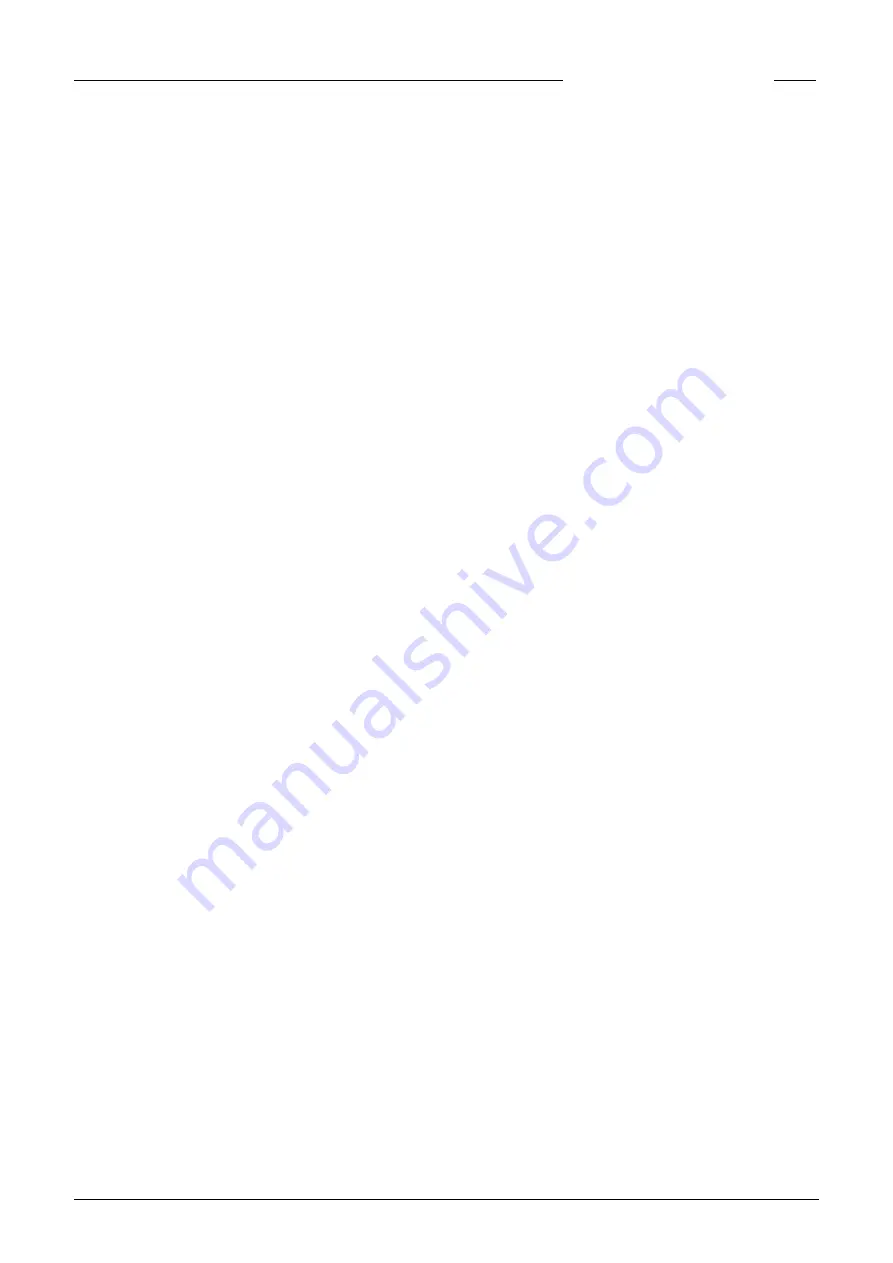
Before carrying out welding works or using electrical devices,
check to ensure there is no danger of explosion.
People working in wastewater systems must be vaccinated
against the pathogens that may be found there. For the sake of
your health, be sure to pay meticulous attention to cleanliness
wherever you are working.
Make sure that there are no toxic gases in the working area.
Observe the health and safety at work regulations and make
sure that a first-aid kit is to hand.
In some cases, the pump and the pumping medium may be hot
and could cause burns.
For installations in areas subject to explosion hazards, special
regulations apply!
AREAS OF APPLICATION
The ready to connect Compli sewage lifting stations are TÜV
certified and are suitable for the disposal of wastewater from
toilets and urinals, and domestic wastewater containing the
usual impurities.
