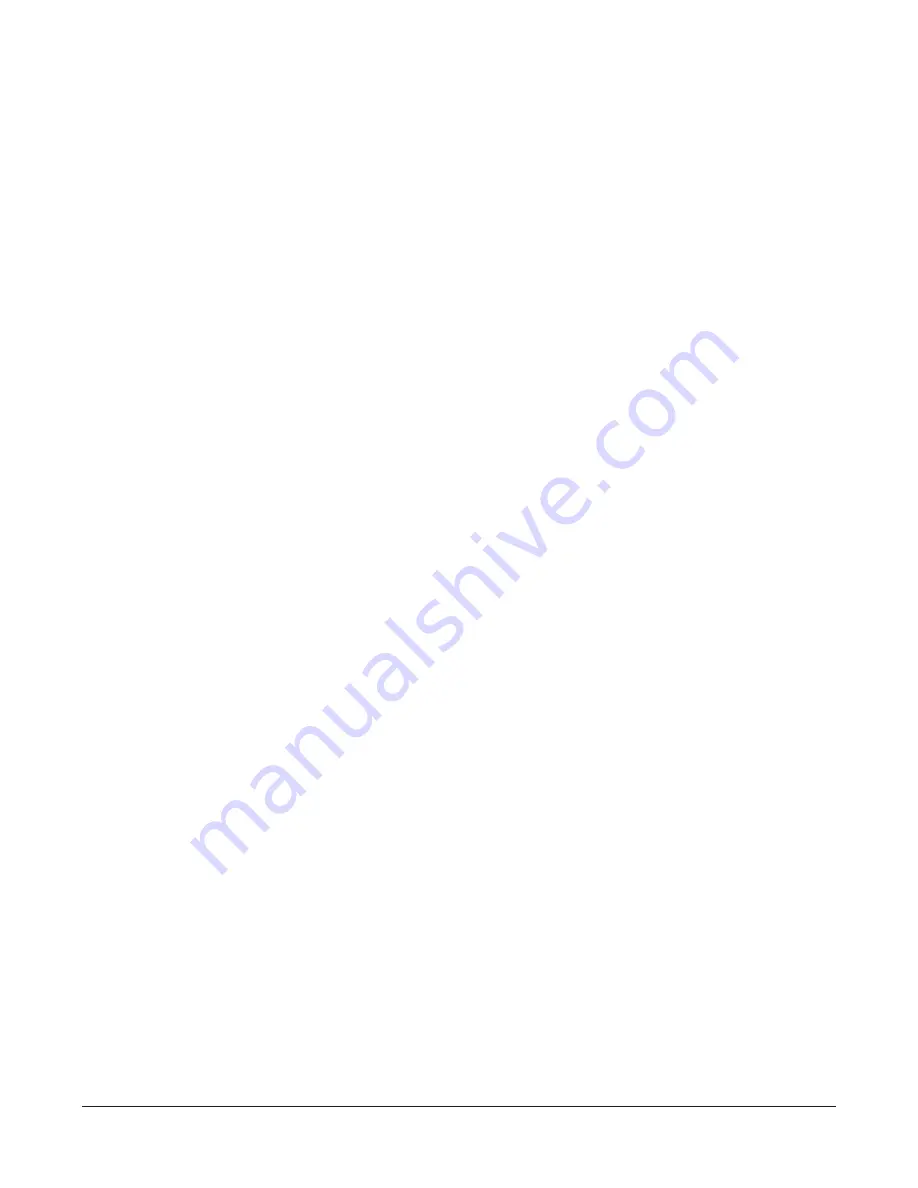
Model MMC200 Multi-Material Cutter
IMPORTANT: No liability will be incurred by The
Eraser Co. for injury, death, or property dam-
age caused by a product which has been set
up, operated, and/or installed contrary to
Eraser’s written operating manual, or which
has been subjected to misuse, negligence, or
accident, or which has been repaired or al-
tered by anyone other than Eraser, or which
has been used in a manner or for a purpose
for which the product was not designed.
OPERATING INSTRUCTIONS
DO NOT OPERATE TOOL UNTIL YOU HAVE
READ THOROUGHLY, AND UNDERSTAND
COMPLETELY, ALL INSTRUCTIONS, RULES,
ETC., ON THESE PAGES. THESE ARE IMPOR-
TANT SAFETY INSTRUCTIONS AND SHOULD
BE KEPT FOR FUTURE REFERENCE. CON-
TACT ERASER IF INSTRUCTIONS ARE NOT
CLEAR.
The following instructions apply for firmware cre-
ated after June 07, 2005. For previous versions,
use instructions appropriate for those. When the
machine is powered up, the “splash” screen will
reveal which instructions are to be used:
THE ERASER COMPANY
MMC200 06-07-05
A date in the third line of the display indicates re-
vised firmware and that the following instructions
apply. No firmware written before this date displays
the revision date on the splash screen.
SET-UP:
The MMC200 is supplied with one fixed, stationary
blade (lower) and one moveable blade (upper).
Also included are three Allen wrenches; 1/8",
3/16" & 9/64"
CAUTION
: The MMC200 comes with the blades
completely installed. These blades are intended
for use on wire and tubing and are extremely sharp.
Caution must be used when removing or installing
these blades.
Place the unit on a sturdy workbench with the right
side exit chute even with the right side of the bench.
Short and long cut lengths will drop out the right
side of the exit chute. Material collection bins can
be placed to collect the cut material as it exits. If
using the DE700 (or any other tensioning de-reeler)
place the de-reeler to the left of the unit at least 24"
from the entrance. High feed rates and high man-
datory production rates may necessitate the use
of the APF100 prefeeder. Refer to the de-reeler’s
operating instructions for further set up details.
If this MMC200 is to be used with the automatic
pre-feeder (APF100), insert the communication
cable (part # PR1212) into the DB9 connector la-
beled “COMMUNICATION PORT” on both ma-
chines. This allows the MMC200 to pause process-
ing in the event of a material mis-feed. This fea-
ture can be used to stop the MMC200 by an exter-
nal signal applied to the pins of this port (a DC
voltage from 5V to 24V or higher if applied briefly).
This allows the MMC200 to be controlled by an
external process. Call factory for details.
Insert the power cord into the IEC connector. Plug
the unit into the appropriate power supply using
the correct plug for the unit purchased. Use a prop-
erly grounded mains supply. The American plug is
for use on 110/120V 60Hz mains supply. The
European and United Kingdom plugs are for 220/
240V 50Hz mains supply. Connect clean, dry, com-
pressed air at 40 to 90 P.S.I.
Caution:
Environmental conditions for proper op-
eration should be 50° F-104° F (10° C-40° C) and
30-75% relative humidity. The MMC200 should be
operated in a well-ventilated open workspace. This
machine may be affected by outside environmen-
tal disturbances. The unit is rated for continuous
use and is protected by one fuse located in the
IEC connector.
Caution:
Safety glasses or other suitable eye pro-
tection should be worn when operating this unit.
OPERATION:
Turn the MMC200 on using the I/O switch on the
side of the unit. Do not turn the unit on and off re-
peatedly without waiting 5 seconds. Removing the
Production Automation • Eden Prairie, MN USA • Ph: 888-903-0333 • [email protected] • www.gotopac.com • Fax 952-903-0315
Summary of Contents for MMC200
Page 15: ...NOTES...
Page 16: ...IR1814 REV 04 08 Aut...