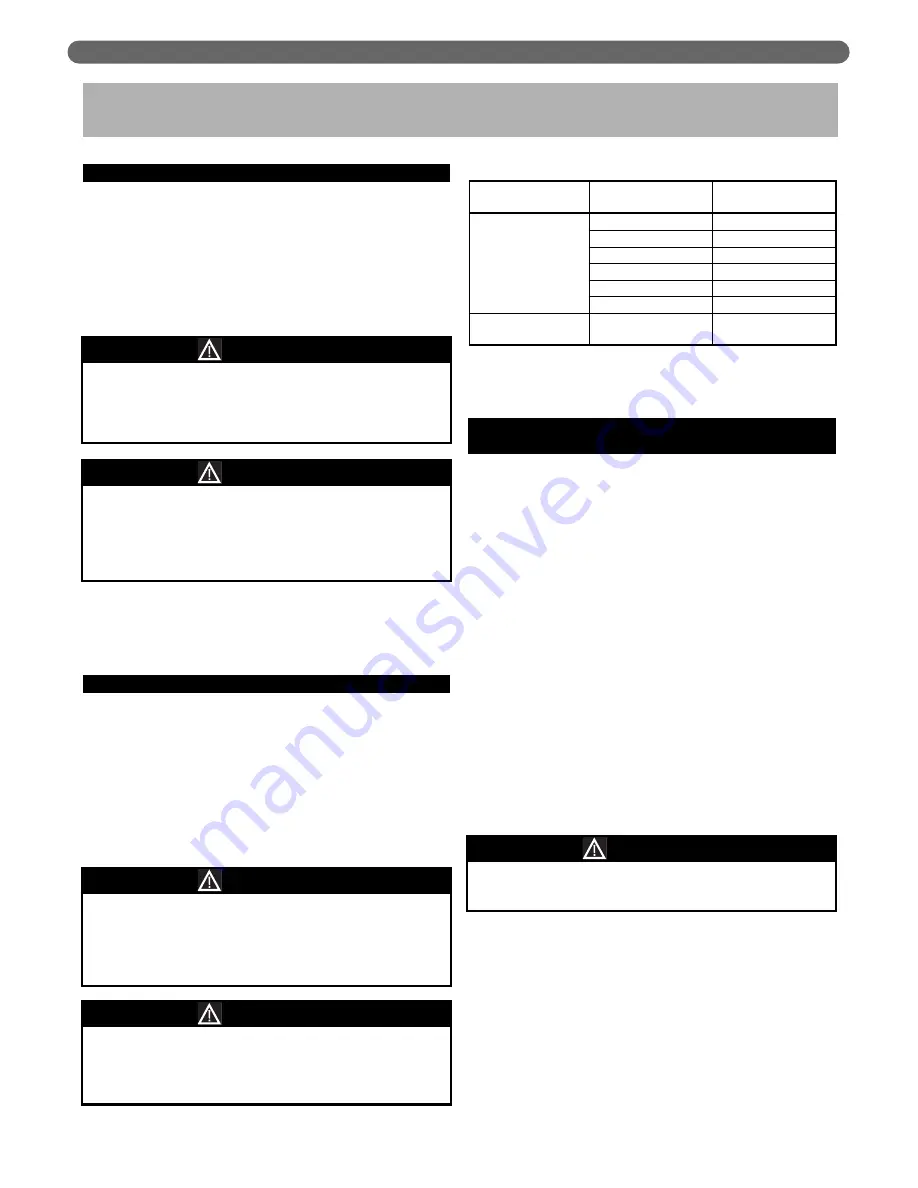
A. GENERAL
1. Install the PureFire boiler venting system in
accordance with these instructions and with the
National Fuel Gas Code, ANSI Z223.1/NFPA 54
,
CAN/CGA B149
, and/or applicable provisions of local
building codes.
2. The PureFire boiler is a direct vent appliance and is
ETL Listed as a Category IV appliance with Intertek
Testing Laboratories, Inc.
3. Sources of combustion air contaminated with chlorine,
ammonia or alkali agents must be avoided. Do not
install this boiler near a swimming pool, hot tubs or
laundry. Do not store chemicals near the boiler.
B. APPROVED MATERIALS
1. Table 3.1 lists approved materials for vent pipe (and
adhesives where applicable). Use only these materials
for exhaust vent piping.
