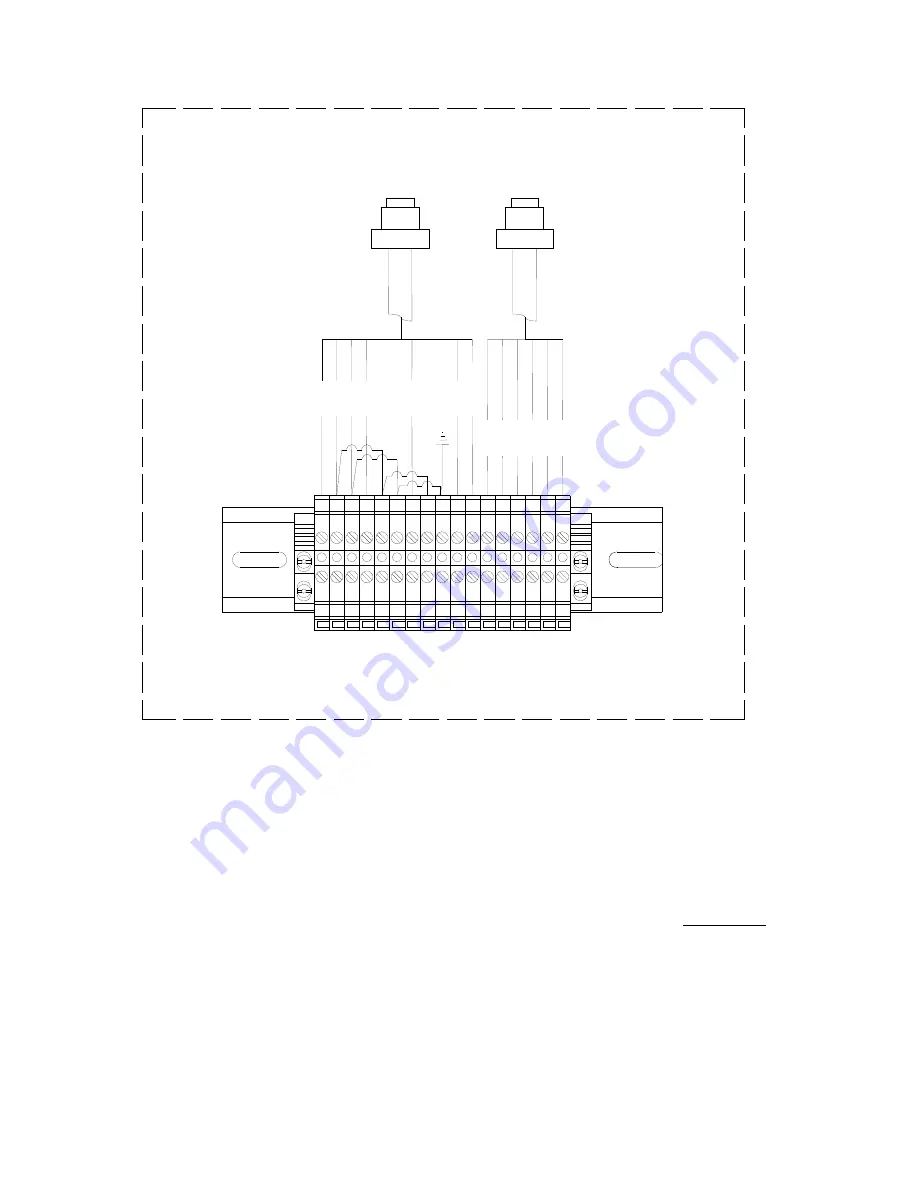
PB-1525 Wood Pellet Burner System: Installation and Operation Manual
Rev 1.0, OCTOBER 2011
Page 21 of 67
1
2
3
4
5
6
7
8
9 10 11 12 13 14 15 16 17
6-CONDUCTOR
CABLE
7-CONDUCOR
CABLE
GRN
WHT
WHT
G
R
N
B
L
K
W
H
T
G
R
N
R
E
D
B
L
U
O
R
G
W
H
T
/B
L
K
B
L
K
W
H
T
G
R
N
R
E
D
O
R
G
B
L
U
TERMINAL PANEL
ENCLOSURE
Figure 2.7: Factory Terminal Connections within the Pellergy Supplied
enclosure.
There are two external electrical connections required to connect the PB-
1525:
1.)
Connection to a 120V AC Power Source
2.)
Connection to a thermostat (Normally Open Switch with no power)
There are two required components of the PB-1525 system that need to
be field connected. These are the:
1.)
Auger Motor
2.)
Stack Temperature Sensor