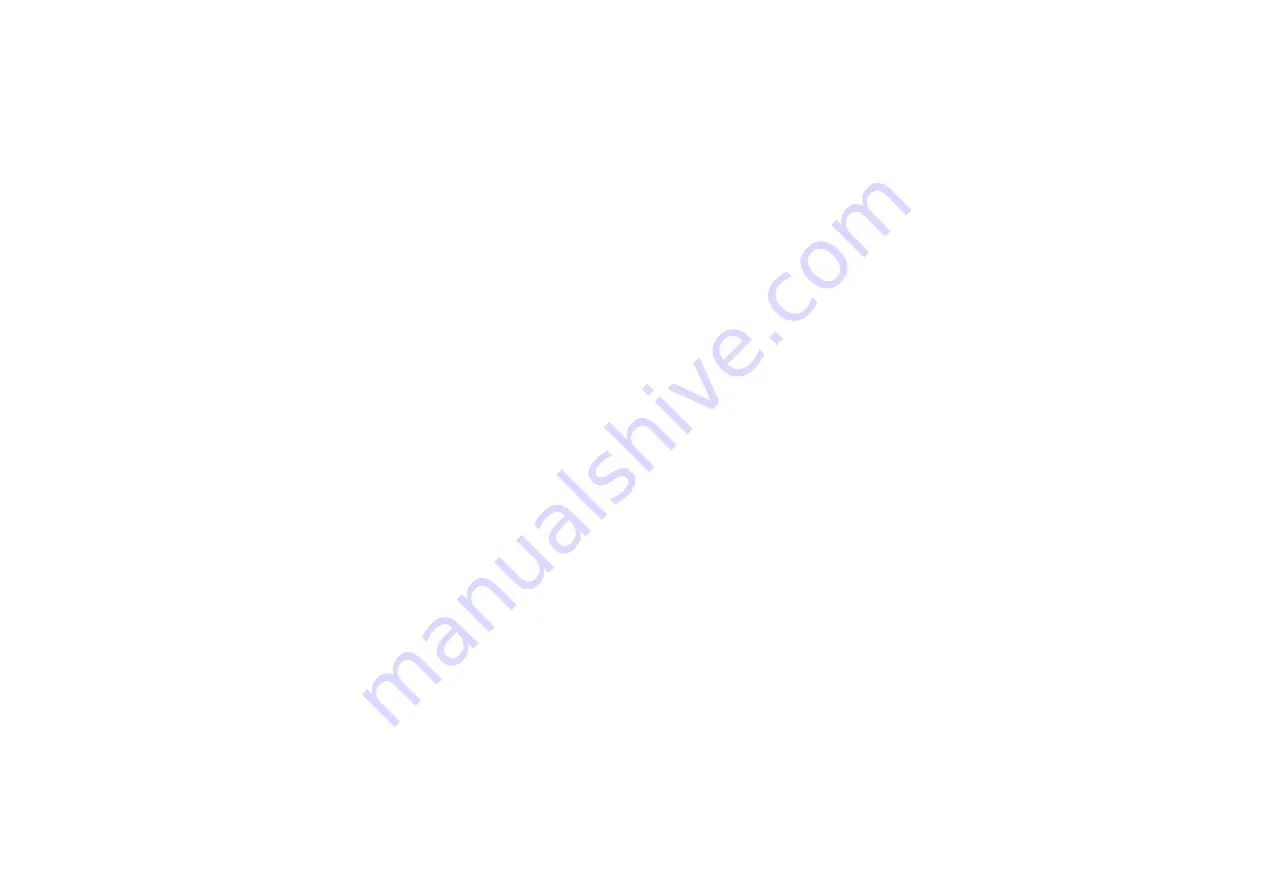
5 DETECTION OF FLAMMABLE REFRIGERANTS
Under no circumstances shall potential sources of ignition be used in the
searching for or detection of refrigerant leaks. A halide torch (or any other
detector using a naked flame) shall not be used.
6 LEAK DETECTION METHODS
The following leak detection methods are deemed acceptable for systems
containing flammable refrigerants. Electronic leak detectors shall be used to
detect flammable refrigerants, but the sensitivity may not be adequate, or may
need recalibration. (Detection equipment shall be calibrated in a refrigerant-free
area.) Ensure that the detector is not a potential source of ignition and is
suitable for the refrigerant used. Leak detection equipment shall be set at a
percentage of the LFL of the refrigerant and shall be calibrated to the refrigerant
employed and the appropriate percentage of gas (25 % maximum) is
confirmed. Leak detection fluids are suitable for use with most refrigerants but
the use of detergents containing chlorine shall be avoided as the chlorine may
react with the refrigerant and corrode the copper pipe-work. If a leak is suspect-
ed, all naked flames shall be removed/extinguished. If a leakage of refrigerant
is found which requires brazing, all of the refrigerant shall be recovered from
the system, or isolated (by means of shut off valves) in a part of the system
remote from the leak. Oxygen free nitrogen (OFN) shall then be purged through
the system both before and during the brazing process.
7 REMOVAL AND EVACUATION
When breaking into the refrigerant circuit to make repairs – or for any other
purpose – con- ventional procedures shall be used.However, it is important that
best practice is followed since flammability is a consideration. The following
procedure shall be adhered to: remove refrigerant; purge the circuit with inert
gas; evacuate; purge again with inert gas; open the circuit by cutting or braz-
ing.The refrigerant charge shall be recovered into the correct recovery cylin-
ders. The system shall be “flushed” with OFN to render the unit safe. This
process may need to be repeated several times.Compressed air or oxygen
8
shall not be used for this task. Flushing shall be achieved by breaking the
vacuum in the system with OFN and continuing to fill until the working pressure
is achieved, then venting to atmosphere, and finally pulling down to a vacuum.
This process shall be repeated until no refrigerant is within the system. When
the final OFN charge is used, the system shall be vented down to atmospheric
pressure to enable work to take place.This operation is absolutely vital if
brazing operations on the pipework are to take place. Ensure that the outlet for
the vacuum pump is not close to any ignition sources and there is ventilation
available.
8 CHARGING PROCEDURES
In addition to conventional charging procedures,the following requirements
shall be followed.
- Ensure that contamination of different refrigerants does not occur when using
charging equipment. Hoses or lines shall be as short as possible to minimise
the amount of refrigerant contained in them.
- Cylinders shall be kept upright.
- Ensure that the refrigeration system is earthed prior to charging the system
with refrigerant.
- Label the system when charging is complete (if not already).
- Extreme care shall be taken not to overfill the refrigeration system.
Prior to recharging the system it shall be pressure tested with OFN. The system
shall be leak tested on completion of charging but prior to commissioning. A
follow up leak test shall be carried out prior to leaving the site.
9 DECOMMISSIONING
Before carrying out this procedure, it is essential that the technician is com-
pletely familiar
with the equipment and all its detail. It is recommended good practice that all
refrigerants are recovered safely. Prior to the task being carried out, an oil and
refrigerant sample shall be taken in case analysis is required prior to re-use of
reclaimed refrigerant. It is essential that electrical power is available before the
task is commenced.
9