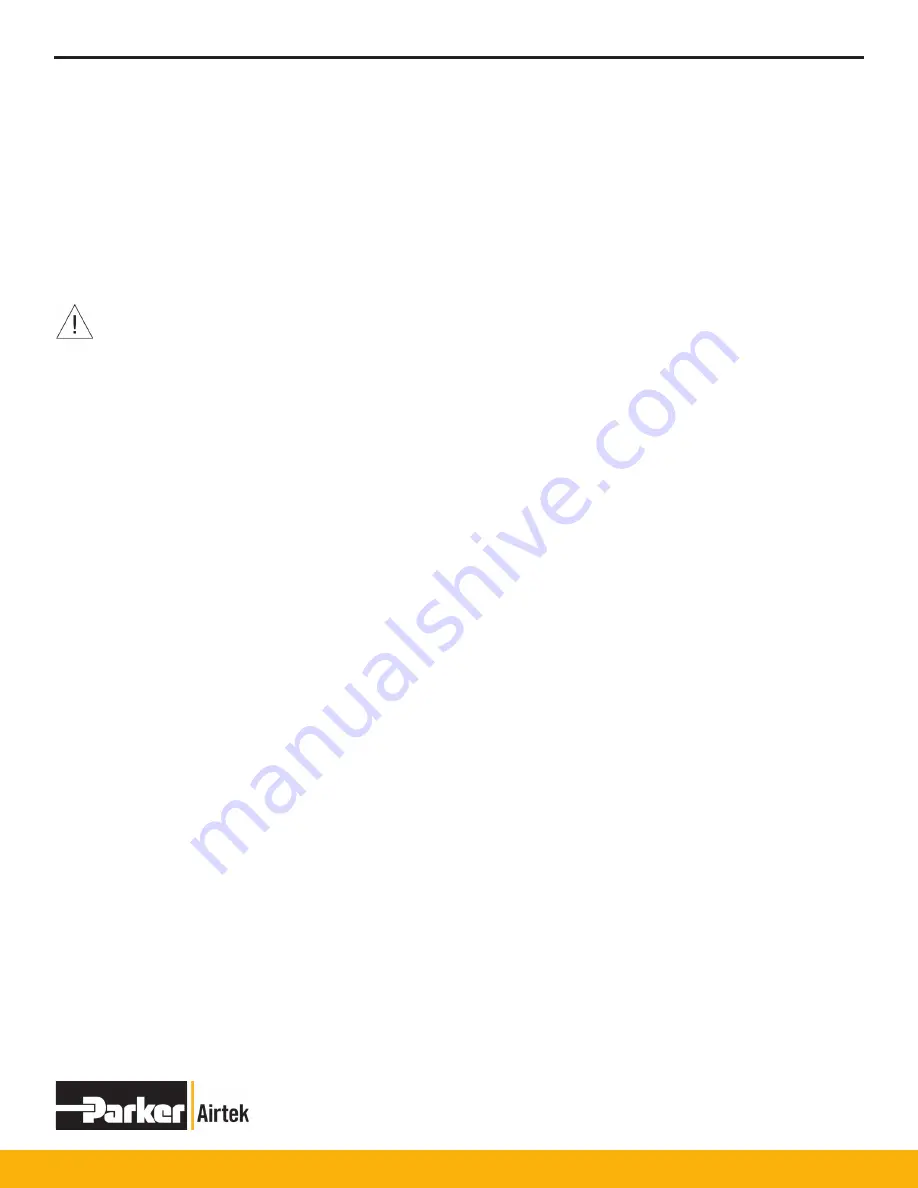
TWP/TWB200 – TWP/TWB9000
22
START UP
Verify all piping and electrical connections are secure. Do not power the dryer at this time.
Start the compressor and pressurize the air system, bypassing the dryer.
Slowly
pressurize the dryer by opening the inlet isolation valve. It is important to allow the dryer to slowly
pressurize to prevent fluidization of the desiccant bed. Rapid pressurization can also cause damage to the
vessel internal screens and filter elements.
The dryer must be started without the mufflers installed. This will expedite removal of excess desiccant dust and
prevent premature clogging of the mufflers.
CAUTION: USE EAR AND EYE PROTECTION WHEN OPERATING THE DRYER WITHOUT MUFFLERS. EXCESSIVE
NOISE WILL BE CREATED. DUST AND PARTICLES FROM THE SURROUNDING AREA MAY BECOME AIRBORNE.
