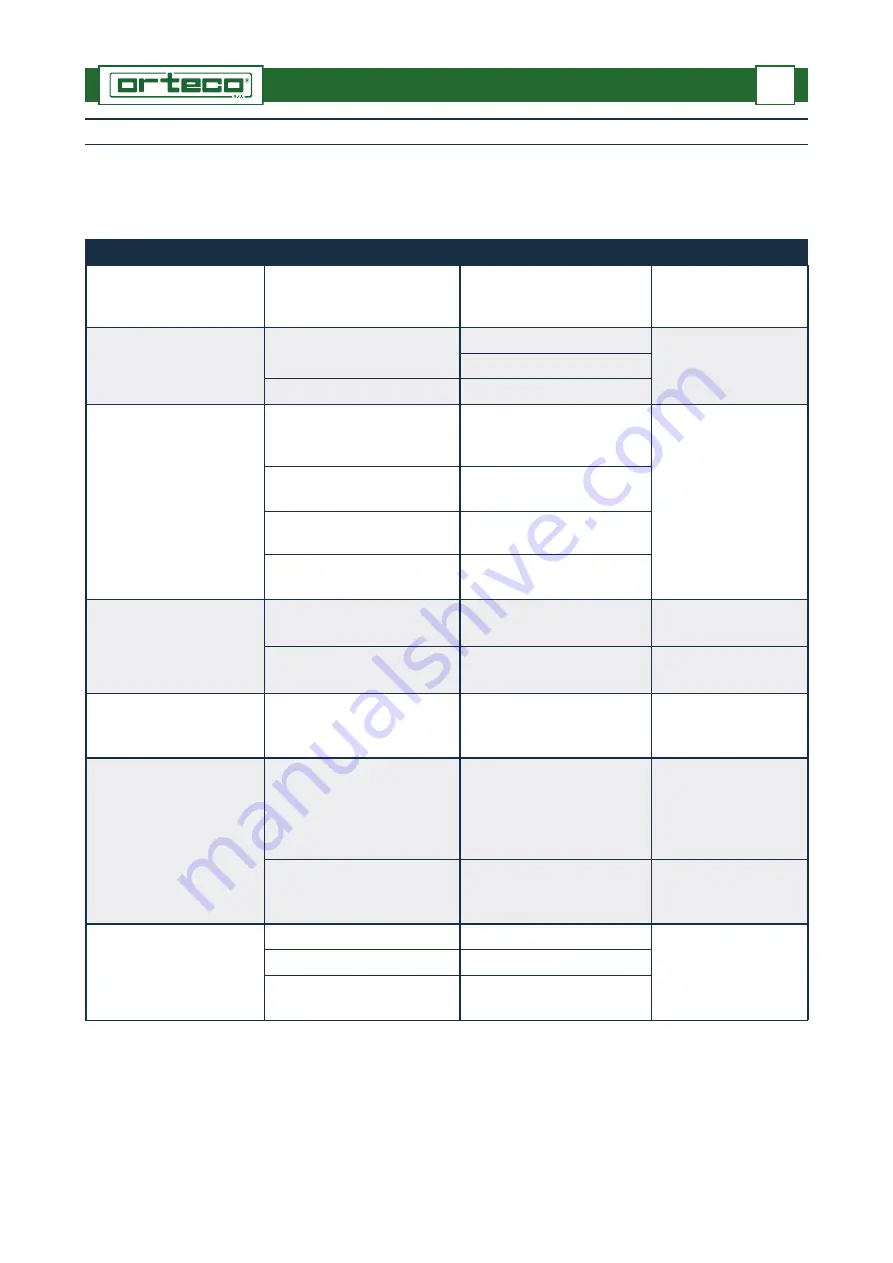
63
English language
Use and maintenance
BREAKDOWN INFORMATION
8
Safety advice in case of faults
Repairs that require specific technical competence or special skills must be carried
out only by an authorised service centre.
Fault
Likely cause
Solution
Reference
Hammer percussion is not
regular
Cold oil
Repeat machine movements
several times to heat the oil
Weak hammer percussion
Flat accumulator
Recharge
Contact an authorised
service centre
(*)
Damaged accumulator
Replace the membrane
Percussion gets blocked
Excessive oil counter pressure
in return pipe
Restore the correct counter
pressure
Contact an authorised
service centre
Excessive oil delivery
Restore the correct oil
delivery
Loose nuts of the percussion
hammer’s tie rod
Tighten the nuts
Faulty hydraulic system
Restore the hydraulic system
The engine switches off
immediately after start-up
The emergency button has
been accidentally pressed
Deactivate the emergency
button
The electrical system of the
emergency button in faulty
Repair the fault
Contact an authorised
service centre
Locking machine
movements
Maximum pressure valves of
the distributors clogged with
dirt
Clean the valves
Contact an authorised
service centre
The accessory does not
switch on
The hydraulic supply by-pass
valve lever is in the hammer
activation position
Turn the valve lever to the
correct position
The accessory does not work
correctly
See the instruction
manual of the accessory’s
manufacturer
The machine does not
have the original operating
speed and percussion
power
Damaged pump
Replace the pump
Contact an authorised
service centre
Damaged PTO
Replace the PTO
Main pressure valve not
calibrated correctly
Set correct calibration
(*) If the accumulator has worked for a prolonged period at a pressure below 20 bar, replace the
membrane
Summary of Contents for IIa Series
Page 2: ......
Page 6: ......
Page 84: ...78 ENCLOSURES A English language Use and maintenance...
Page 85: ...79 ENCLOSURES A English language Use and maintenance...
Page 86: ...80 ENCLOSURES A English language Use and maintenance...
Page 87: ...81 ENCLOSURES A English language Use and maintenance...
Page 88: ...82 ENCLOSURES A English language Use and maintenance...
Page 89: ...83 ENCLOSURES A English language Use and maintenance...
Page 90: ...84 ENCLOSURES A English language Use and maintenance...
Page 91: ...85 ENCLOSURES A English language Use and maintenance...
Page 92: ...86 ENCLOSURES A English language Use and maintenance...
Page 114: ...108 ENCLOSURES A English language Use and maintenance...