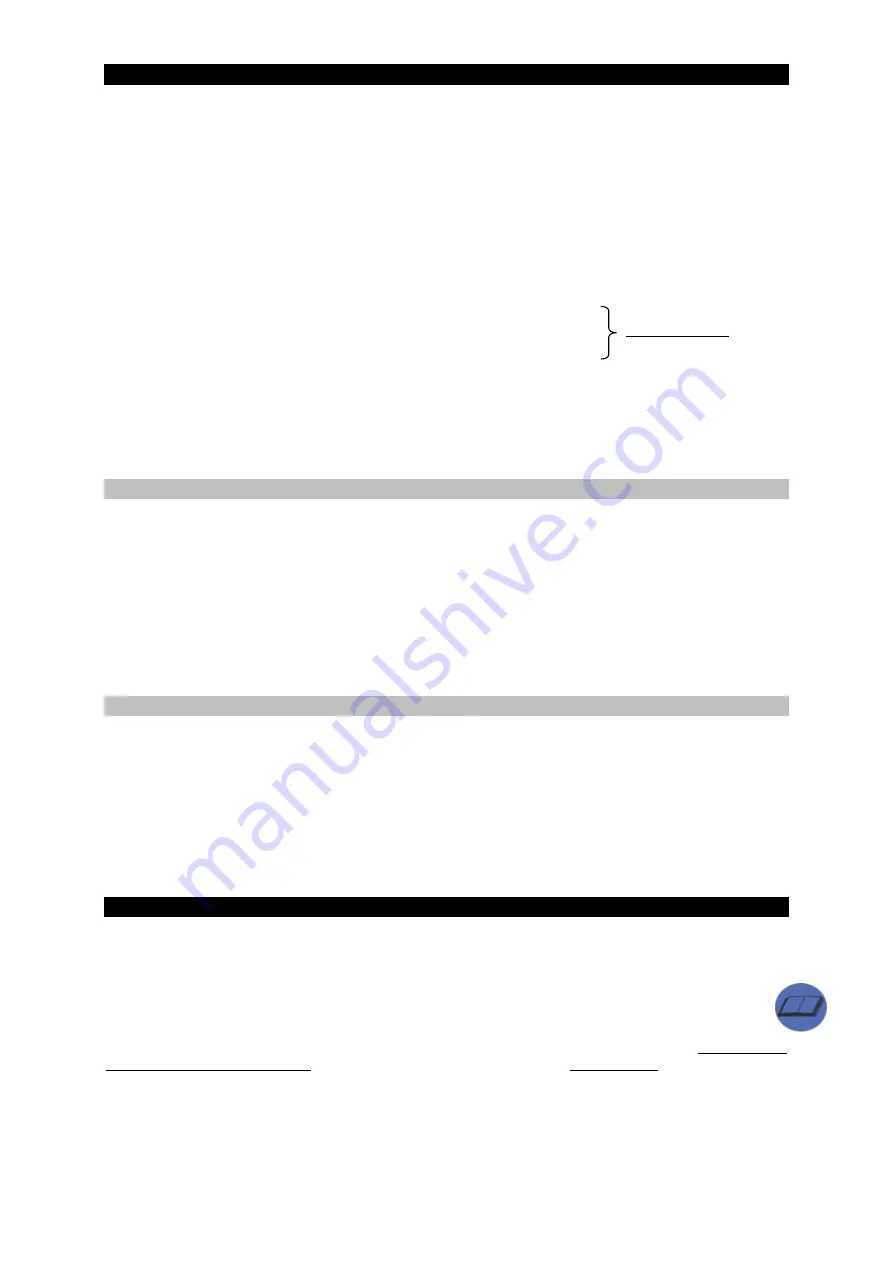
Parker Hannifin S.p.A. – S.B.C. Division
quick installation guide Hi-drive
Page 10 of 12
10 FIRST CONVERTER START-UP
The drive is supplied from the factory with default programming.
Remember that the Hi-drive can control brushless synchronous or asynchronous motors. Before entering the
motor data, programme
Pr31
: write “
0
” for brushless motor (default condition), “
1
” for asynchronous motor.
At this point the mechanism must be set with the fundamental parameters to characterise the connected motor
(motor plate data). The fundamental parameters are:
Pr29
Number
of
motor
poles
N
Pr32
nominal
motor
speed
r.p.m.
Pr33
rated motor current (eg. 2.5A, write 2.5)
A
Pr46
motor phase-phase resistance (eg. 1.8
Ω
, write 1.8)
ohm
Pr47
motor phase-phase inductance (eg. 2.6mH, write 2.6)
mH
Pr60
number
of
resolver
poles
N
In the case of an asynchronous motor, the previous data must be completed with the following parameters:
Pr45
basic
speed
r.p.m.
Pr48
sliding
r.p.m.
Pr49
magnetisation
current
A
Pr32
limit
speed
of
motor
r.p.m.
After setting the parameters for motor characterisation, the operator must give the data saving command,
Pb42.15
(with drive disabled) and start the mechanism again. The drive will calculate the correct values of Pr2,
Pr3, Pr16, Pr17, Pr18 and Pr19. The gain calculation is done if the drive is in default condition.
To change the entered parameters, put bit
Pb42.1
=1. The drive, at this point, again asks for the default
parameters (alarm 15). After data entering, save and start the drive again. The parameters Pr2, Pr3, Pr16, Pr17,
Pr18 and Pr19 will be recalculated according to the entered values.
10.1
First Hi-drive start-up
Below, the steps are shown to be carefully followed during first converter start-up.
1)
Connect the motor to the converter, carefully following the manual diagrams.
2)
Make sure the converter is disabled.
3)
Start the converter.
4)
Make sure no alarm has tripped.
5)
Set the analogue reference at 0 V (pin 13, 14 of terminal board X5), and enable the converter (24V at the
pin that enables the drive).
6)
Now the motor shaft must be stopped; when the analogue reference voltage changes, the motor speed
must change proportionately. If it does not, check the wiring harness.
The converter is made with default values already set.
10.2
Setting the default parameters
To set the default parameters (which change all previously set parameters) proceed as follows:
- start the converter
- disable the converter by means of software command (
Pb40.9=0
) or via hardware (before starting the
converter)
- set
Pb39.13=0
- give the command
Pb42.12=1
, which enables drive default parameter loading
- enter the fundamental parameters (motor plate data, see para. 3.2)
- save the setting with commands
Pb42.14
e
Pb42.15
(the drive must be disabled)
- stop and start the drive again.
11 USE OF KEYBOARD (OPTIONAL)
S
, SHIFT, is used in combination with the other keys to enable the cursor to move inside the fields:
o
Together with key T, movement inside the fields is made in the opposite direction (anticlockwise).
o
Together with key + o – to move the cursor inside the field on a figure with greater or less "weight".
+
, increases the datum shown by the cursor; if PLC instructions.
–
, decreases the datum shown by the cursor; if PLC instructions.
T
, the purpose of this key is to change the field shown by the cursor.
E
, ENTER, confirms datum entering or change. The changed or entered datum or instruction must be saved
before changing the display page, otherwise the change made will be lost. IMPORTANT: the instructions can
also be changed when the Pico-PLC is running (Pr39.13=1), and so before changing anything, it is best to stop
the Pico-PLC.
Asynchronous motor