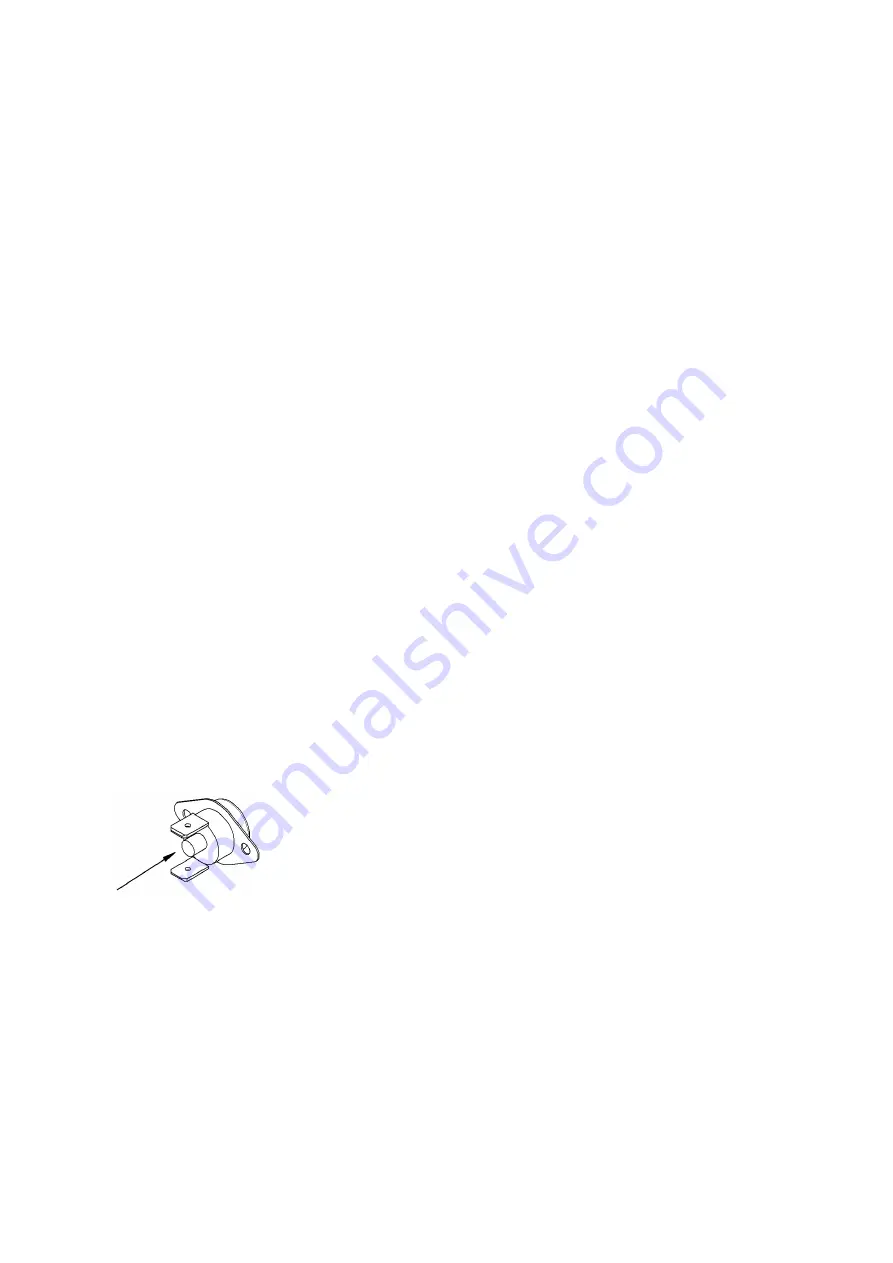
PV 100a
Feed screw motor
The condition of the feeding screw motor is crucial for safety. Therefore the motor must be replaced
after every 2000 working hours or after 120-150 tons of pellets are burned or when the burner gives
warning. Burnered pellets amount (in kg) is accessible from info-menu.
Battery
Battery must be replaced when the burner gives warning message or after 5 years. As the battery is
also safety device, burner monitors the state of battery and blocks next work cycle if battery voltage
is not within limits.
Fan
The air in boiler room contains dust that can deposit on fan bearings. The best cure is to keep boiler
room as clean as possible. Otherwise the fan bearings can get stuck after several years of working
and must be replaced.
Resetting safety thermostat
In case of overheating the burner flashes yellow indicator and displays message OVERHEAT. The
safety thermostat must be reset manually. Thermostat is located on the horizontal tube of inner
auger.
1. Make sure the burner has cooled down and disconnected from power supply.
2. Remove the cover by loosening 4 screws (2 on both sides)
3. Press small button on thermostat.
4. Connect power supply
5. Press OK for 5s
6. If indicator keeps flashing, you need to replace the thermostat.
Figure 11: Resetting the
safety thermostat
27