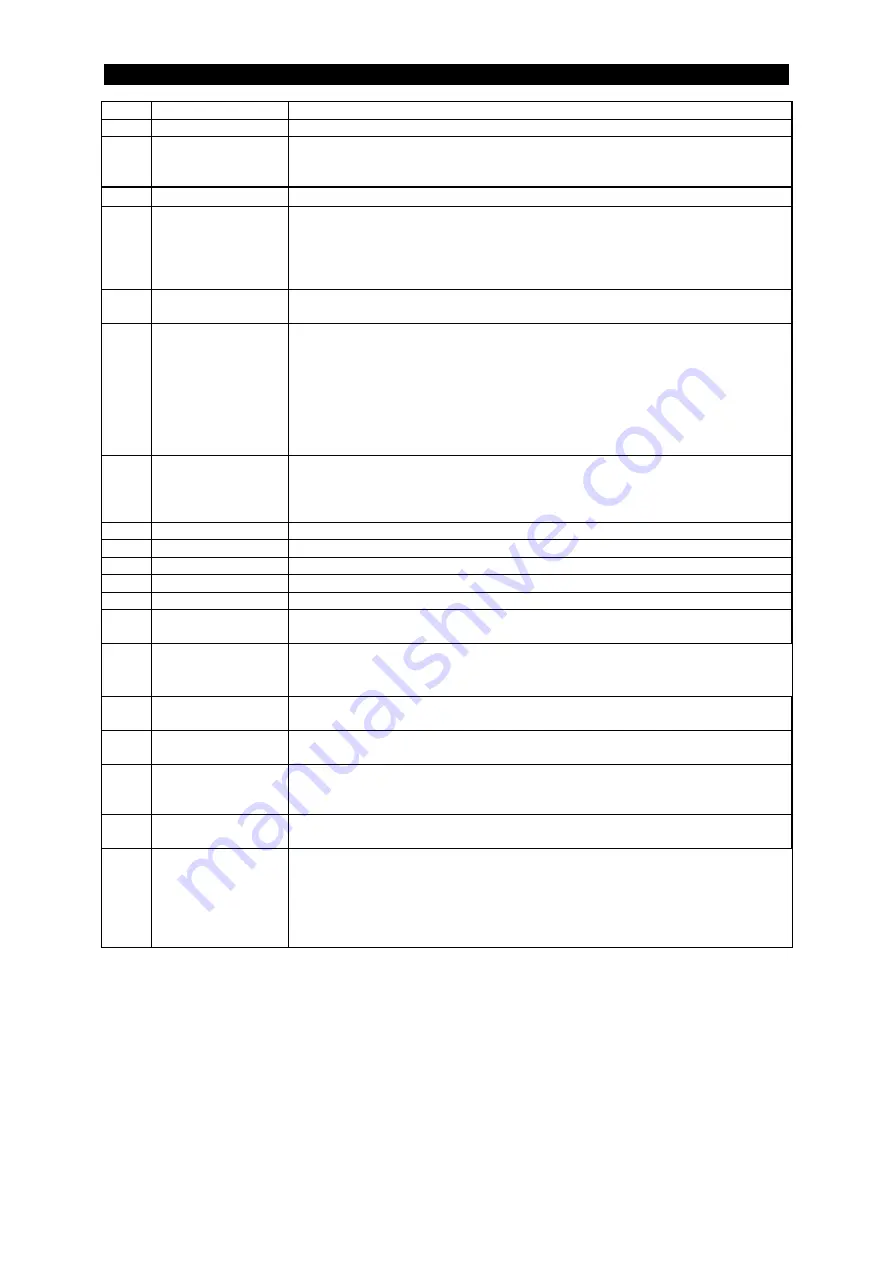
Parker Hannifin S.p.A. – S.B.C. Division
quick installation guide Hi-drive
Page 11 of 12
12 Alarms
Pr23 Alarm
Remedies
0 No
alarm
1 Overvoltage
Check
the
three-phase power line.
Check the braking line and braking resistance
Check the application
2 Undervoltage
Check the three-phase power line.
3
Overcurrent
Check any mechanical impediments and correct motor size for required use.
Check motor connections and any short-circuits between phase-phase and phase-
earth.
Check the length and type of motor cable used.
Make sure a mains filter is not connected on the motor!
4
FBK speed loop
error
Check the speed loop connections and the connectors from both sides (drive-
motor).
5
Motor PTC alarm
-Check the PTC connection cable.
-If the alarm persists, disable the drive, interrupt power to the motor, disconnect
the power supply to the drive (24VDC). Disconnect the PTC connector from the
drive, and make a connection short-circuiting the PTC (between PTC+ and PTC-)
on the terminal board of the drive itself.
Power the drive (24VDC). If the alarm continues, the drive is faulty, otherwise
the PTC on board the motor is faulty (after completing the test, remove the
connection short-circuiting the PTC)
6 Power
module
overheating
Check the cooling fans and any blockages/restrictions in air flow.
Check the braking cycle.
Check the room temperature of the switchboard where the drive is fitted and
outside room temperature.
7
External alarm
Depends on application (see PicoPLC program)
8
Auxiliary alarm
Depends on application (see PicoPLC program)
10(*) Check sum PLC
Set the default parameters, save, switch back on and reprogramme the drive
11(*) Check sum param.
Set the default parameters, save, switch back on and reprogramme the drive
15
Default parameters
Set the default parameters, save and switch back on
21 24VDC
undervoltage
The drive power voltage is below minimum threshold: voltage too low.
22 Environment
overheating
Check the cooling fans and any blockages/restrictions in air flow.
Check the room temperature of the switchboard where the drive is fitted and
outside room temperature.
24 Braking
transistor
cutout
Braking resistance in short circuit. If an external braking resistance is connected
to the drive, check its condition and wiring harness.
25(**) Wrong FBK speed
loop initialisation
Check the FBK speed settings.
Check the FBK speed connection.
26(**) Wrong FBK
position loop
initialisation
Check the settings of the position FBK.
Check the connection of the position FBK.
28 FBK
position
loop
error
Check the connections of the position loop and the connectors on both sides
(drive-motor).
I
2
T Current
restriction
(I
2
T) - “the red LED
flashes
continuously”
The drives goes in I²T due to an overload (more power is required than that being
supplied). Check:
-The wiring between the drive and the motor (there must be no switched-over
phases). Above all mind the motors with terminal board rather than connector: it
is easy to make a mistake. Make sure you keep to the wiring diagrams.
- Mechanical sizing
(*) only reset after default loading and new saving.
(**) cannot be reset until next switch-on.
ISBN0411301550