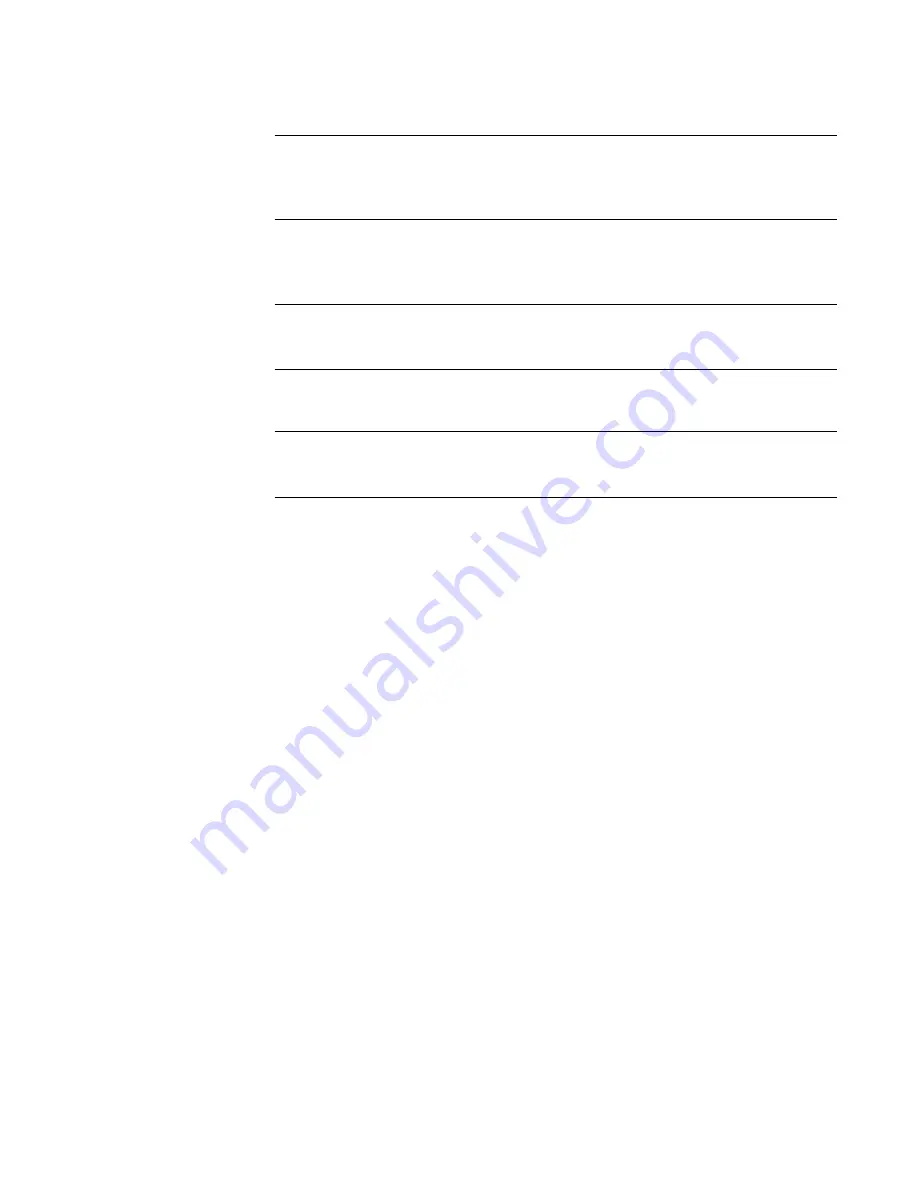
P
AGE
58
Er 36
- Incorrect Crystal
1. Turn off the power to the instrument, wait 5 seconds,
For Digital Comm.
then turn the power on.
2. Check crystal, Y1, for 11 MHZ (see Appendix A-2,
Page 60).
Er 37
- Incorrect Micro.
1. Turn off the power to the instrument, wait 5 seconds,
For Digital Comm.
then turn the power on.
2. Check to see if U1 is marked "8032" (see Appendix
A-2, Page 60).
Momentary Er 70
-
1. Tried to communicate while unit was in a non-control
Controller unable to respond
mode.
within 250 milliseconds.
Momentary Er 71
-
1. The unit received a request before proper amount of
Byte received before the
time has elapsed since last request.
response was transmitted.
Momentary Er 72
-
1. Data received not valid, possible corruption on the
Incorrect Block check
comm link. Possible noise.
character was received.
Momentary Er 73
-
1. Improper parity selection on the transmitting terminal.
Byte received with incorrect
2. Incorrect baud rate.
parity.
3. Noise