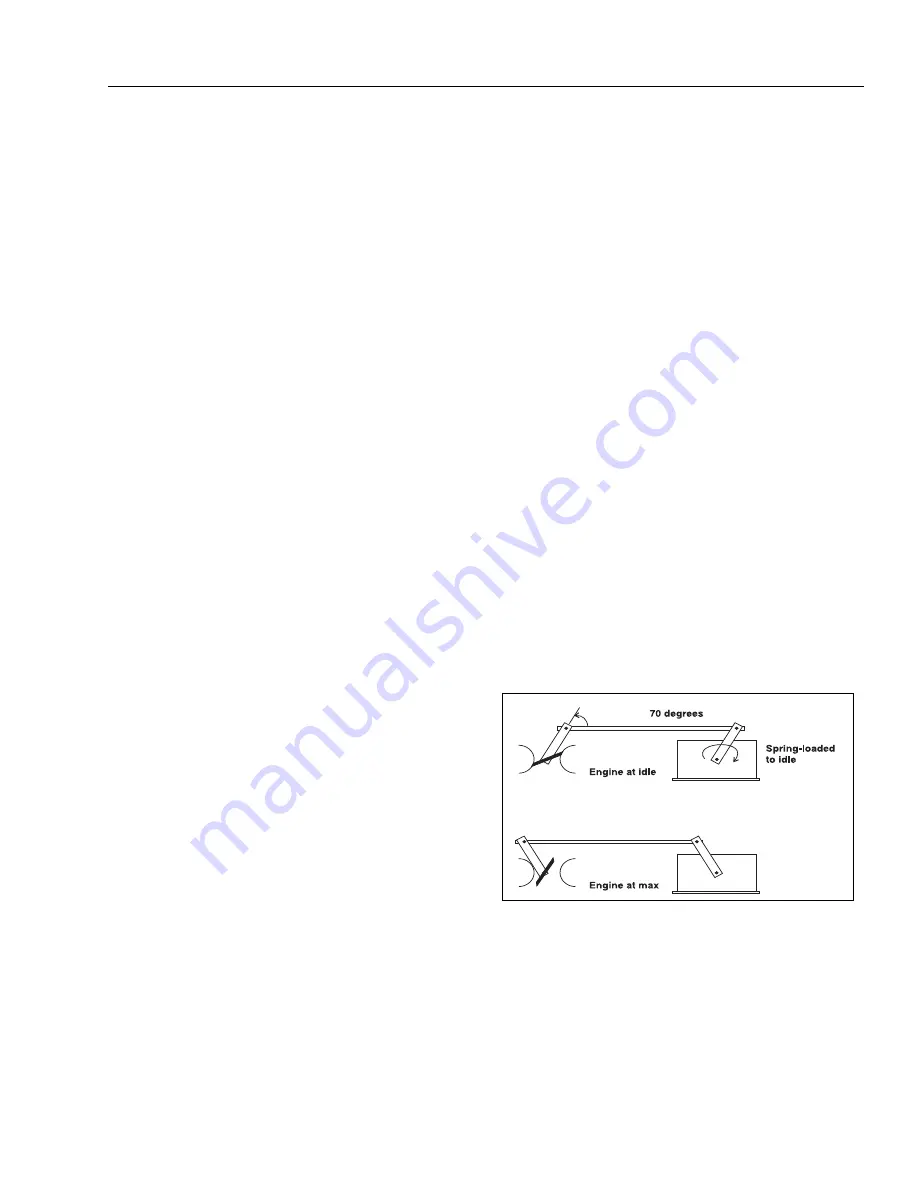
SECTION 3 - CHASSIS & TURNTABLE
3120740
– JLG Lift –
3-111
DTC 363
- Megajector Internal Actuator Fault Detection.
a. Connections
- Check power, ground, and CAN cir-
cuits at the Megajector in addition to all electrical
connections. Repair as necessary and retest.
b. Megajector
- Megajector has an internal failure.
Contact JLG Industries for further assistance.
DTC 364
- Megajector Internal Circuitry Fault Detection.
a. Connections
- Check power, ground, and CAN cir-
cuits at the Megajector in addition to all electrical
connections. Repair as necessary and retest.
b. Megajector
- Megajector has an internal failure.
Contact JLG Industries for further assistance.
DTC 365
- Megajector Internal Comm Fault Detection.
a. Connections
- Check power, ground, and CAN cir-
cuits at the Megajector in addition to all electrical
connections. Repair as necessary and retest.
b. Megajector
- Megajector has an internal failure.
Contact JLG Industries for further assistance.
3.26
ELECTRIC GOVERNOR INSTALLATION AND
ADJUSTMENTS - FORD LRG425 ENGINE (PRIOR
TO S/N 0300065534)
General
These instructions presume no electrical test equipment other
than a multimeter for making the electrical measurements
called for on the following pages. If no suitable meter is avail-
able, an inexpensive but adequate meter, part number 22-188
is available from any local Radio Shack store.
Many “governor problems” turn out to be installation prob-
lems, particularly in first-time applications. Careful attention to
the directions provided will go far toward a successful installa-
tion made in the least amount of time.
Quick-start Installations
If you are experienced in installing and adjusting Electric Gov-
ernor, follow these steps. Otherwise, refer to the more detailed
instructions starting with “MOUNTING-ACTUATOR”.
1.
Mount Actuator rigidly to engine location which will
permit a short, straight linkage to the carburetor or fuel
valve. Avoid very hot areas.
2.
Mount controller in a dry, fairly cool location. Accessibil-
ity for adjusting is required.
3.
Wire per appropriate included schematic, using #16
wire.
4.
Set up fuel linkage. This is critical, so review the section
titled “LINKAGE”.
5.
Hold linkage for safety, and start engine.
6.
Adjust engine speed to desired valve using High Engine
pot. Turn CW to increase, CCW to decrease speed.
Mounting-Actuator
The Actuator may be mounted in any attitude - there is no pre-
ferred orientation.
With no power applied, the Actuator is spring-loaded to the
minimum fuel position. The Actuator output shaft rotates
toward the maximum fuel position against this spring through
electrical power from the controller. This rotation is CW (clock-
wise) on one side of the Actuator, and CCW (counterclockwise)
on the other. If necessary, reverse the Actuator on its mount-
ing plate so that the desired direction of rotation is on the
desired side to match the fuel system direction of travel.
Before selecting the mounting location, consider the linkage
that will be required to connect the Actuator output arm to
the butterfly or fuel valve. Read the following section on link-
ages before deciding on a mounting location!
1.
Mount Actuator rigidly to engine location which will
permit a short, straight linkage to the carburetor or fuel
valve. Avoid very hot areas.
Linkage
1/4” -28 threaded rod and low friction rod-end bearings are
recommended for linkage materials.
Keep the linkage as short and as straight as possible.
The linkage must not rub against the engine, brackets, hoses,
etc. The linkage must be free of friction and lost motion or
“slop”.
The following sketch indicates the proper linkage geometry
for most installations.
Note that the angle between the carburetor arm and the rod is
70 degrees with the engine at idle. This is highly desirable!
Note also that the Actuator arm travels equally on either side
of a 90 degree angle with the rod. This angular arrangement
will give the proper mechanical gain for good stability and
performance. It may be necessary to rotate the carburetor arm
relative to the butterfly to achieve this. This can usually be
done, and is usually worth the effort! Below are some work-
able installations, with good linkages. Remember, the Actuator
can be turned 180 degrees on its mounting to “reverse” the
Go
to
Discount-Equipment.com
to
order
your
parts