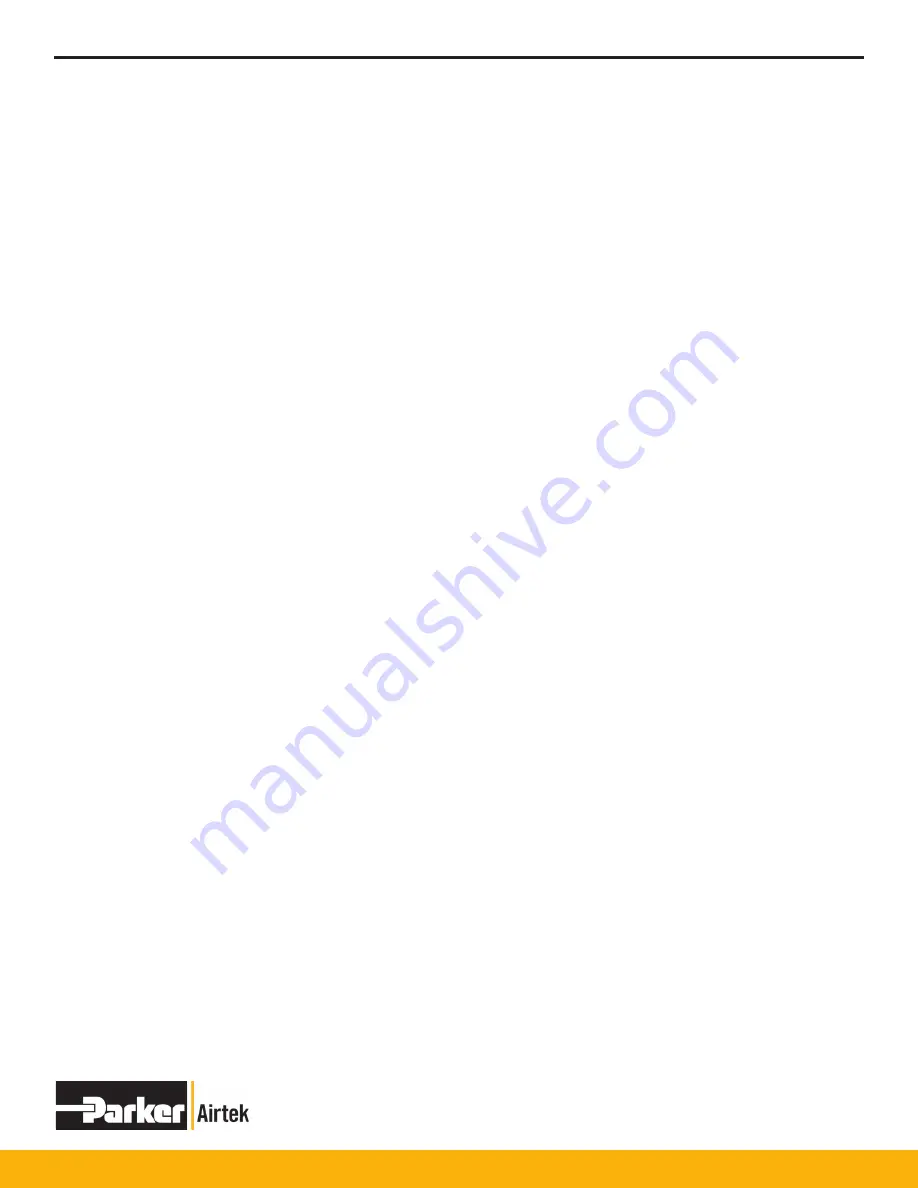
TWP/TWB200 – TWP/TWB9000
8
GENERAL OPERATION
The externally heated and blower purge desiccant dryers are designed to remove moisture in water vapor form, from
compressed air to yield dewpoints of -40°F or better. The twin tower design allows constant drying of compressed
air through one adsorption vessel while the other vessel desiccant bed regenerates by using heated dry purge air.
Compressed air is directed through the inlet valve and up through the drying desiccant vessel where moisture is
adsorbed by the desiccant. The low dewpoint dry air is then directed through the outlet check valve and down-
stream for use.
