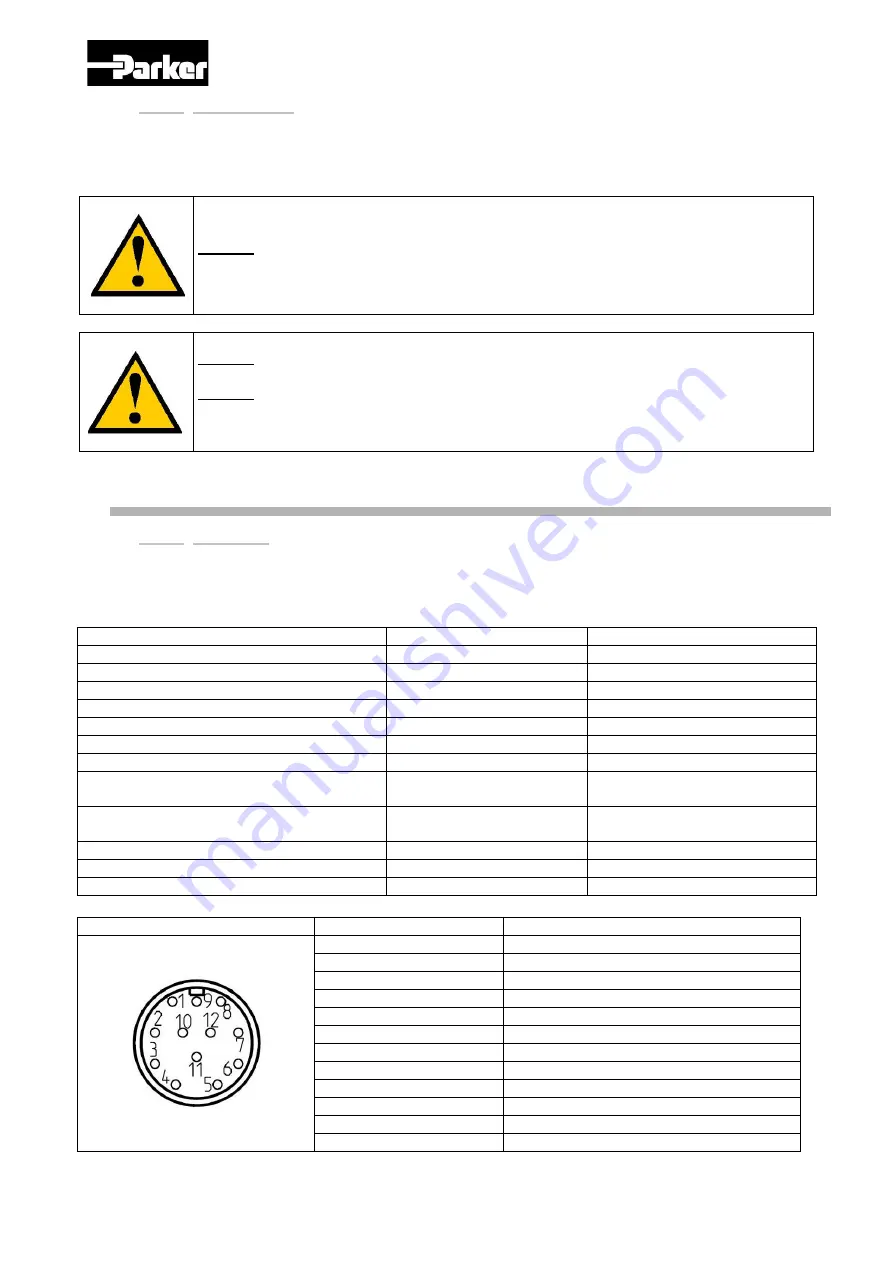
31 - PVD 3661 MGV_ commisionning manual_March 2012.docx
3.8.5.
The electrical connection on MGV motor is realized by high performance cable. The motor cable section
depends on the motor current level. Please refer to the outline drawing to know the cross section (depending of
torque/speed characteristics letter code).
Motor cable
Caution:
The motor cables are designed for high current density, so cable surface can
reach or exceed 100°C.
Caution: The wiring must comply with the drive commissioning manual and with the
recommended cables.
Caution:
Section motor cable is lower than commissioning section cable between motor and
drive due to high performance motor cable design. Do not use the same cable section than
the motor ones.
3.9. Feedback system
3.9.1.
A resolver determines the rotor position.
Resolver
Its signals are processed by the drive in order to control the stator currents, the speed and the position.
Two resolver types can be associated with the MGV: CB52 or CB102 with a connector seat.
CB52
CB102
Motor associated
MGV4 / MGV6 / MGV8
MGV9 / MGVA
Maximum speed
50 000 rpm
20 000 rpm
Number of pole
2 poles
2 poles
Feeding voltage at 8 KHz
7 Vrms
7 Vrms
Feeding current at 8 KHz
70mA maximum
70mA maximum
Precision under 7Vrms at 8KHz
+/-6’
+/-10’
Transformation ratio at 8 KHz
0.425 mini, 0.55 maxi
0.425 mini, 0.55 maxi
Input DC resistance, supply transformer
(R1-R2)
Mini 24 Ω
Maxi 26 Ω
Mini
: 15.1 Ω
Maxi : 16.2
Ω
DC stator resistance output sin (S2-S4)
output cos (S1-S3)
Mini 34.5 Ω
Maxi 37.5 Ω
Mini 57.4 Ω
Maxi 63Ω
Insulation resistance
≥ 50MΩ
≥ 50MΩ
Assembly
Direct on shaft end
Direct on shaft end
Operating temperature
-55 – +155 °C
-55 – +155 °C
Resolver connector
PIN
Signal
1
Output voltage S3 (cos-)
2
Output voltage S1 (cos+)
3
4
5
6
7
Output voltage S2 (sin+)
8
Output voltage S4 (sin-)
9
10
Input voltage R1
11
12
Input voltage R2