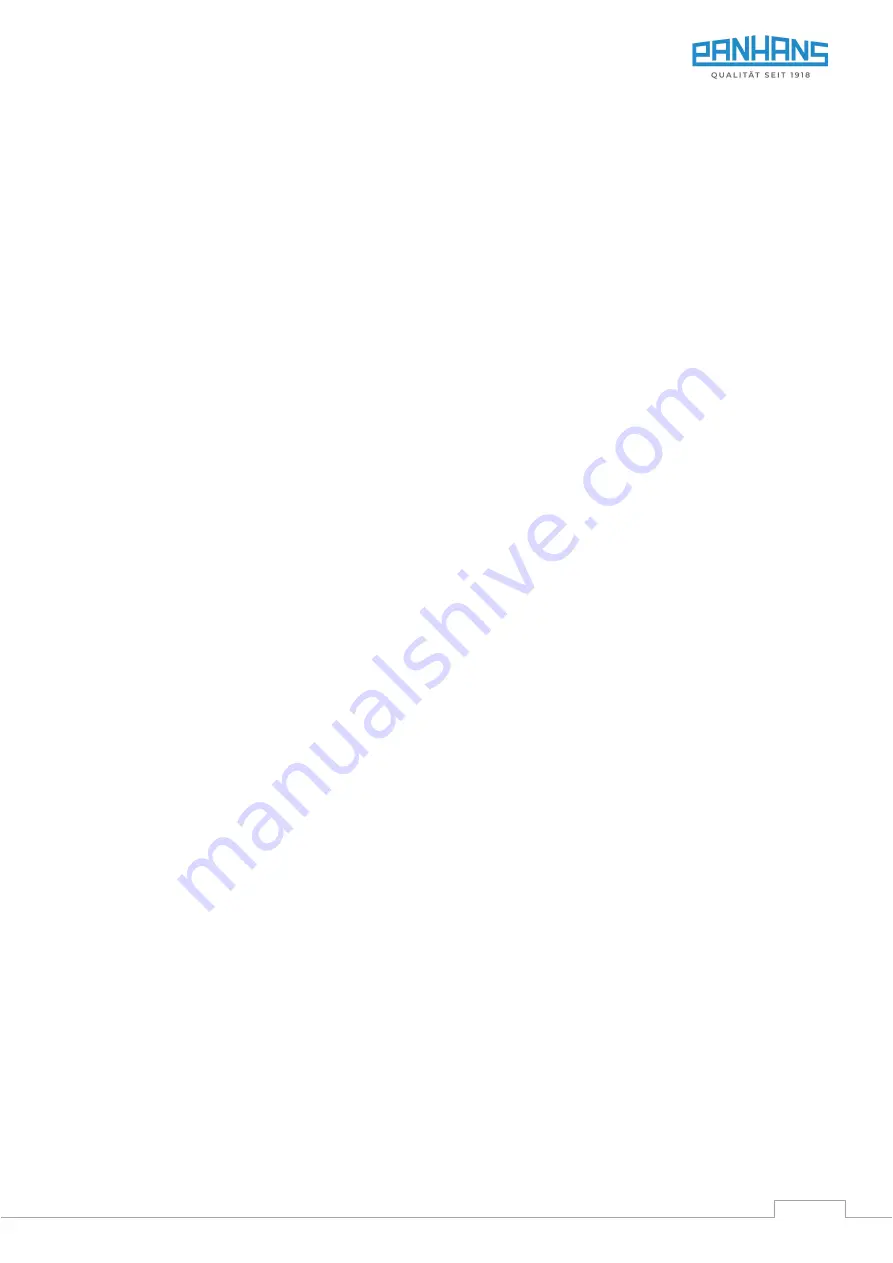
BA_PH_690-200_EN_11-22.docx
24
5.2
Technical Characteristics
•
Sliding table saw for trimming, cutting to length, sizing, mitre cutting, etc.
•
Dimensionally stable and self-supporting machine body
•
Torsion-resistant and finely planed cast iron table top
•
Robust and powerful saw unit for precise saw cuts
•
Double-guided swivel segments made of grey cast iron
•
Double column guide for height adjustment with 2-fold ball bearing mounted, long circular saw shaft for
absolutely smooth running and with remote locking in 50 mm grid
•
Smooth-running and maintenance-free double slide table (ball-bearing mounted and extra stable) with
precise and play-free running over the entire length
•
Stable and lightweight cross slide, made of steel profiles with a support roller on the outer narrow side
•
Cross-cut fence profile with mm scale and magnifying glass, telescopic extension up to 3200 mm, including
two robust and backlash-free flip stops and additional end flip stop
•
Electromotive rip fence with cutting width 1250 mm to the right of the saw blade, position setting at the top of
the control panel via positioning control (accuracy 0.1 mm).
•
Fold-down fence for free table surface; safety shut-off bar in case of danger of crushing between rip fence and
slide table
•
Table widening
1430 x 940
mm and table extension 750 x 655 mm with pull-out tool drawer
•
Control panel with 7" touchscreen control placed at eye level, swivelling, including template holder
•
Motorised height and tilt adjustment via positioning control, including visualisation of cutting height, cut-
ting width, tilt adjustment and saw blade speed
•
Swivel-mounted control panel, template holder included
•
Tilt range of the saw blade 0 -
46°
•
APA saw blade quick clamping system
•
Main saw blade speed 3000/4000/5000/6000 rpm
•
Protective device can be swivelled away to both sides, guard with interchangeable insert wide/narrow
•
Push-button control with electronic soft start (start/stop)
•
Electronic, wear-free motor brake
•
Saw blade Ø 400 mm retractable under the table
•
Extraction port Ø 120 mm on machine body, Ø 80 mm on protective hood
•
Slide table, length and width stop profile anodised
•
Machine body and swivel arm powder coated
•
CE-conform, GS tested