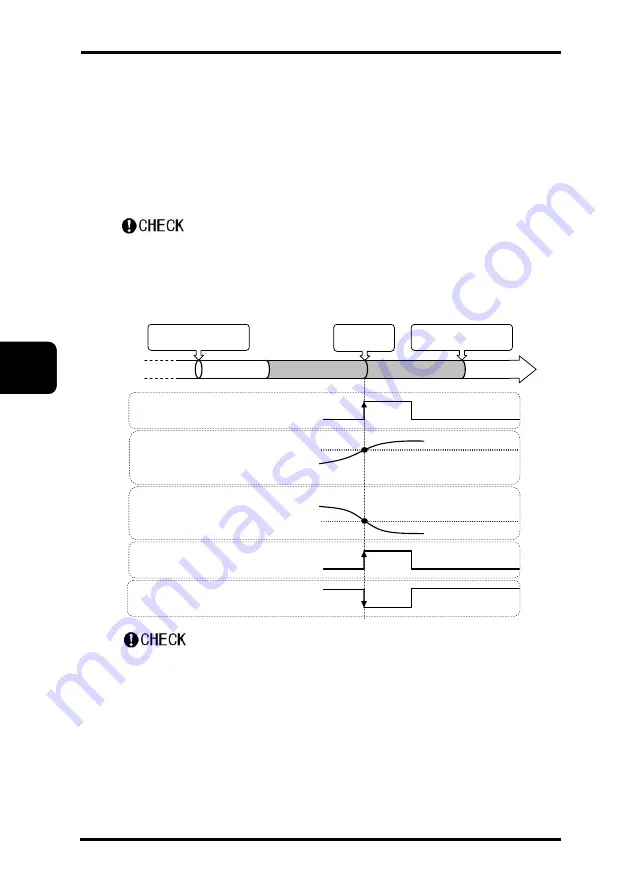
Chapter 3 Function
3-52
3
Trigger Conditions
This function is used for setting the trigger generation conditions when the
buffering mode is set to trigger mode.
A value the same as or higher or lower than a threshold or the time of alarm
occurrence or release can be set as a trigger condition if timing input is ON.
The value is set to "At timing input ON" by default.
•
Keep in mind that the "Alarm Delay Times" set will become effective if "At
alarm occurred" is set as a trigger condition.
Ex) If the "Buffering Mode" is set to trigger mode, the operation of each trigger
condition is shown below:
Normally, the measurement value is kept on hold when timing input is ON. Only if
the buffering mode is set to “trigger mode” and this function is set to "At timing
input ON," however, the measurement value will not be kept on hold at the
moment timing input is ON while the system is in buffering operation.
Trigger generate
(Trigger point)
Accumulation of data
Meas. ope
Buffering start
Buffering stop or Accu.
amount reached
Stand-by
Threshold
Meas. value
Meas. state
Alarm
Normal
At threshold or above
At alarm occurred
Meas. state
At alarm released
At threshold or below
Timing input
ON
OFF
At timing input ON
Alarm
Normal
Threshold
Meas. value
Summary of Contents for HL-G1 A-C5 Series
Page 18: ...Introduction 16 ...
Page 151: ......