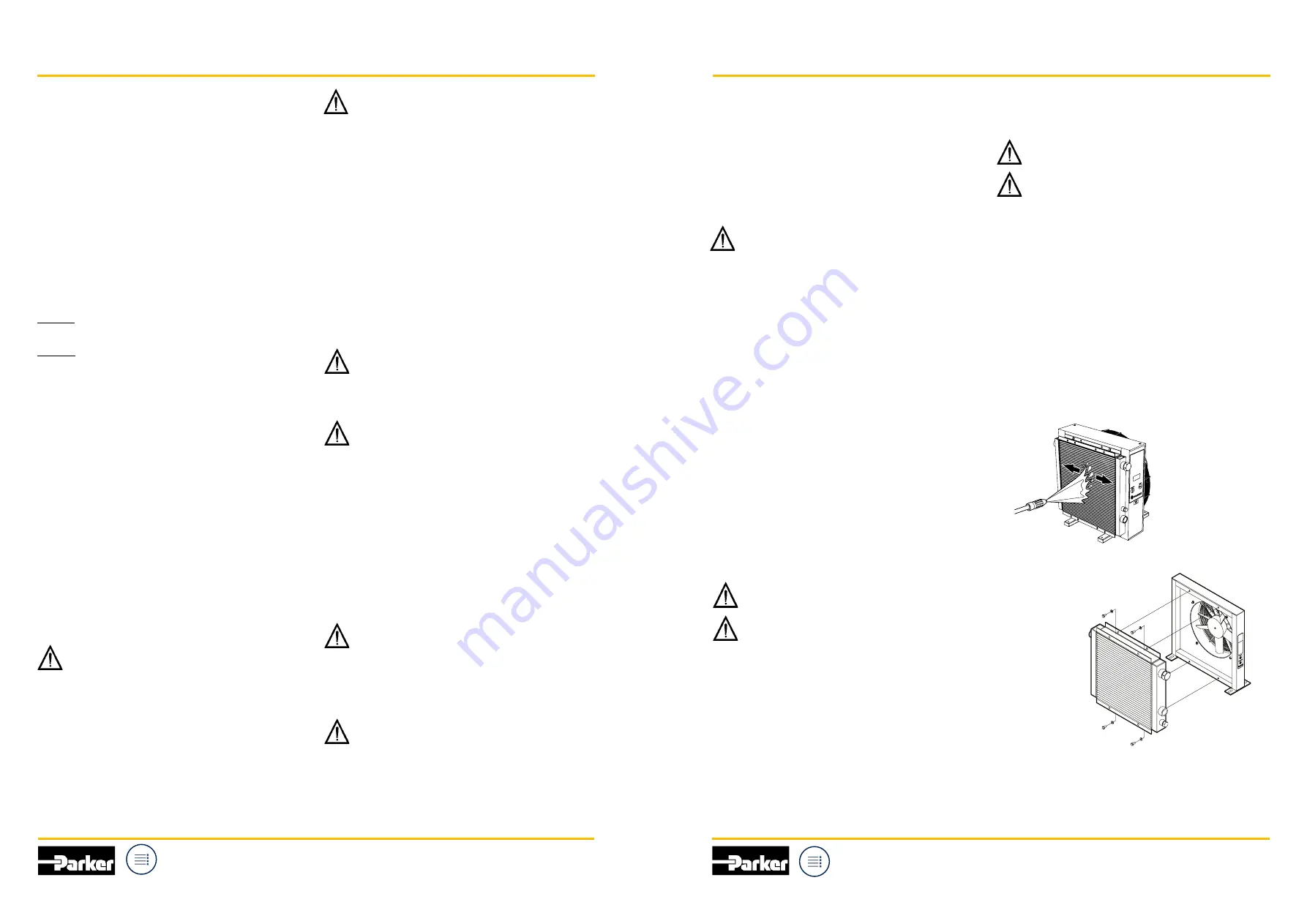
3. Installation/Handling
Acoustic pressure level
could reach 50 - 86 dB(A) at 1 m
distance depending on air fluid cooler size and rotation speed
under normal operating conditions. An inappropriate location or
operation under extreme conditions could cause an increase in
acoustic pressure level and a decrease in cooling capacity.
