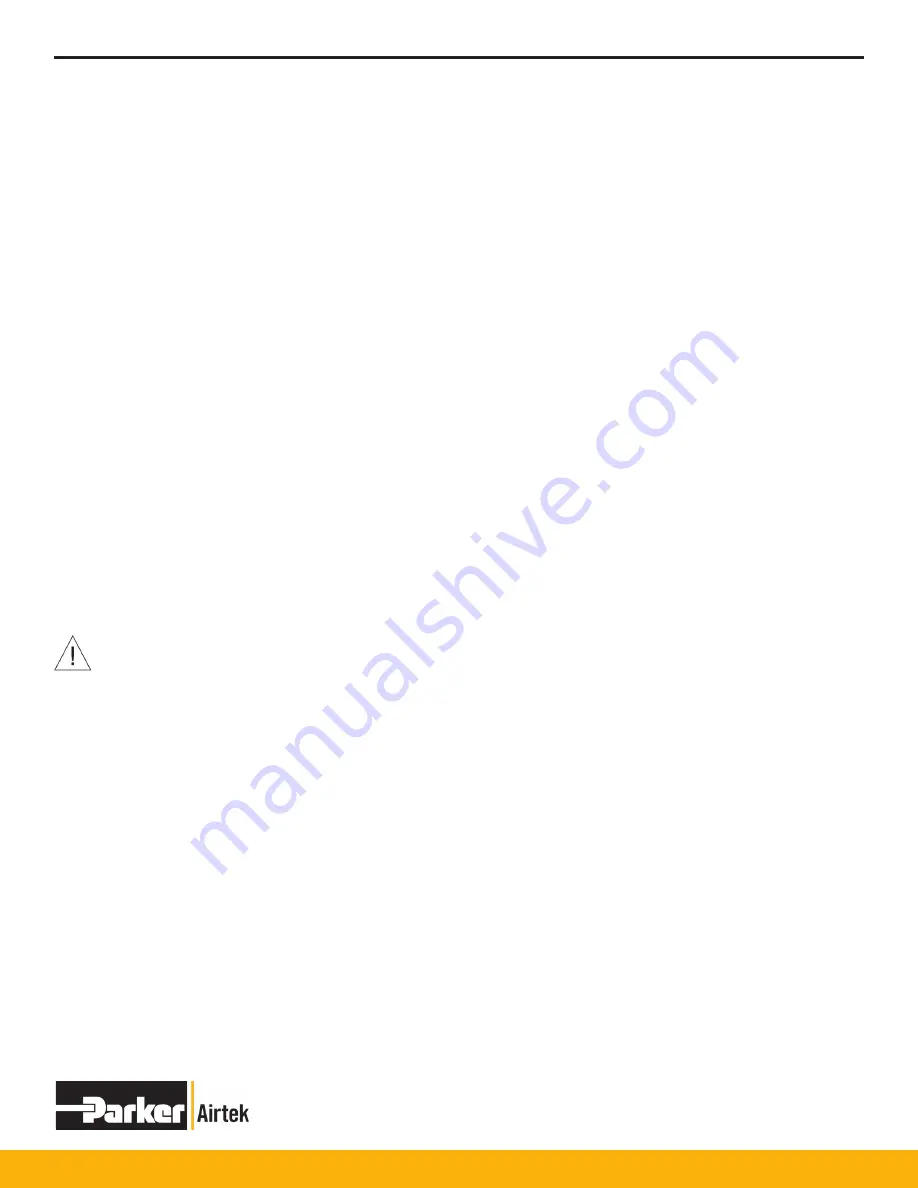
TWP/TWB200 – TWP/TWB9000
52
SHUT DOWN
The dryer should be sufficiently cooled down and allowed to repressurize before shutting down. Allow dryer to run
normally or use the manual stepping feature to proceed to the cooling stage and wait for cooling to end. After the
regenerating tower has sufficiently cooled down, place the dryer into STANDBY.
If the dryer is operating in the heatless backup mode of operation, place the dryer immediately into stand by.
Wait for the dryer to repressurize, then push the emergency stop button and open the main electrical disconnect.