The units have a level controller that switches the pump on and
off depending on the level of the water. An integrated alarm
system beeps if there is a malfunction, even if this is only tem-
porary.
If the pump overheats, the motor cuts out due to the winding
thermostat. After the thermostat has switched off the system,
pull out the mains plug before remedying the fault, since the
device can switch itself on again automatically if the power is
still connected. A direct malfunction message is not generated.
The tanks can withstand submersion to a depth of not more
than 2 m of water and a submersion period of up to 7 days.
The control unit cannot withstand submersion, but is splash-
proof in accordance with IP 44.
If installed in compliance with the regulations and used prop-
erly, then this control unit meets the protective requirements
of the EMC Directive 2014/30/EU and is suitable for domestic
use and connection to a power supply from the grid. When
connected to an industrial mains within an industrial operation
with power supply provided by a company-own high-voltage
transformer, insufficient immunity to interference has to be
expected.
When using the pumps, the relevant national laws, regulations
and stipulations must be adhered to, for example:
•
Sewage disposal units for building and ground drainage
systems (e.g. EN 12050 and 12056 in Europe)
•
Installation of low voltage systems (e.g. VDE 0100 in Ger-
many)
•
Safety and working materials (e.g., BetrSichV and BGR 500
in Germany)
•
Safety in wastewater systems (e.g., GUV-V C5, GUV-R 104
and GUV-R 126 in Germany)
•
Electrical systems and operating resources (e.g., GUV-V A3
in Germany)
•
Explosion protection EN 60079-0,
EN 60079-1, EN 60079-14, EN 60079-17 and EN 1127-1
Scope of supply
•
Tank with pumps and clamp flange for inlet
•
Reducer DN 150 / DN 100 for Compli 1000
•
Slip-on socket pipe for ventilation pipe (Compli 1200 flexible
connection with hose clamps)
•
Connection flange for pressure pipe
•
Flexible connection with hose clamps for the pressure pipe
•
Plug-in seal(s) for the diaphragm hand pump or additional DN
50 inlet
•
Fixing materials for tank
•
Non-return valve for the pressure pipe
•
Control
Mode of operation:
intermittent operation S3; see "Technical
Data"
INSTALLATION
The pump must be installed so that it is buoyancy-proof and
free-standing. At least 60 cm free working space must be pro-
vided around and above the parts that require access for op-
eration or maintenance.
Ventilation: The ventilation pipe must be vented above roof level.
Inlet: A wastewater sluice valve must be installed in the inlet at
the front of the tank.
Pressure pipe: A further wastewater sluice valve must be in-
stalled behind the non-return valve in the pressure pipe. If the
non-return valve is not included in the scope of delivery of the
pumping unit, then an EN 12050 certified swing-type check
valve must be fitted.
The pressure pipe must be laid in a loop above the local backup
level.
A pump sump must be provided to facilitate the disposal of wa-
ter from the pump installation area.
NOTICE!
All bolts that are used for fixing individual compo
-
nents to the tank should be tightened with a torque of no more
than 6 Nm.
Installing the tank
Close the sluice valve in the inlet (accessory) to prevent any
leakage of water during the installation work.
Units must be slid onto the inlet pipe, together with the clamp
flange, as far as possible and then aligned.
If a DN 150 side inlet is used, the inlet must first be opened
at the marked position using a hole saw, Ø 152, and then de-
burred. The standard inlet must then be closed using a closure
kit (accessory) and the switch-on level must be reset.
In the case of Compli 1000, the inlet can be reduced from DN
150 to DN 100 if the enclosed reducer is first of all fitted to the
clamp flange.
Tighten the hexagon screws on the clamp flange.
Mark the positions of the holes for fixing the tank to the floor,
then drill the holes.
Insert the wood screw, together with the washer and wall plug,
into the drill hole in the tank and tighten it.
NOTICE!
Ensure that the tank does not become deformed due
to overtightening the screws, otherwise this could result in
leakage.
The tanks for Compli 1200 units are additionally fixed with two
brackets at the sides.
3
ENGLISH
Summary of Contents for 1225/2 BW
Page 18: ...Compli 1000 Compli 1200 18 ...
Page 19: ...Compli Sensor 19 ...
Page 20: ...HighLogo 2 610 ECP 1 20 ...
Page 21: ...HighLogo 2 610 ECP 2 21 ...
Page 22: ...HighLogo 2 00 P 2 610 P 1 22 ...
Page 23: ...HighLogo 2 00 P 2 610 P 2 23 ...