Identification plate
The identification plate of the air fluid cooler is fitted on the fan
housing and contains the following information: See Figure 2.
A
– Part number.
B
– Designation.
C
– Serial number.
D
– Date of delivery
(year and week, e.g. 1018, i.e. year 2010 and week 18).
Replace a damaged or missing identification plate as soon as pos-
sible.
Fluids
WATER: add corrosion inhibitors to the water to avoid corrosion.
All materials included in the cooling circuit must be considered for
choice of correct inhibitor.
GLYCOL: Mix glycol and water in a ratio of 50% / 50% before filling!
Never mix different types and different brands of glycol. We recom-
mend the use of demineralized or osmosis water.
Additives like Glysantin G48 or TYFOCOR have demonstrated their
ability to prevent corrosion in a closed cooling circuit.
See supplier information regarding water quality, additive quantity
and periodic replacements.
CAUTION: Follow material safety data sheets (MSDS) of glycol
manufacturers! Please note that the coolant is considered hazard-
ous waste and needs to be disposed accordingly.
Filtration
The use of a filter allows reducing the presence of impurities or
chips in the liquid circuit in order to prevent any obstruction.
Check the contamination with particles and biological changes,
the composition of the water-glycol mixture and the current pos-
sible temperature range in which it can be operated at regular
intervals. Change the filter elements if the values deviate from the
values at initial start-up. Follow the filter manufacturer’s instruc-
tions and the fluid manufacturer’s MSDS.
Suggestion : use spin-on filter design in a bypass channel.
Installation
Lifting
Caution
Risk of bodily injury. To prevent physical harm when
lifting the unit, use the correct lifting technique. Make sure
that all lifting devices are free from damage and approved
for the weight of the air fluid cooler.
Mounting
The QDC air fluid cooler can be mounted in any position. Howev-
er, an upright installation standing on its feet is recommended. A
free space corresponding to a minimum of half the height of the
matrix should be available in front of and behind the air fluid cool-
er to allow for optimal cooling capacity and low acoustic power
level. See Figure 3.
An inappropriate location or operation under extreme conditions
could cause an increase in acoustic pressure level and a decrease
in cooling capacity.
Important
The cooler matrix is designed for maximum dynamic
working pressure 14 bar. When the cooler is installed in a return
line, there should be no pressure spikes. If this is not possible, an
offline cooling system should be used.
Electrical connection
Precaution
Prior to connecting the DC motor to the supply
system, make sure the information on the motor label
corresponds to specified direct current.
The DC motor must only be installed according to general and
electrical safety rules. Circuit diagram, see Figure 6 and Interface
Hardware for digital control, see p.12 (5.07)
Precaution
Be careful when connecting. Improperly
made connections, damaged cables, etc. could cause
components to become live or result in the incorrect di-
rection of rotation of the DC motor and fan.
Note!
A motor overload protection is recommended. The size
of the overload protection/fuse, depends on fan size and air flow
across the cooler. Contact Parker concerning motor protection/fuse
size. An automotive fuse according ISO8820 must be chosen
and used by the customer in the application wire harness.
Each drive must be protected by the unique proper fuse (e.g. in
case of double fan modules, two fuses are needed).
The QDC air fluid cooler can be fitted with a thermo sensor on the
inlet and outlet side for temperature control. The fan RPM can be
controlled by the integrated inverter, see p.12 (5.07)
Handling
Prior to initial start-up
Precaution
Check that the air fluid cooler is securely fixed
and correctly connected.
We recommend that you proceed as follows prior to start-up:
1. Run the air fluid cooler with the system fluid.
2. Filter the fluid before passing through the cooler.
See Technical specification for recommended fluid compatibility.
Prior to start up
Precaution
Do not start the air fluid cooler if there is a risk
of damage to person, property or environment.
Check that:
• all air fluid cooler parts are free from damage
• the air fluid cooler is correctly connected
• the fan rotates freely (use hand force)
• all liquid connections are tight
• the inside of the fan housing is free from objects that could be
thrown around and cause bodily injury or damage to property.
At start-up
Check that:
• the direction of rotation of the fan and the air flow corresponds
to indications on the fan housing
• the air fluid cooler is free from abnormal noise and vibrations.
