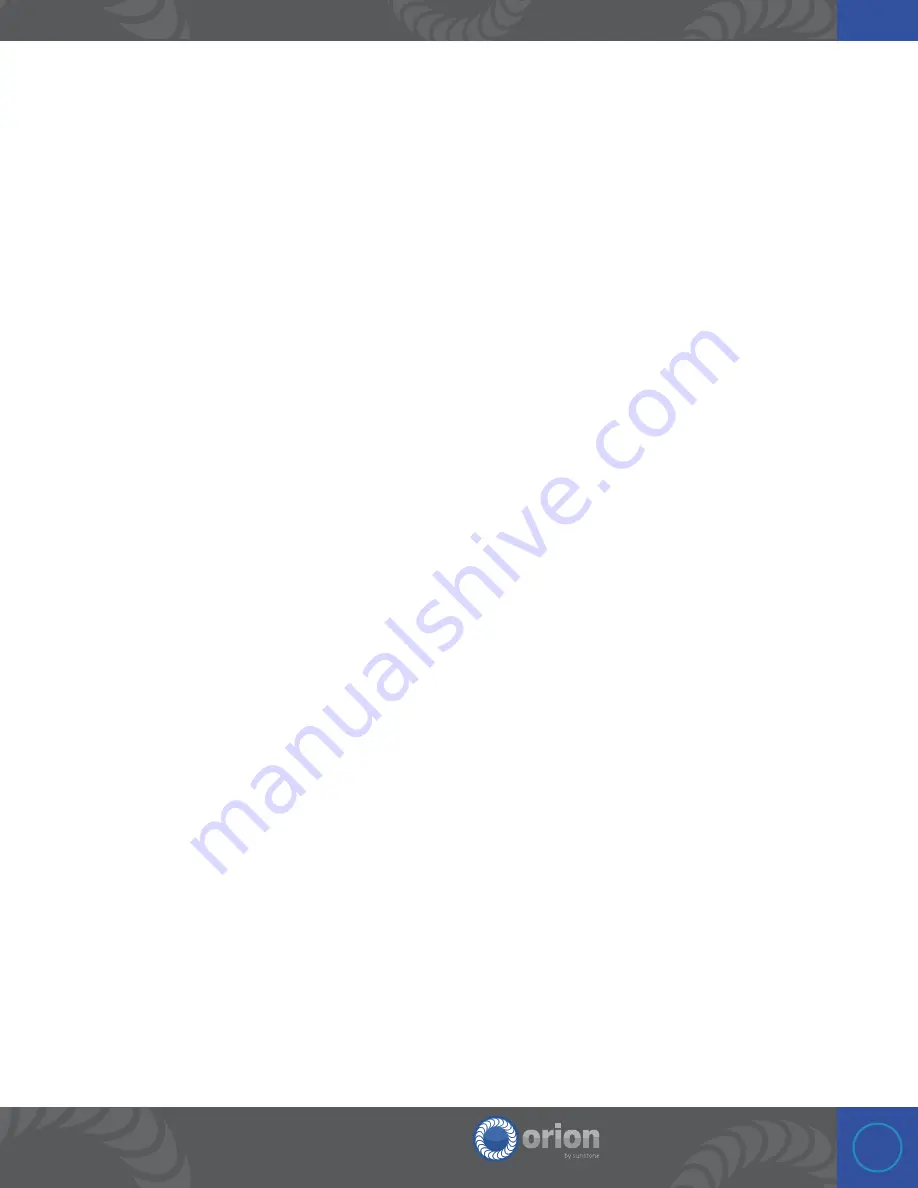
3
35
40
43
46
48
Chapter 7: Maintenance
7.1: Clean or Replace the Protection Lens
7.2: Realigning the Cross hairs
7.3: Periodically Change the Cooling Water
7.4: How to Remove the Water
7.5: How to Refill the Cooling System
Chapter 8: Error Messages and Troubleshooting
8.1: Other Anomalies
Chapter 9: Safety Systems
9.1: Resonator Shutter
9.2: Microscope Shutter
9.3: Microscope Infrared Filter
9.4: Weld Chamber Infrared Filter
9.5: Leather Strips Protecting the Chamber Opening
QUICK LASER PARAMETERS
Chapter 10: Quick Setup
10.1: COMBO 200 QUICK SETUP
10.2: LASER WELDER SAFTY BASICS
Summary of Contents for Combo 200
Page 1: ...Orion Laser Welder User Manual Orion Combo 200 ...
Page 4: ...4 ...
Page 7: ...7 ...
Page 52: ...52 ...