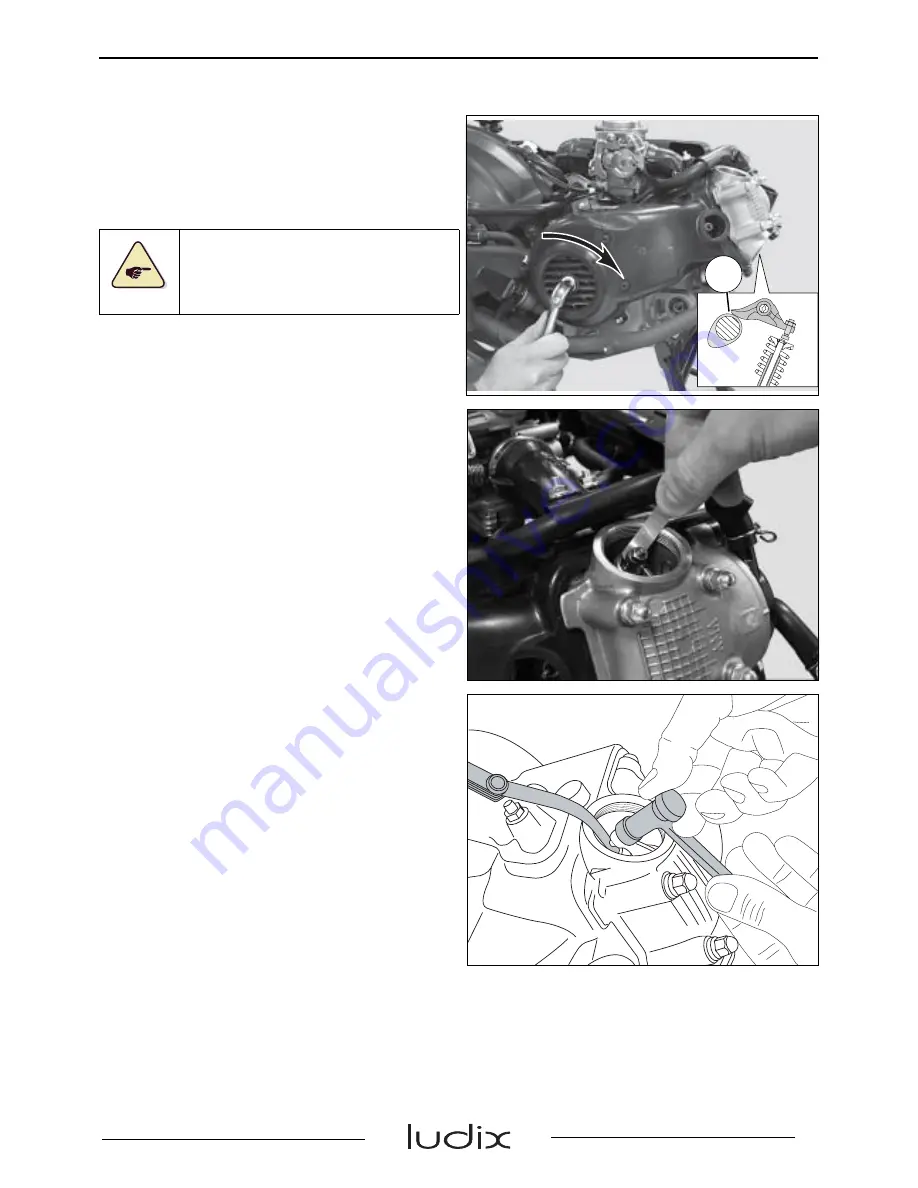
SERVICE OPERATIONS
27
Reproduction or translation, even partial, is forbidden without the written consent of Peugeot Motocycles
Installing the valve clearance
- Remove the power unit (See page 50).
- Remove the valve clearance adjustment
covers.
Apply the correct tightening torque to
the valve clearance adjustment covers.
Tightening torque: 15 Nm.
- Rotate the engine by hand in the operating
direction in order to bring the rocker pads on
the back of the cams (A).
- Using the set of feeler gauges, measure the
clearance of each valve.
- Clearances:
• Intake: 0.05 mm
±0.02
mm.
• Exhaust: 0.10 mm
±0.02
mm.
- If the clearance is not correct, adjust by
means of the cam follower screw.
- Use a wrench to adjust the valve clearance.
Type: Marolotest, P/N 500140.
Checking the valve clearance.
• At the intake a 0.10 mm feeler gauge
shouldn't go.
• At the exhaust a 0.15 mm feeler gauge
shouldn't go.
- On the contrary, if the fealer gauge goes,
reset the clearances.
A
Summary of Contents for Ludix 4T
Page 1: ...Sales division Technical network leadership WORKSHOP MANUAL ...
Page 2: ......
Page 54: ......
Page 55: ......