• the air fluid cooler is free from leaks
In order to protect the cooler matrix, use a by-pass valve when
operating in cold start mode/with thick lubricating oils.
During operation
Caution
Risk of severe burns. The air fluid cooler could
become extremely hot during operation. Make sure that the
air fluid cooler is cool before touching.
Maximum permitted fluid temperature in the cooler matrix is
120 °C.
The cooler matrix is designed for maximum allowed dynamic
working pressure of 14 bar.
Do not overload the DC motor (see p.12 (5.07)). See identification
plate.
Note!
Use hearing protection when standing in the immediate vi-
cinity of an operating air fluid cooler for long periods of time.
Preventive maintenance
Preventive maintenance work must be carried out at regular
intervals. Make sure that:
• there is no abnormal noise or vibrations
• air fluid cooler is securely fixed
• the cooler matrix is clean - debris will reduce the cooling
capacity
• the air fluid cooler is free from damage, replace damaged
components
• the air fluid cooler is free from leaks, take appropriate
measures
• warning labels are in good condition, replace any damaged/
missing label immediately.
Annually:
Check the electrical installation.
Cleaning
Precaution
Risk of bodily injury. Prior to cleaning,
disconnect all motor power supplies.
Caution
Risk of severe burns. The air fluid cooler could be-
come extremely hot during operation. Make sure the air fluid
cooler is cool before touching.
Air fluid cooler
When cleaning the exterior of the cooler, for
instance using water, disconnect all power supplies. Be aware
of the DC motor protection standard.
Cooler matrix
The air fins of the matrix can be cleaned by blow-
ing through with compressed air
1
. If necessary a high-pressure
water system can be used
3
. When using a high-pressure water
system point the jet parallel to the air fins. See Figure 7.
Fan housing
Remove the cooler matrix when cleaning the in-
side of the fan housing. To clean the inside of the fan housing,
use compressed air
1
. If necessary suitable cleaning
agents
2
can
be used. Blow with compressed air
1
from the electric motor side
through the fan guard.
Maintenance
Parker shall not be held responsible for any consequences due to
repair and/or modification made by the customer.
Caution
Risk of severe burns. The air fluid cooler could
become extremely hot during operation. Make sure the air
fluid cooler is cool before touching.
Caution
Risk of bodily injury. Disconnect the motor power
supply prior to maintenance.
Dismounting the cooler matrix
1. Turn off the system.
2. Disconnect the electric motor power and control supply.
3. Make sure that the system is depressurized.
4. Disconnect the liquid inlets and outlets.
5. Disconnect the flexible hoses from the cooler matrix.
6. Unscrew the screws with washers fixing the cooler matrix to
the fan housing: See Figure 8.
7. Remove the cooler matrix.
Mounting of the cooler matrix
1. Locate the cooler matrix.
2. Fit the cooler matrix to the fan housing. See Figure 8.
3.
Connect the flexible hoses to the cooler matrix.
4. Connect the electric motor power and control supply.
5. Proceed to Paragraph Handling:
Prior to start-up and At start-up.
D
AIR OIL
COOLER
LDC
LDC
7
AIR
OIL
COO
LER
LAC
LAC
8
Precaution
Risk of bodily harm. Make sure that the air fluid
cooler is securely fixed.
Connection of the cooler matrix
Connect the cooler matrix using flexible hydraulic hoses. Make
sure that all connections and hoses are sized according to the
system pressure, flow, temperature and type of liquid.
Connect the hoses to the cooler matrix as illustrated below. See
A
– Inlet |
B
– Outlet |
C
– Inlet G 1/2 sensor port
D
– Outlet G 1/2 sensor port
Dimensions on connections are cooler matrix size dependent,
see catalogue.
Connection chart, See Figure 5.
1
Follow resp. country safety guidelines when using compressed air.
2
Use 99% isopropyl alcohol on surface and follow MSDS.
3
If needed, use cleaning agents. Make sure they are suitable for dissolving
the contamination without damaging the materials or coatings, follow
MSDS.
6
7
Parker Hannifin
Cylinder and Accumulator
Division Europe
Manual and Installation Guide
Manual and Installation Guide
QDC
for electrified mobile applications
QDC
for electrified mobile applications
Parker Hannifin
Cylinder and Accumulator
Division Europe