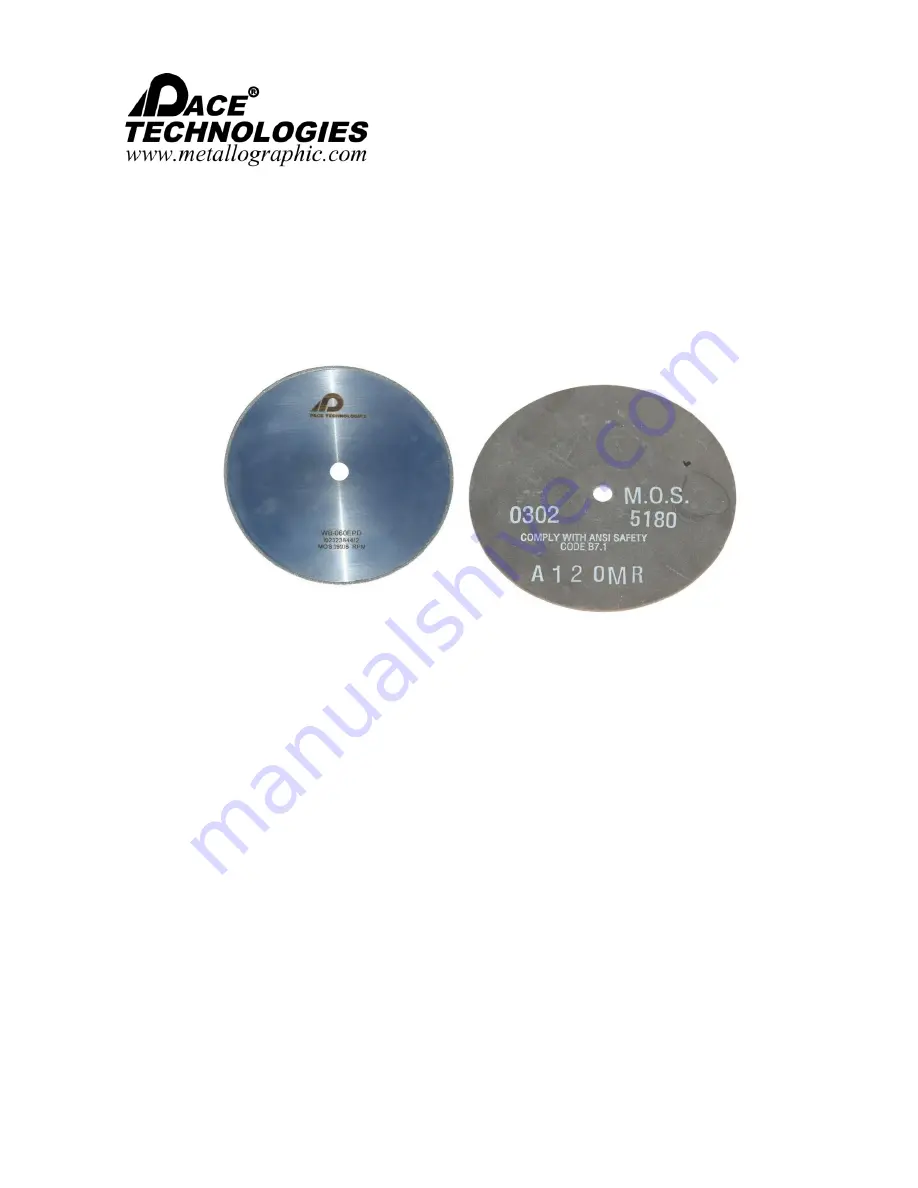
Please read this instruction manual carefully and follow all installation, operating and safety guidelines.
44
PICO-155S Precision Saw
I
NSTRUCTION
M
ANUAL
- - - - - - - - - - - - - - - - - - - - - - - - - - - - - - - - - - - - - - - - - - - - - - - - - - ▲
3601 E. 34th St. Tucson, AZ 85713 USA Tel. +1 520-882-6598 Fax +1 520-882-6599 email: [email protected] Web: http://www.metallographic.com
Figure 9-3
(a) Electroplated diamond wafering blade for cutting
Although less common, thin resin/rubber abrasive blades can used for cutting on precision wafering
saws (Figure 9-3b). For cutting with abrasive blades on precision wafer saws, set the speed of the
saw to at least 1500 rpm. Note that abrasive blades create significantly more debris which requires
changing out of the cutting fluid more frequently.
soft materials (left) and (b) alumina resin/rubber blade (right).
Perhaps the most important parameter for precision sectioning is the abrasive size. Similar to
grinding and polishing, finer abrasives produce less damage. For extremely brittle materials, finer
abrasives are required to minimize and manage the damage produced during sectioning.
Sectioning with a fine abrasive wafering blade is often the only way that a specimen can be cut so
that the final polished specimen represents the true microstructure. Examples include: silicon
computer chips, gallium arsenide, brittle glasses, ceramic composites, and boron/graphite
composites. Figure 9-4a and 9-4b compares the effects of cutting with a fine grit blade vs. a
standard medium grit blade for sectioning a boron graphite golf shaft. As can be seen, the fine grit
blade produces significantly less damage to boron fibers.