OPERATION WITHOUT MUFFLERS EXCEEDS OSHA LIMITS.
Open the control air ball valve.
Push in the emergency stop button.
Power up the dryer. Check rotation of blower by pushing in contactor manually. If opposite of the flow direction
arrow, switch the two leads.
Pull the emergency button out.
Start in Heatless
- Touch the START IN HEATLESS OPERATION button from the controller’s SERVICE screen to
start the dryer. The dryer will initially ensure that vessels are pressurized, then will begin by blowing down one
of the vessels while placing the opposite ‘drying’ vessel online. If you do not want the dryer to begin cycling
automatically, close the control air ball valve. This will prevent the inlet and exhaust valves from switching. In this
situation, a bad blowdown alarm will occur which must be reset from the control panel after re-opening the control
air ball valve.
The dryer can be run in the heatless mode for two or three cycles to quickly remove desiccant dust caused by
shipping or filling the unit. This also serves to verify that the vessels are switching normally, and to allow resolving
any issues with system pressure before applying heat the regeneration process.
Switch to Heated
- When you are ready to switch the dryer to HEATED regeneration operation, simply touch the
START IN HEATED OPERATION button from the controller’s Service screen. The dryer will immediately repressurize,
then switch towers and start HEATED regeneration on the opposite vessel.
Install the exhaust mufflers on the dryer.
Check Purge Pressure
- For TWP dryers, verify the purge pressure setting is correct for the operating conditions.
The purge pressure setting must be set to the factory advised setting while using the dewpoint demand feature.
The purge pressure must be set while in the Heated Regeneration State. Do not adjust the purge pressure when
operating in the heatless backup timing configuration.
Heating
- Verify that the heater contactor(s) pull in and the purge air temperature value on the controller screen
begins to rise. If the dryer is blower type, then the blower will also be running at this time.
Over-Temp
- There is a redundant over-temperature module inside the control cabinet that is preset at the factory to
650°F. This module monitors a thermocouple for purposes of independently sensing an over-temperature condition.
In addition, there is an over-temp setting, also preset the factory to 650°F, accessed from the ADVANCED SETTINGS
screen on the controller. This setting is associated with the purge temperature sensor.
Summary of Contents for Airtek TWB1000
Page 1: ...1 Externally Heated Blower Purge Desiccant Dryers User Manual Models TWP TWB200 TWP TWB9000...
Page 9: ...TWP TWB200 TWP TWB9000 9 TWP Desiccant Dryer Operation TWB Desiccant Dryer Operation...
Page 10: ...TWP TWB200 TWP TWB9000 10 FLOW SCHEMATIC MODELS TWP200 300 DWG FS11682 Rev...
Page 11: ...TWP TWB200 TWP TWB9000 11 FLOW SCHEMATIC MODELS TWP400 800 DWG FS11683 Rev...
Page 12: ...TWP TWB200 TWP TWB9000 12 FLOW SCHEMATIC MODELS TWP1000 1500 DWG FS11684 Rev...
Page 13: ...TWP TWB200 TWP TWB9000 13 FLOW SCHEMATIC MODELS TWP2000 9000 DWG FS11685 Rev...
Page 14: ...TWP TWB200 TWP TWB9000 14 FLOW SCHEMATIC MODELS TWB200 800 DWG FS11686 Rev...
Page 15: ...TWP TWB200 TWP TWB9000 15 FLOW SCHEMATIC MODELS TWB1000 1500 DWG FS11687 Rev...
Page 16: ...TWP TWB200 TWP TWB9000 16 FLOW SCHEMATIC MODELS TWB2000 9000 DWG FS11688 Rev...
Page 17: ...TWP TWB200 TWP TWB9000 17 WIRING DIAGRAM STANDARD CONTROLLER...
Page 18: ...TWP TWB200 TWP TWB9000 18 WIRING DIAGRAM STANDARD CONTROLLER...
Page 19: ...TWP TWB200 TWP TWB9000 19 WIRING DIAGRAM STANDARD CONTROLLER...
Page 20: ...TWP TWB200 TWP TWB9000 20 WIRING DIAGRAM STANDARD CONTROLLER...
Page 21: ...TWP TWB200 TWP TWB9000 21 PANEL LAYOUT STANDARD CONTROLLER...
Page 38: ...TWP TWB200 TWP TWB9000 38 Service Screen...
Page 71: ...TWP TWB200 TWP TWB9000 71...