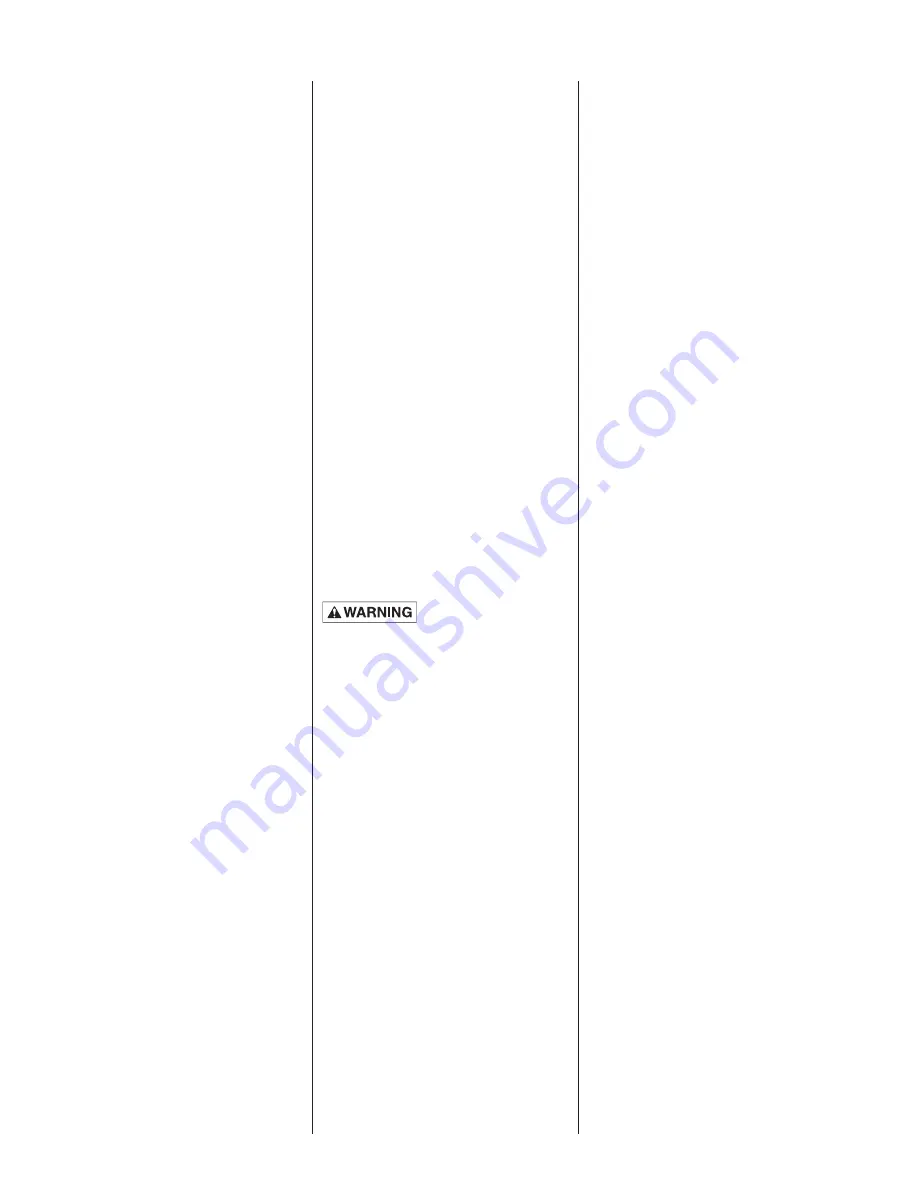
2
Safety Warnings
Before Installation:
This manual contains important
information for the safe use of
this product. Read this manual
completely and follow the
instructions carefully. Reasonable
care and safe methods relating to
the installation and operation of
this product should be practiced.
Check local codes and requirements
before installation.