For externally heated dryers, regeneration of the saturated desiccant vessel bed is begun by blowing down the
saturated vessel bed. The quick change from line pressure to atmosphere causes moisture to detach itself from the
desiccant and be exhausted. The regeneration cycle is continued by directing 8% of the dry compressed air through
a purge valve and orifice. The purge air is expanded to atmosphere, passed across an electric resistance heater
where the air temperature is elevated to 400°F, then passed down through the saturated bed heating the desiccant.
Adsorbed moisture is released from the desiccant, and then exits the dryer through the exhaust valve and muffler.
Once heated regeneration is complete, the heater is powered off and cooling begins. Dry purge air continues to pass
through the regenerated bed, cooling it to reduce the air temperature spike downstream and allow the newly regen-
erated bed to readily adsorb moisture again after switchover.
For blower purge dryers, regeneration of the saturated desiccant vessel bed is begun by blowing down the sat-
urated vessel bed. The quick change from line pressure to atmosphere causes moisture to detach itself from the
desiccant and be exhausted. The regeneration cycle is continued by the blower pulling in ambient air and passing
this low pressure wet air across an electric resistance heater. The air temperature is elevated to 400°F, then passed
down through the saturated bed, heating the desiccant. Adsorbed moisture is released from the desiccant, and then
exits the dryer through the exhaust valve and muffler. Once heated regeneration is complete, the heater is powered
off and cooling begins. The blower continues to pass air through the regenerated bed, cooling it to reduce the air
temperature spike downstream and allow the newly regenerated bed to readily adsorb moisture again after switcho-
ver. A stream of dry purge air in the amount of 2% may also be used after blower cooling to reduce the dewpoint
spike at switchover caused by using wet ambient air with the blower.
Once regeneration is completed, the offline desiccant vessel is slowly pressurized to system pressure. The dryer is
ready for switchover, at which point compressed air will be directed though the newly regenerated desiccant bed for
drying and the opposite desiccant vessel begins regeneration. This cycle continues automatically.
The dryer inlet, exhaust, and repressurization valves are controlled by solenoid actuated control valves, which are
controlled by the dryer PLC. The PLC operates opens and closes the valves using a programmed timing sequence.
The PLC is equipped with various timing cycles to maximize the dryer efficiency. It is also possible to extend the
drying cycle time using the dewpoint demand function.
Summary of Contents for Airtek TWB1000
Page 1: ...1 Externally Heated Blower Purge Desiccant Dryers User Manual Models TWP TWB200 TWP TWB9000...
Page 9: ...TWP TWB200 TWP TWB9000 9 TWP Desiccant Dryer Operation TWB Desiccant Dryer Operation...
Page 10: ...TWP TWB200 TWP TWB9000 10 FLOW SCHEMATIC MODELS TWP200 300 DWG FS11682 Rev...
Page 11: ...TWP TWB200 TWP TWB9000 11 FLOW SCHEMATIC MODELS TWP400 800 DWG FS11683 Rev...
Page 12: ...TWP TWB200 TWP TWB9000 12 FLOW SCHEMATIC MODELS TWP1000 1500 DWG FS11684 Rev...
Page 13: ...TWP TWB200 TWP TWB9000 13 FLOW SCHEMATIC MODELS TWP2000 9000 DWG FS11685 Rev...
Page 14: ...TWP TWB200 TWP TWB9000 14 FLOW SCHEMATIC MODELS TWB200 800 DWG FS11686 Rev...
Page 15: ...TWP TWB200 TWP TWB9000 15 FLOW SCHEMATIC MODELS TWB1000 1500 DWG FS11687 Rev...
Page 16: ...TWP TWB200 TWP TWB9000 16 FLOW SCHEMATIC MODELS TWB2000 9000 DWG FS11688 Rev...
Page 17: ...TWP TWB200 TWP TWB9000 17 WIRING DIAGRAM STANDARD CONTROLLER...
Page 18: ...TWP TWB200 TWP TWB9000 18 WIRING DIAGRAM STANDARD CONTROLLER...
Page 19: ...TWP TWB200 TWP TWB9000 19 WIRING DIAGRAM STANDARD CONTROLLER...
Page 20: ...TWP TWB200 TWP TWB9000 20 WIRING DIAGRAM STANDARD CONTROLLER...
Page 21: ...TWP TWB200 TWP TWB9000 21 PANEL LAYOUT STANDARD CONTROLLER...
Page 38: ...TWP TWB200 TWP TWB9000 38 Service Screen...
Page 71: ...TWP TWB200 TWP TWB9000 71...