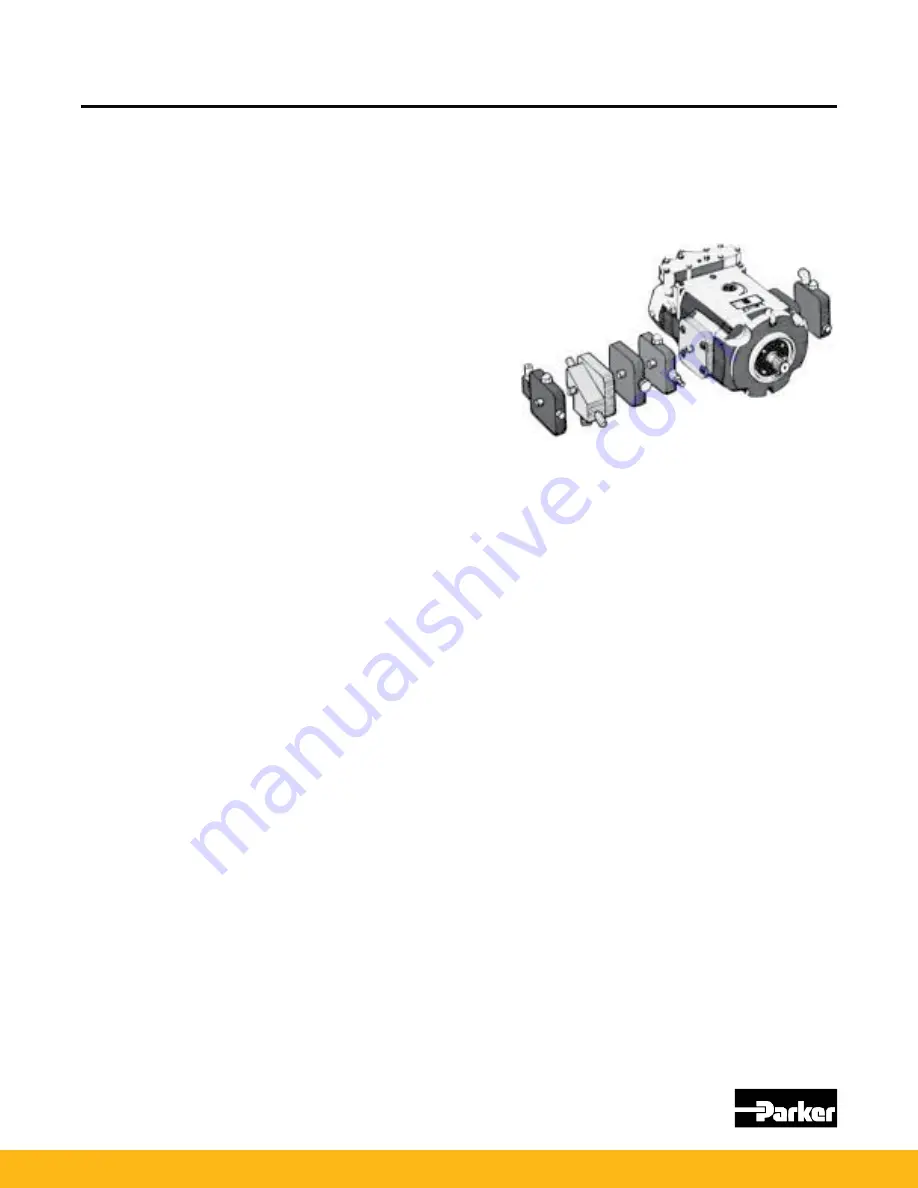
HY28-2668-01/GC/NA,EU
GOLD CUP
®
Series - Application Manual
Piston Pumps & Motors
3.1
Parker Hannifin Corporation
Hydraulic Pump Division
Marysville, Ohio USA
Section 3
The spring centered rotary servo input, pressure compensator override, and displacement in-
dicator are all standard features on all GOLD CUP
®
package pumps. Spring centering is used
in addition to the rotary servo input control to provide a positive return-toneutral action. It in-
cludes an adjustable neutral position to allow fine tuning the neutral position, or offsetting the
neutral position. Variable motors have spring offset rotary servo inputs, cylinder controls and
displacement indicators as standard features. Additional, optional controls are available which
increase the utility of the GOLD CUP
®
components. These controls include the following:
s !DJUSTABLEDISPLACEMENTSTOPS
s -ANUALSCREWADJUSTMENT
s !UTOMATICBRAKEANDNEUTRALBYPASSCONTROL
s 4ORQUELIMITOVERRIDE
s (YDRAULICSTROKER
s %LECTROHYDRAULICSTROKER
s %LECTROHYDRAULICSERVO
s #YLINDERCONTROL
s %LECTROHYDRAULICCYLINDERCONTROL
Adjustable stops are available as an option. They provide an adjustment to limit the maximum
displacement of the rotary servo input between zero and full displacement on both sides of
center.
A manual screw adjustment is available to provide an easily set pump displacement which will
not move during operation. It is used when pump displacement will be adjusted infrequently.
The automatic brake and neutral bypass control is used to actuate a spring set pressure
released parking brake and open a small channel between the system ports when the rotary
servo input and rocker cam are coincident in the neutral position. If one or the other device is
not in the neutral position, the control will not shift into the brake and bypass mode. This con-
trol is used on track drives, swing drives, hoist drives and any other system where creeping is
intolerable. In some cases this control may be used for the bypass function alone.
The torque limit override control is used for limiting the input shaft torque. At constant speeds
it serves as a horsepower limit override. This control maintains a relationship between dis-
placement and pressure which results in a limitation of the input torque. At torque levels below
the set value the pump follows the input rotary servo normally, but if pressure or displacement
(or both) increase to a value which results in torque higher than set by the control, the pump
will destroke to limit the input torque. Because this control works with displacement instead of
flow, the horsepower setting varies directly with shaft speed.
The hydraulic stroker is used on both pump and motors. This control positions the rotary servo
proportionally to externally controlled pilot pressure.
The electrohydraulic stroker is used on both pumps and motors. It provides an input rotary
servo position proportional to input current. It is used primarily with remote electrical control-
lers. It may be used with programmed controllers as long as the system does not require rapid
response. Presently, there are two versions available, the 500 and 900 series.
The electrohydraulic servo provides a control for electrohydraulic systems requiring rapid re-
sponse and precise control. RVDT feedback or Potentiometer feedback are available options.
The three position cylinder control permits a pump to be offset to an adjustable displacement
on either side of center by supplying a pilot signal to the appropriate control port. With no
signal the pump returns to an adjustable zero stroke position.
The two position pump cylinder control permits a pump to be offset to an adjustable displace-
ment on one side of center by supplying a pilot signal to the appropriate control port. With no
signal the pump returns to an adjustable zero position.
The two position motor cylinder control permits a motor to be stroked to a reduced displace-
ment by supplying a pilot signal to the appropriate control port. With no signal the motor
returns to an adjustable maximum stroke position.
By mounting an electric directional control valve on the cylinder control, the pump or motor
stroke may be controlled by energizing the appropriate solenoid valve, eliminating the need
for separate mounting and fluid connections to the control valve.
GOLD CUP
®
CONTROLS
Adjustable displacement stops
Manual screw adjustment
Automatic brake and neutral bypass
control
Torque limiter override control
Hydraulic stroker
Electrohydraulic stroker
Electrohydraulic servo
Three position cylinder control
Two position cylinder control
Two and three position cylinder
control with integrally mounted
electric directional control valve
include the following:
ops
al
www.comoso.com