DANGER: Risk of Electrical Shock
or Electrocution. May result in
serious injury or death or fire
hazard. Installer must disconnect
all electrical sources prior to
installation, handling or servicing.
Only qualified personnel may install
this system. NFPA 70/National
Electric Code (NEC) or local codes
must be followed. System must be
properly grounded according to
NEC. Do not lift pump by power cord.
DANGER: Biohazard Risk. Once
wastewater source has been
connected to system, biohazard risk
exists. Installer(s) and/or service
personnel must use proper personal
protective equipment and follow
handling procedures per OSHA
29 CFR 1910.1030 when handling
equipment after wastewater source
has been connected to system.
DANGER: Risk of Asphyxiation.
Installer(s) and/or service personnel
must use proper personal protective
equipment and follow OSHA 29
CFR 1910.146 or OSHA 29 CFR 1926.
Pump may be installed in a location
classified as a confined space.
DANGER: Risk of Fire or Explosion.
Do not smoke or use open flames in
or around this system.
DANGER: Cutting Risk. Risk of
serious cutting or amputation exists.
Disconnect all power sources prior
to servicing pump. Pump may start
without warning.
Do not modify the cord and plug.
When using the cord and plug, plug
into a grounded outlet only. When
wiring to a system control, connect
the pump ground lead to the
system ground.
Do not run the pump dry. Dry running
can overheat the pump (causing
burns to anyone handling it) and will
void the warranty.
The pump normally runs hot. To
avoid burns, allow it to cool for 30
minutes after shutdown before
handling it.
Submersible sump pumps are not
approved for use in swimming pools,
recreational water installations,
decorative fountains or any
installation where human contact
with the pumped fluid is common.
Pump is designed to be installed
in a sump or wet location where
drainage collects.
CALIFORNIA PROPOSITION 65
WARNING:
This product and
related accessories contain
chemicals known to the State of
California to cause cancer, birth
defects or other reproductive harm.
General Information
Unpacking Pump:
Remove pump from carton. When
un pack ing unit, check for con cealed
damage. Claims for damage must be
made at the receiving end through
the delivery carrier. Damage cannot
be processed from the factory.
WARNING: Before handling these
pumps and controls, always
disconnect the power first. Do not
smoke or use sparkable electrical
devices or flames in a septic
(gaseous) or possible septic sump.
Pumps Not Operating or
in Storage:
Pumps with carbon ceramic seals
must have impellers manually
rotated (6 revolutions) after setting
nonop er a tion al for 3 months or
longer and prior to electrical
start-up.
Pumps with tungsten carbide seals
must have impellers manually
rotated (6 revolutions) after setting
non-op er a tion al for 3 weeks or
longer and prior to electrical
start-up.
Seal Failure:
An electrode is installed in the seal
chamber so if any water enters the
chamber through the first seal the
elec trode will be energized and a
sig nal will be trans mit ted to the sen-
sing unit at ground surface causing
a red light to turn on. The elec trode
probe is installed in all units but the
sensing unit is sup plied at extra cost
and must be ordered.
In operation the seal failure unit
in di cates only that there is some
water in the seal chamber. The
pump will con tin ue to operate
without damage, but the seal should
be checked im me di ate ly after failure
is indicated.
The sensing unit is recommended
on all installations.
All hazardous location submersible
pumps have two factory installed
mois ture detectors (seal failure
probes). They are in a normally open
series cir cuit, in the seal chamber.
Un der normal operating conditions,
the circuit remains open. If the
lower seal leaks and moisture enters
this cham ber, the moisture would
settle to the bottom of the chamber
and will com plete the circuit
between the mois ture detectors.
This circuit must be connected to
a sensing unit and signaling device.
This is supplied in a Hydromatic
®
built control panel.
NOTE: Failure to install such a
device negates all war ran ties by
Hydromatic.
Summary of Contents for S3R
Page 9: ...9 Wiring Diagrams...