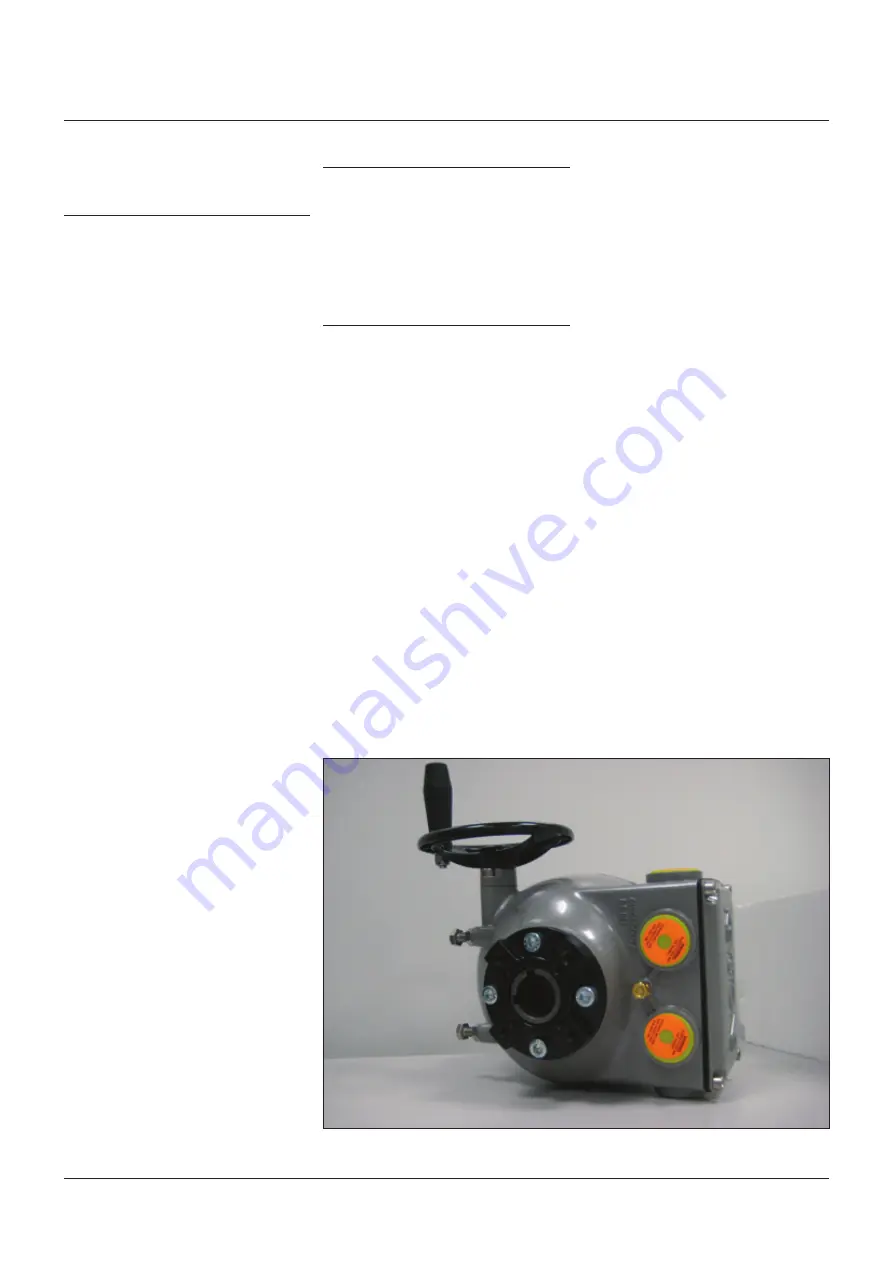
7
iMpOrtant
Check the ‘ambient temperature range’ printed
on the nameplate, for the correct utilisation with
respect to the ambient temperature. Installation
in ambient with temperature range outside the
specified values will invalidate the warranty.
figure 5 -
overview of one type of insert and drive details of the f02.
iMpOrtant
In case the screws of the cover, of the terminal
compartment and of the OM3 must be replaced,
SS Class A4 grade 80 screw must be used with
minimum yield strength 600 N/mm
2
.
Every time the main cover, the terminal
compartment cover and the OM3 are
reassembled, make sure to tight all the screws
with 5 Nm torque.
4 installation
4.1 CheCks tO Be perfOrMed BefOre
instaLLatiOn
to assemble the actuator onto the valve
proceed as follows:
• check that the coupling dimensions of the
valve flange and stem, or of the relevant
extension, meet the actuator coupling
dimensions
• the electrical supply cables must be suitable
for the power rating
• Gather the necessary tools for the assembly
and configuration of the actuator controls
• lubricate the valve stem with oil or grease
to make the assembly easier: pay attention
not to contaminate with lubricant the flange
surfaces which transmit the actuator torque
• clean the valve flange and remove anything
that might prevent a perfect adherence to the
actuator flange and especially all traces of
grease
• install the actuator onto the valve so that
the shaft output drive enters the groove of
the stem extension. this coupling must take
place without forcing and only with the weight
of the actuator. When the actuator output
shaft and the valve stem are connected,
check the holes of the valve flange. if they do
not meet with the holes of the spool piece
flange or the stud bolts screwed into them,
the actuator shaft output drive must be
rotated. actuate the manual override until
coupling is made possible. tighten the nuts of
the connecting stud bolts evenly
• if possible, operate the actuator to verify it
moves the valve smoothly
if a long storage period has occurred, before
reinstalling the actuator, please:
• check the status of the o-ring seals
• check the installation of the plugs or cable
glands on the cable entries
• check whether the enclosure covers or the
actuator body are cracked or broken
4.2 WOrking COnditiOn
standard f02 actuators are suitable for the
following environment temperatures:
• -25°c to +70°c (-13°f to +158°f)
special versions are available for extreme
environment temperatures:
• -40°c to +70°c (-40°f to +158°f)
4.3 COupLing BLOCk
the electric actuator is delivered with drive
details and flange in accordance with the
technical characteristics required by the
customer, ready to be installed onto the valve.
only one insert is included in the actuator
package delivered to end users.
Warning
During normal operation the temperature of
the actuator surface can reach 30°C above the
ambient temperature.
Biffi
f02 quarter-turn electric actuator
InstallatIon and MaIntenance InstructIons