2. PVC pipe and fittings are not to be used for venting in
confined spaces such as closet installations. Use only
CPVC or approved polypropylene (InnoFlue or
PolyPro) vent pipe under these conditions.
3. Cellular core piping is approved for inlet air piping only.
* PVC pipe/fittings are not to be used for venting within confined spaces.
Notice: Installations in Canada require compliance with
ULC S636 – Standard for Type BH Gas Venting Systems.
C. EXHAUST VENT/AIR INTAKE PIPE
LOCATION
1. Install vent piping before installing water, fuel, or
condensate piping. Working from largest to smallest
diameter reduces the complexity of piping
interferences.
2. Vent and air intake piping is to be installed so that
there is sufficient access for routine inspection as
required in Section 11 of this manual.
3. The vent piping for this boiler is approved for zero
clearance to combustible construction. However, a fire
stop must be used where the vent pipe penetrates
walls or ceilings.
4. The PureFire boiler, like all high efficiency, gas-fired
appliances, is likely to produce a vapor plume due to
condensation. Surfaces near the vent termination will
likely become coated with condensation.
5. The maximum combined vent and air inlet vent
length for the Infinite Energy boiler is about 200
equivalent feet (60 m). Be sure that the boiler is
located such that the maximum vent length is not
exceeded.
6. Air Intake Pipe Location – Sidewall Venting:
a. Provide 1 foot (30 cm) clearance from the bottom
of the air intake pipe to the level of maximum
snow accumulation. Snow removal may be
necessary to maintain clearances.
b. Do not locate air intake pipe in a parking area
where machinery may damage the pipe.
c. Maintain a minimum of 8” horizontal distance
between exhaust vent and the air intake.
Increasing this distance minimizes the potential for
contamination of the inlet air with exhaust.
3. VENTING & AIR INLET PIPING
The venting system for this product is to be installed in
strict accordance with these venting instructions.
Failure to install the vent system properly may result in
severe personal injury, death or major property damage.
WARNING
This vent system operates under positive pressure.
Vent connectors serving appliances vented by
natural draft shall not be connected into any portion
of this venting system. Failure to comply may result
in serious injury, death or major property damage.
WARNING
Only materials listed in Table 3.1 are approved for use
with PureFire boilers. Use only these components in
accordance with these instructions. Failure to use
the correct material may result in serious injury,
death, or major property damage.
WARNING
Use of cellular core pipe for any exhaust vent
component is prohibited. Use of cellular core pipe
may result in severe personal injury, death, or major
property damage.
WARNING
If the maximum equivalent vent length is exceeded,
the maximum burner input rate may be reduced.
NOTICE
8
VENTING & AIR INLET PIPING
Table 3.1: Approved Materials for Exhaust Vent Pipe
Description
Material
Conforming to
Standard
Exhaust Vent Pipe &
Fittings
PVC (Sch 40 or 80)
*
ANSI/ASTM D1785
CPVC (Sch 40 or 80)
ANSI/ASTM D1785
PVC-DWV
*
ANSI/ASTM D2665
FasNSeal
®
UL1738 & ULC S636
PolyPro
®
ULC-S636
InnoFlue
®
UL1738 & ULC S636
Pipe Cement
(PVC & CPVC Only)
PVC/CPVC Cement
ANSI/ASTM D2564
Summary of Contents for PUREFIRE PFW-199
Page 20: ...18 WATER PIPING AND CONTROLS Figure 4 3 Schematic Piping One Boiler with a Single Storage Tank...
Page 60: ...58 Figure 13 2 Heat Exchanger Burner Assembly Repair Parts REPAIR PARTS...
Page 63: ...61 APPENDIX A STATUS SCREENS APPENDIX A STATUS SCREENS...
Page 64: ...62 APPENDIX A STATUS SCREENS...
Page 65: ...63 APPENDIX A STATUS SCREENS...
Page 66: ...64 APPENDIX B USER MENU APPENDIX B USER MENU...
Page 67: ...65 APPENDIX B USER MENU...
Page 68: ...66 APPENDIX C INSTALLER MENU APPENDIX C INSTALLER MENU...
Page 69: ...67 APPENDIX C INSTALLER MENU...
Page 70: ...68 APPENDIX C INSTALLER MENU...
Page 71: ...69 APPENDIX C INSTALLER MENU...