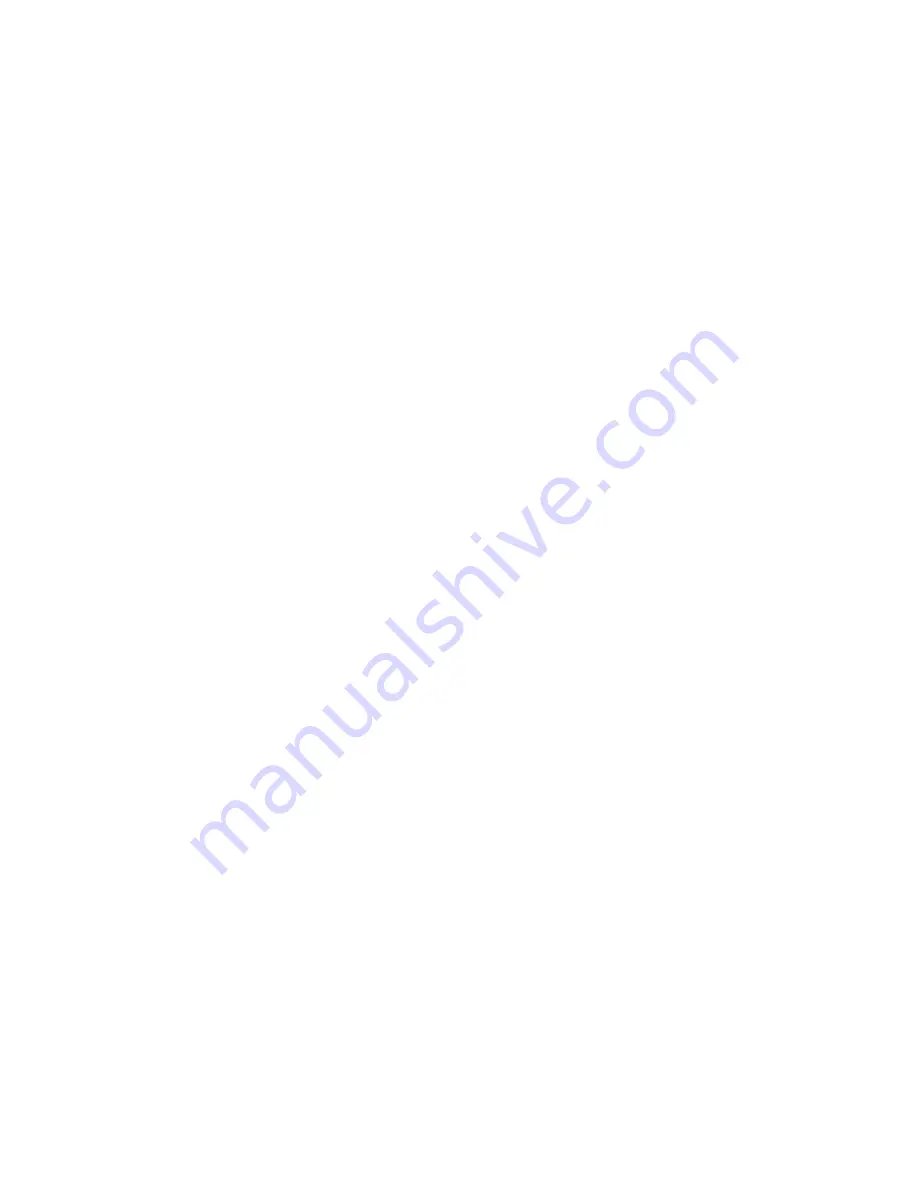
Parker Hannifin S.p.A. - Divisione S.B.C. LVD User’s Manual
45
OPERATING MODE 9 PARAMETERS
Pr50
K multiplication factor for input pulses
. Default=1. If b70.9=1 pulses on the
frequency/sign input will be multiplied by Pr50 and the result will be summed to
Pr64:65. The frequency input direction signal must be forced to a fixed level. Refer
to the chapter
Frequency input connection
for connection diagrams
.
Pr51
Acceleration time
. Unit=s/krpm, range=0.002..30.000, resolution=0.001s,
default=0.500 s. This is the acceleration ramp that will be utilised during the
positioning profile.
Pr52
Steady state speed
. Unit=rpm, range=0..9000, default=1000, absolute value. This is
the operating speed that will be utilised during generation of the position profile.
Pr56
Servo-error window
. Unit=steps, default=100. If the absolute value of the position
error exceeds the value entered in Pr56, bit b70.5 is set to 1. If b70.5 is utilised, it
must be reset by the user following servo-errors, e.g. by means of the PLC program.
Pr57
Proportional gain of the position control loop
. Default=100, range 0..32000.
Pr58
Feedback multiplication factor
. Default=1, range=-32000..+32000. With this
parameter and with Pr59 it is possible to standardise the pulses/revolution of the
encoder feedback to 4096.
Pr59
Feedback division factor
. Default=1, range=-32000..+32000. With this parameter
and with Pr58 it is possible to standardise the pulses/revolution of the encoder
feedback to 4096.
Pr60:61
Position control loop reference
. Unit=steps.
Pr62:63
Motor position
. Unit=steps; increases by 4096 steps each revolution.
Pr64:65
Incremental position
. Unit=steps. On transmission of the profile execution request
b70.8, the motor will perform Pr64:65 steps in the direction programmed in b70.4.
Pr68:69
Final position
. Unit=steps, read only parameter. When a new positioning is required,
Pr68:69 is updated with the final position.
b70.1
Feedback.
Default=0. If at zero, feedback is provided by the resolver, if set to 1,
encoder feedback is utilised (X5); in this latter case, parameters Pr58 and Pr59 are
utilised to standardise pulses/revolution to 4096.
b70.2
Incremental position reset
. Command utilised to reset Pr64:65. This command is
useful when programming incremental dimensions by means of the frequency input.
b70.3
Reserved.
b70.4
Forward / reverse
. On receipt of the start profile command (b70.8) if b70.4=0 the
motor will perform Pr64:65 steps in the positive speed direction. If b70.4=1 the same
distance will be covered, but this time in the negative speed direction.
b70.5
Servo error
. b70.5 is set to 1 if the absolute value of the position error exceeds the
value entered in Pr56. If b70.5 is utilised, it must be reset by the user following
servo-errors, e.g. by means of the PLC program.
b70.6
Feed-forward enable
. Default=0. If set to 1 feed-forward is enabled on the position
loop.
b70.7
Profile in execution
. If set to 1 the drive is executing a position profile.
b70.8
Start profile
. This is the positioning execution command.
b70.9
Frequency input enable
. Default=0. If set to 1 parameter Pr64:65 can be
programmed by means of the frequency input.
b70.10 Reset type 1
. Resets the motor position and reference. Activated only when there is
no profile in execution.
b70.11 Reset type 2
. Command to set the motor position and the reference to the absolute
position of the shaft. Activated only when there is no profile in execution.
b70.12 Reset type 3
. Command to set the reference to the motor position. Activated only
when there is no profile in execution.