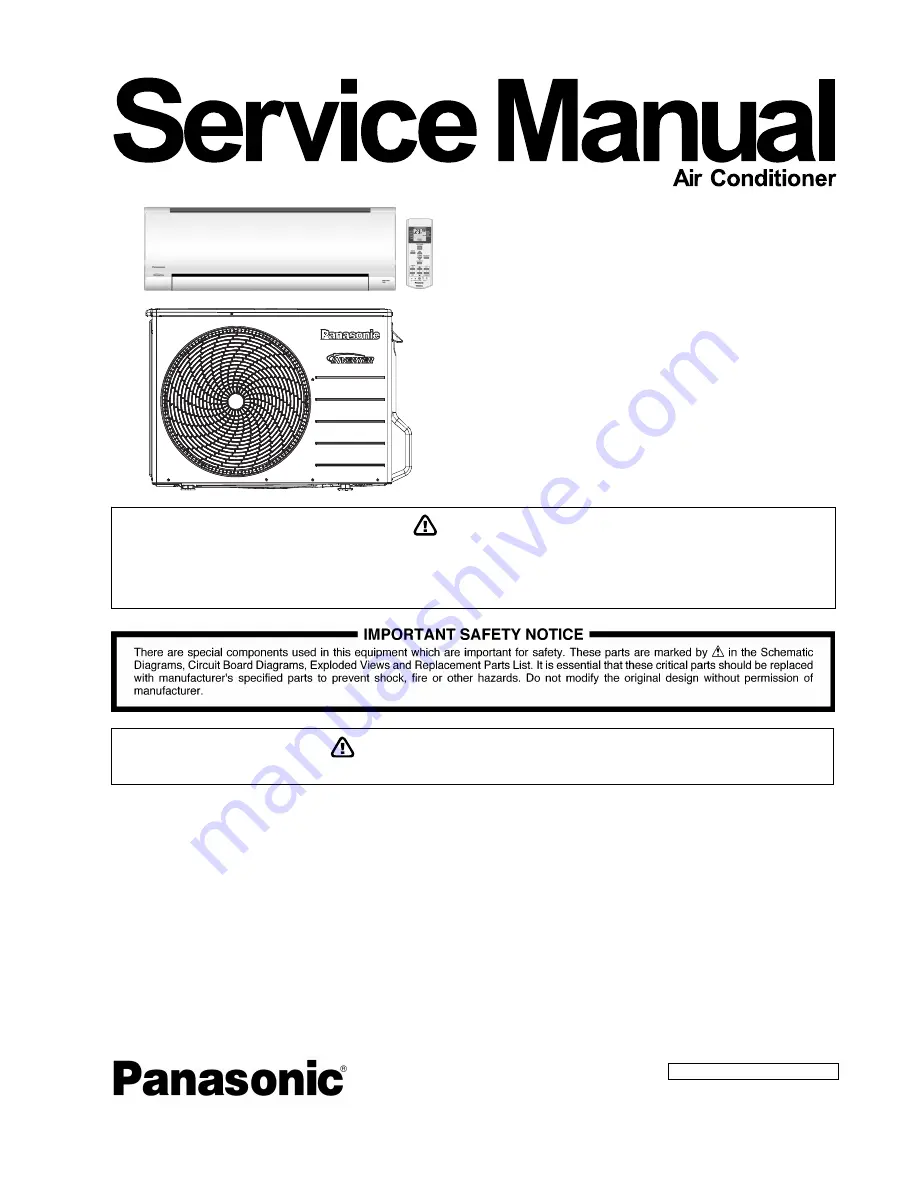
© Panasonic Corporation 2013.
Order No: PAPAMY1307111CE
Indoor Unit
Outdoor Unit
CS-CE9PKE
CS-CE12PKE
CU-CE9PKE
CU-CE12PKE
Destination
North Europe
TABLE OF CONTENTS
1.
Safety Precautions.............................................3
2.
Specifications .....................................................5
3.
Features ............................................................11
4.
Location of Controls and Components .........12
4.1
Indoor Unit..................................................12
4.2
Outdoor Unit ...............................................12
4.3
Remote Control ..........................................12
5.
Dimensions .......................................................13
5.1
Indoor Unit..................................................13
5.2
Outdoor Unit ...............................................14
6.
Refrigeration Cycle Diagram...........................15
6.1
CS-CE9PKE CU-CE9PKE .........................15
6.2
CS-CE12PKE CU-CE12PKE .....................16
7.
Block Diagram ..................................................17
8.
Wiring Connection Diagram............................18
8.1
Indoor Unit..................................................18
8.2
Outdoor Unit ...............................................19
9.
Electronic Circuit Diagram ..............................21
PRECAUTION OF LOW TEMPERATURE
In order to avoid frostbite, be assured of no refrigerant leakage during the installation or repairing of refrigerant circuit.
This service information is designed for experienced repair technicians only and is not designed for use by the general public.
It does not contain warnings or cautions to advise non-technical individuals of potential dangers in attempting to service a product.
Products powered by electricity should be serviced or repaired only by experienced professional technicians. Any attempt to service
or repair the product or products dealt with in this service information by anyone else could result in serious injury or death.
WARNING