Once the dryer is in STANDBY, the EMERGENCY STOP button can then be used to remove power from the valves,
the heater, and the blower. Open the main electrical disconnect to completely remove power from the dryer.
To put dryer into STANDBY, press the SWITCH TO STANDBY button on the display. The GOING TO STANDBY
message will appear on the screen. If pressed during the heating cycle, the dryer will proceed to cooling for two
minutes. Once the dryer repressurizes, the status message will change to read DRYER IN STANDBY. Both tanks
will be pressurized and the heater will remain off. To restart, press the DRYER IN STANDBY button on the display.
The regeneration cycle will immediately resume at the point in the regenerating process where the stand by button
was first pressed.
To depressurize the dryer, first follow the appropriate shutdown procedure. Open the dryer bypass valve.
Close the outlet isolation valve, and then the inlet isolation valve.
Open the manual drain valve on the afterfilter or control air filter to allow full depressurization of the dryer.
Verify all pressure is removed from equipment and power is disconnected before servicing.
If a dewpoint sensor is installed and the dryer will be out of service for an extended period of time, remove the
sensor and place in a safe, dry location. The sensor will be damaged if exposed to prolonged periods of saturated
conditions.
The dryer should be immediately bypassed to prevent loading the desiccant beds while the dryer is out of service.
MAINTENANCE
Use caution when near the dryer and wear eye protection. Hearing protection is recommended. Dryer maintenance
should only be performed by trained personnel. Always shutdown the dryer, relieve all pressure, and disconnect
power before servicing.
Consult service manual for additional information on part replacement.
Daily
Check the dewpoint of the compressed air system to ensure it is in good operating condition.
Check drain for proper function. Ensure drain is not clogged.
Check purge pressure setting (TWP only), proper prefilter drain operation, and verify no back pressure on regenerat-
ing vessel to avoid more serious operating issues.
Check for proper heater and desiccant bed temperatures.
Check controller for any active alarms.
Summary of Contents for Airtek TWB1000
Page 1: ...1 Externally Heated Blower Purge Desiccant Dryers User Manual Models TWP TWB200 TWP TWB9000...
Page 9: ...TWP TWB200 TWP TWB9000 9 TWP Desiccant Dryer Operation TWB Desiccant Dryer Operation...
Page 10: ...TWP TWB200 TWP TWB9000 10 FLOW SCHEMATIC MODELS TWP200 300 DWG FS11682 Rev...
Page 11: ...TWP TWB200 TWP TWB9000 11 FLOW SCHEMATIC MODELS TWP400 800 DWG FS11683 Rev...
Page 12: ...TWP TWB200 TWP TWB9000 12 FLOW SCHEMATIC MODELS TWP1000 1500 DWG FS11684 Rev...
Page 13: ...TWP TWB200 TWP TWB9000 13 FLOW SCHEMATIC MODELS TWP2000 9000 DWG FS11685 Rev...
Page 14: ...TWP TWB200 TWP TWB9000 14 FLOW SCHEMATIC MODELS TWB200 800 DWG FS11686 Rev...
Page 15: ...TWP TWB200 TWP TWB9000 15 FLOW SCHEMATIC MODELS TWB1000 1500 DWG FS11687 Rev...
Page 16: ...TWP TWB200 TWP TWB9000 16 FLOW SCHEMATIC MODELS TWB2000 9000 DWG FS11688 Rev...
Page 17: ...TWP TWB200 TWP TWB9000 17 WIRING DIAGRAM STANDARD CONTROLLER...
Page 18: ...TWP TWB200 TWP TWB9000 18 WIRING DIAGRAM STANDARD CONTROLLER...
Page 19: ...TWP TWB200 TWP TWB9000 19 WIRING DIAGRAM STANDARD CONTROLLER...
Page 20: ...TWP TWB200 TWP TWB9000 20 WIRING DIAGRAM STANDARD CONTROLLER...
Page 21: ...TWP TWB200 TWP TWB9000 21 PANEL LAYOUT STANDARD CONTROLLER...
Page 38: ...TWP TWB200 TWP TWB9000 38 Service Screen...
Page 71: ...TWP TWB200 TWP TWB9000 71...