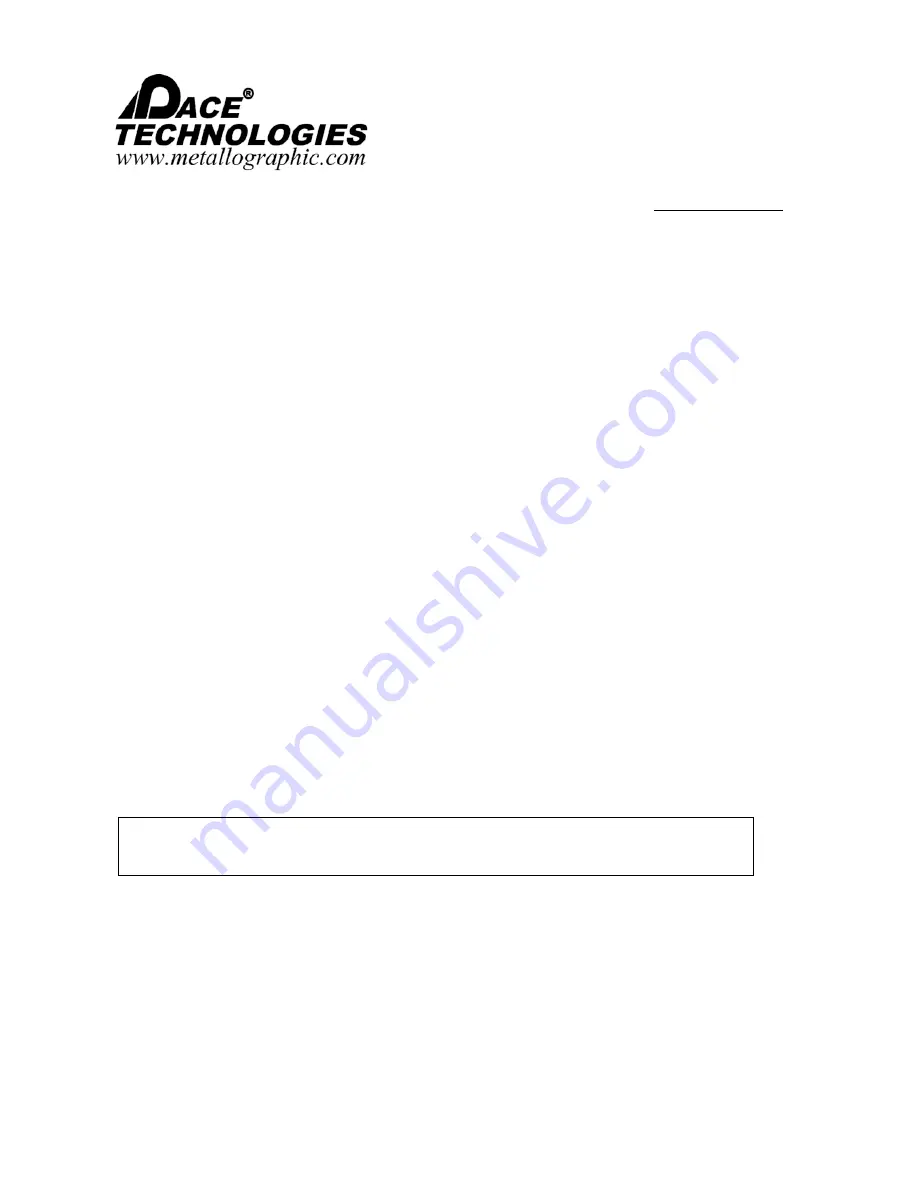
NANO 1000S Polisher
I
NSTRUCTION
M
ANUAL
- - - - - - - - - - - - - - - - - - - - - - - - - - - - - - - - - - - - - - - - - - - - - - - - - - ▲
3601 E. 34th St. Tucson, AZ 85713 USA Tel. +1 520-882-6598 Fax +1 520-882-6599 email: [email protected] W eb: https://www.metallographic.com
Please read this instruction manual carefully and follow all installation, operating and safety guidelines.
21
4.7.1 Rough / Planar Grinding
Rough or planar grinding, is required to produce flat specimens and to reduce
the damage created by sectioning. The planar grinding step is accomplished
by decreasing the abrasive grit particle size sequentially to obtain surface
finishes that are ready for polishing. Care must be taken to avoid being too
abrasive in this step, and actually creating greater specimen damage than
produced during cutting. This is especially true for very brittle materials such
as ceramics and silicon.
The machine parameters which affect the preparation of metallographic
specimens include: grinding / polishing pressure, grinding direction, and the
relative velocity distribution between the specimen and the polishing wheel.
Grinding Pressure
Grinding / polishing pressure is dependent upon the applied force (pounds or
Newton's) and the area of the specimen and mounting material. Pressure is
defined as the Force/Area (psi, N/
m
2
or Pa). For specimens significantly
harder than the mounting compound, pressure is better defined as the force
divided by the specimen surface area. Thus, for larger hard specimens, higher
grinding / polishing pressures increase stock removal rates. However, higher
pressure also increases the amount of surface and subsurface damage
produced in the specimen.
Note
: Regarding SiC grinding papers, as the abrasive grains dull and cut rates
decrease, increasing grinding pressures can extend the life of the SiC paper.
Higher grinding / polishing pressures can also generate additional
frictional heat which may be beneficial for the chemical mechanical
polishing (CMP) of ceramics, minerals and composites. Likewise, for
extremely friable specimens (such as nodular cast iron), higher pressures
and lower relative velocity distributions can aid in retaining inclusions and
secondary phases.