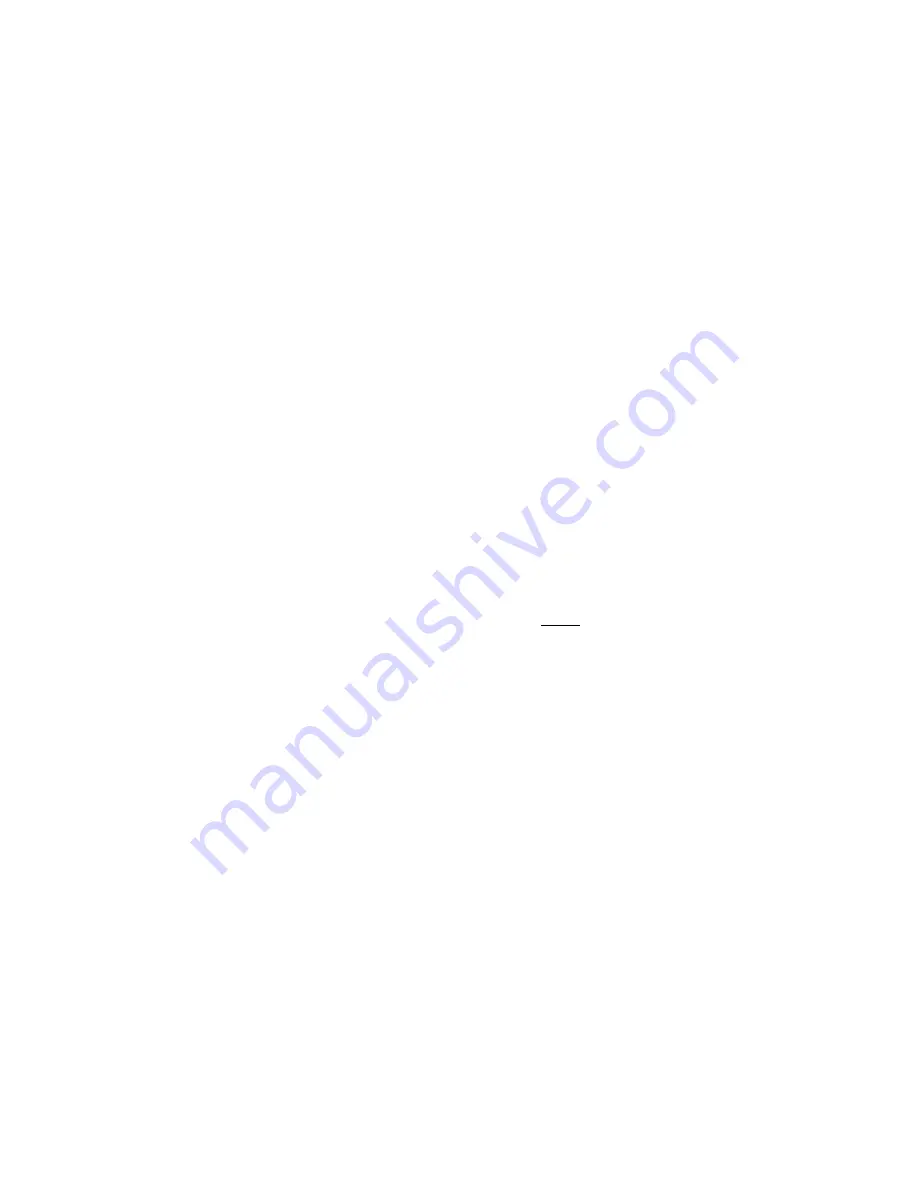
Parker Hannifin S.p.A. - Divisione S.B.C. LVD User’s Manual
50
If operating mode 15 is enabled the LVD drive performs a proportional position loop with
feed-forward; the profile generator is considered to be external and it must transmit the
information relative to the position and speed reference via CanBus in accordance with the
SBCCAN protocol (refer to the chapter
CANBUS
). If b70.1=0 feedback is provided by the
resolver, if b70.1=1 encoder feedback is adopted (X5).
Alternatively, operating mode 15 can be utilised together with the table function to create
an electronic cam. To use this function set the master modulus in steps in Pr68:69 and set the
slave points in the table in long format. Master points are considered to be equidistant and the
distance between two slave points cannot exceed 32767 steps. There can be 32 or 128 slave
points in the table (positive or negative value); when using a table with 128 points the table
cannot be saved in the eeprom memory. As the table elements are in long format, Pr43 will
point to the element corresponding to the value of parameter Pr43 divided by 2. To use a cam
profile set b70.14 to 1 for a 32 point cam or b70.15 to 1 for a 128 point cam; the first cam
point must be 0 and the last point must be 0 for a closed cam or the slave module for an open
cam. The cam function updates Pr54 and Pr60:61 and will be aborted by setting b70.14 or
b70.15 to 0. In order to stop the cam on the module, set b70.13 to 1. The master modulus
Pr68:69 cannot be modified during the cam execution. The encoder master must be connected
to the X5 input; if b70.9 is set, the parameter Pr51 define the speed of a virtual master.
OPERATING MODE 15 PARAMETERS
Pr50
Maximum speed
. Unit=rpm, default=3000, range=0..9000. This parameter makes it
possible to limit the maximum motor speed requested by the position loop. The limit
does not, however, affect feed-forward speed.
Pr51
Virtual master.
Default=0, range=0..20000. If b70.9 is set, this parameter define the
speed of a virtual master for the electronic cam. Set the value of Pr51 using the
following formula:
Pr 51
524288
234375
=
⋅
speed
rpm
Pr52
CanBus commands
(refer to the chapter
CANBUS
).
Pr53
CanBus status
(refer to the chapter
CANBUS
).
Pr54
Speed feed-forward
. Unit=rpm, default=0, range=0..
±
9000. The value of this
parameter is summed to the position loop output to obtain the speed request Pr6.
Pr55
Speed
f
eed-forward via CanBus
. This is the feed-forward value received via
CanBus; when the SYNC is received (Pb70.8=1) Pr55 is copied into Pr54 and
becomes active.
Pr56
Servo-error window
. Unit=steps, default=100. If the absolute value of the position
error exceeds the value set in Pr56, b70.5 is set to 1. If b70.5 is utilised, it must be
reset by the user following servo-errors, e.g. by means of the PLC program.
Pr57
Proportional gain of the position loop
. Default=100, range 0..32000.
Pr58
Feedback multiplication factor
. Default=1, range=-32000..+32000. With this
parameter and with Pr59 the encoder feedback pulses/revolution can be standardised
to 4096.
Pr59
Feedback division factor
. Default=1, range=-32000..+32000. With this parameter
and with Pr58 it is possible to standardise the pulses/revolution of the encoder
feedback to 4096.
Pr60:61 Position loop reference
. Unit=steps.
Pr62:63 Motor position
. Unit=steps; increases by 4096 steps each revolution.
Pr64:65 Position reference via CanBus
. This is the position reference received via CanBus,
on receipt of the SYNC (Pb70.8=1) Pr64:65 will be copied into Pr60:61 and become
active. If the cam function is utilised, this parameter is reserved.