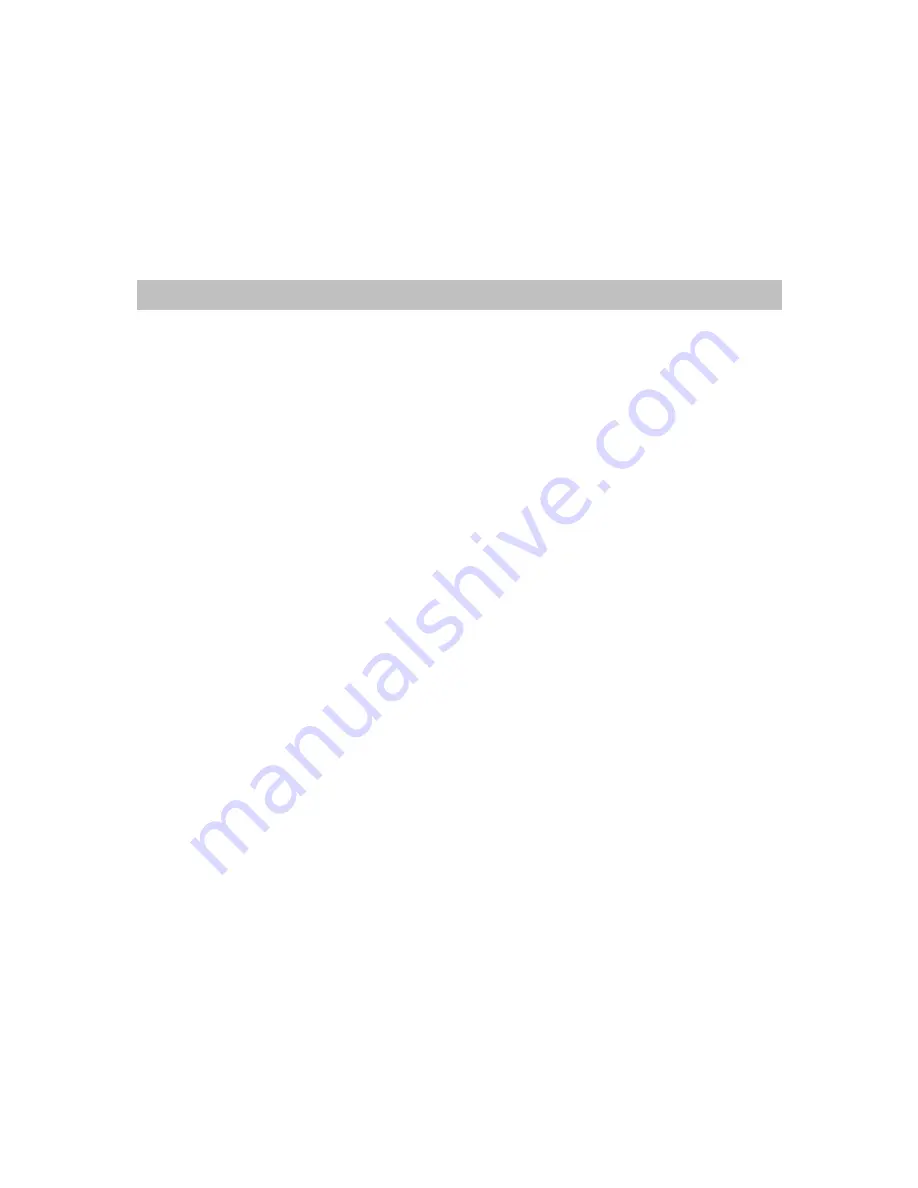
Parker Hannifin S.p.A. - Divisione S.B.C. LVD User’s Manual
47
b70.6
Feed-forward enable
. Default=0. If set to 1 feed-forward is enabled on the position
loop.
b70.8
Axis catch/release
. This bit can be set to 1 to lock, or 0 to release, the axis in relation
to the encoder reference input.
b70.9
Reserved.
b70.10 Reset type 1
. Resets motor position and reference. Activated only if b70.8=0.
b70.15
Reserved.
3.12 Stepper motor simulation
This operating mode emulates the operation of a stepper motor: each pulse received on the
frequency input (connector X5 channel A=frequency, channel B=direction) is multiplied by
Pr51 and the result is added to the reference position. The frequency input must be set up as a
direction/sign signal by setting b42.5=0. Just as in all other operating modes it is possible to
enable feed-forward, limit the action of the proportional part, obtain servo-error indication and
select the most suitable type of reset. Note that the frequency count is performed on the
negative front of the signal and a change in the direction signal must be performed at least 1
µ
S before the negative frequency front. Unlike conventional stepper motors, this system is not
subject to the risk of getting out of step. For connection diagrams refer to the chapter
Frequency input connection.
OPERATING MODE 11 PARAMETERS
Pr50
Maximum speed
. Unit=rpm, default=3000, range=0..9000. This parameter makes it
possible to restrict maximum motor speed.
Pr51
Reference multiplication factor
. Default=1, range=0...4096. This parameter can be
used to program the required multiplication ratio for the input reference frequency.
Pr56
Servo-error window
. Unit=steps, default=100. If the absolute value of the position
error exceeds the value set in Pr56, b70.5 is set to 1. If b70.5 is utilised, it must be
reset by the user following servo-errors, e.g. by means of the PLC program.
Pr57
Proportional gain of the position loop
. Default=100, range 0..32000.
Pr60:61 Position loop reference
. Unit=steps.
Pr62:63 Motor position
. Unit=steps; increases by 4096 steps each revolution.
b70.5
Servo error
. b70.5 is set to 1 if the absolute value of the position error exceeds the
value entered in Pr56. If b70.5 is utilised, it must be reset by the user following
servo-errors, e.g. by means of the PLC program.
b70.6
Feed-forward enable
. Default=0. If set to 1 feed-forward is enabled on the position
loop.
b70.8
Axis catch/release
. This bit can be set to 1 to lock, or 0 to release, the axis in relation
to the encoder reference input.
b70.9
Reserved.
b70.10 Reset type 1
. Resets motor position and reference.
b70.11 Reset type 2
. Sets motor position and reference to the absolute position of the shaft.
b70.12 Reset type 3
. Sets the reference to the motor position.