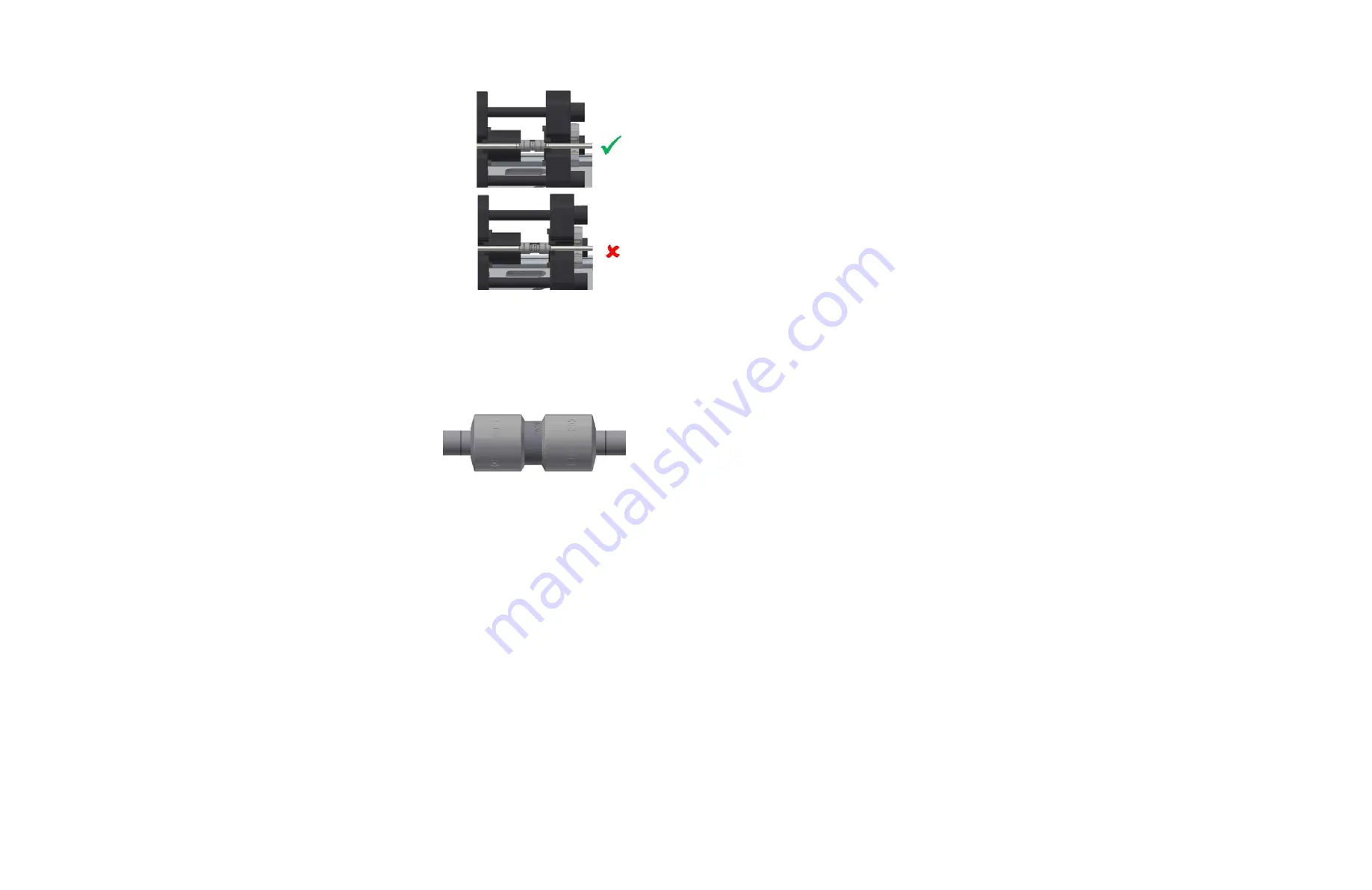
37
36
Figure 61
Figure 60
14. Ensure that the oil fill cap is unscrewed by 1 – 2 turns to
allow air to vent.
15. Press the ‘START’ button on the touch screen of the
controller.
16. Once the ‘START’ button is pressed, the pump will
automatically start, actuating the tool to traverse the
moving jaw and permanently assemble the Phastite
®
connector.
17. The pump will automatically shut-off on complete
assembly of the Phastite
®
connector. However, it is good
practice to WATCH FOR METAL-TO-METAL CONTACT.
Metal-to-metal contact is achieved when the Phastite
®
collar and body are touching (Figure 60).
18. Once the pump has shut-off the moving jaw will retract
automatically. The Phastite
®
connection can now be
removed from the tool by pulling.
19. Inspect the assembled Phastite
®
connector and tubing
for correct assembly and tube insertion:
a. Only one tubemarker line should be visible at each
end of the connection (Figure 61). If two lines are
visible and there is metal-to-metal contact, then a
new connection (new connector and new tubing) is
needed.
b. Check for metal-to-metal contact (visual). If there is
no metal-to-metal contact, then a new connection
(new connector and new tubing) is needed.
20. If a termination connector is being installed, ensure that
the collar rotates freely around the tube. A slight tap may
be required to allow collar movement. Ensure sealing
sleeve cone is protected from damage. Tighten the
collar onto the connector, until the collar abuts fully with
the body. Tighten the nut until metal-to metal contact is
achieved between body and nut.
When the tool and mains operated pump are ready to be packed away ensure that the tool’s moving jaw is fully
retracted before removing the battery from the pump.
a. Unplug the pump’s power lead from the mains.
b. Tighten the oil fill cap to stop the pump from leaking hydraulic oil when in transit or storage.
c. Next disconnect the hose from the tool and pump via the quick connects. It is normal to experience slight
weeping of hydraulic oil during disconnection. Re-apply the dust caps to all quick connects.
d. Remove the inserts from the tool jaws and return them to their aperture in the tool travel case.
e. Return the tool, hose and pump to their respective apertures in the tool and pump travel cases.
f. All travel cases should always be stored and transported in the upright position.
If an emergency or error is identified by the operator, the following actions will stop the process;
ACTION >
Press the stop button in the bottom /right corner of the controller.
EFFECT >
The pump stops instantly, the moving jaw instantly begins to retract. The pressire is instantly relieved from
the system.
Alternatively
ACTION >
Switch off the mains supply at the power outlet.
EFFECT >
The pump stops instantly, the moving jaw instantly begins to retract. The pressire is instantly relieved from
the system.
Summary of Contents for Phastite PH-10-4N-TMS
Page 1: ...Phastite Tube Connectors Installation Manual BULLETIN 5909...
Page 33: ...41 42 Notes Notes...
Page 34: ......