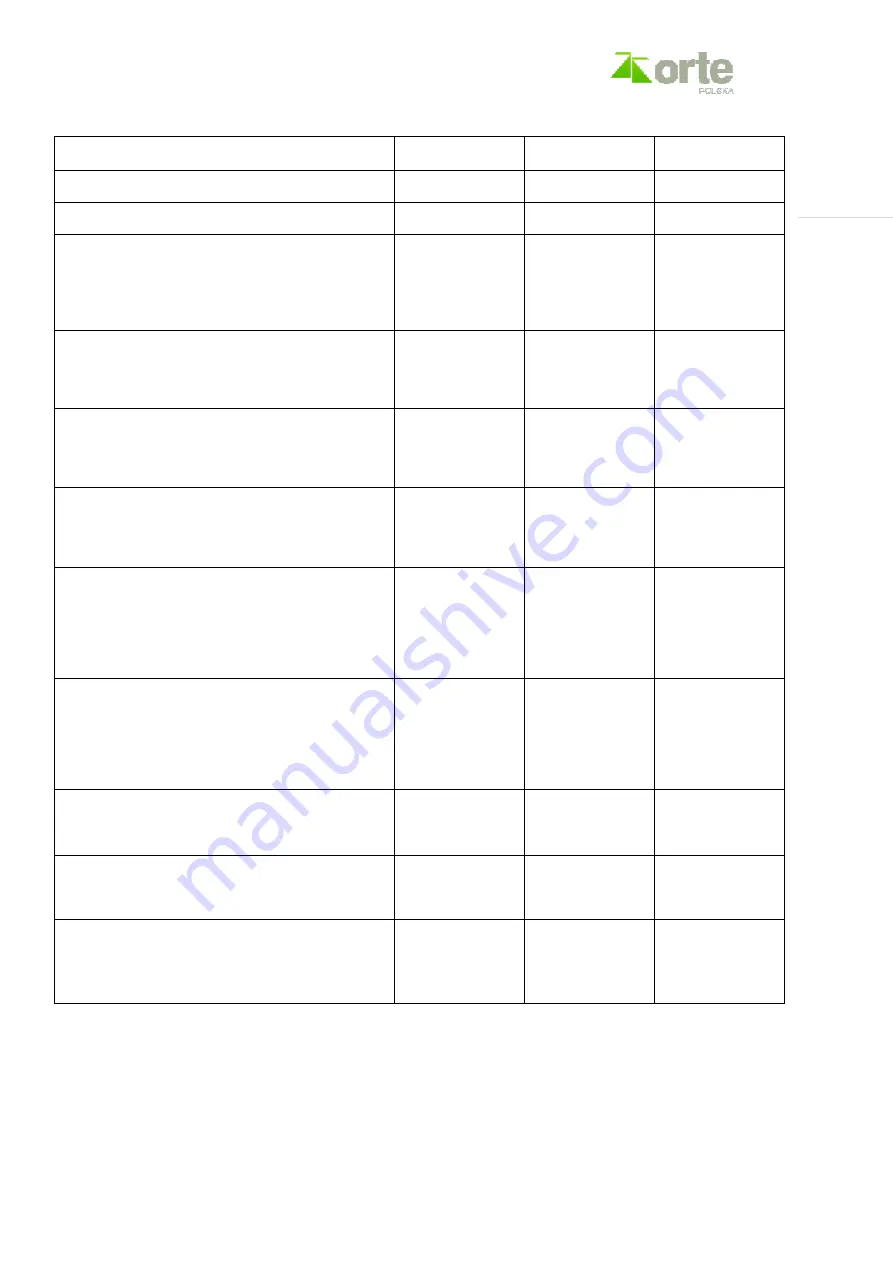
www.orte.pl
www.orte.pl
Page | 36
PERFORMED SERVICE
Maintenance depending on inspections and needs
Date
Date
Date
Checking the general state of the heating
system
Checking and controlling the heating
system
Checking parts with
flowing water:
•
tightness during operation
• leak tests
•
visible signs of corrosion
• signs of wear
Checking heating surfaces
and exhaust manifold for
dirt, cleaning if necessary.
Checking the tightness of the
batch doors and combustion chamber doors
Checking combustion air
supply:
• Does the combustion air hole exist and
is it open?
Has the thermal outflow protection been
checked?
• Flow pressure
• Flow
Checking operating pressure
• Vent the heating system
•
Check the safety valve
• Set the initial pressure of the expansion
vessel (technical documentation
of the expansion vessel: option)
Checking the exhaust system
•
Connection pipe is cleaned
• Additional air device is clean
and set according to the boiler output
• Temperature of exhaust gases
• Chimney draft
Checking minimum return temperature
•
Set to the correct value
•
Return temperature at the boiler return
Final inspection of maintenance activities,
document measurement and
test results
Confirmation of professional inspection
Stamp
of
the
company/signature
Stamp
of
the
company/signature
Stamp
of
the
company/signature