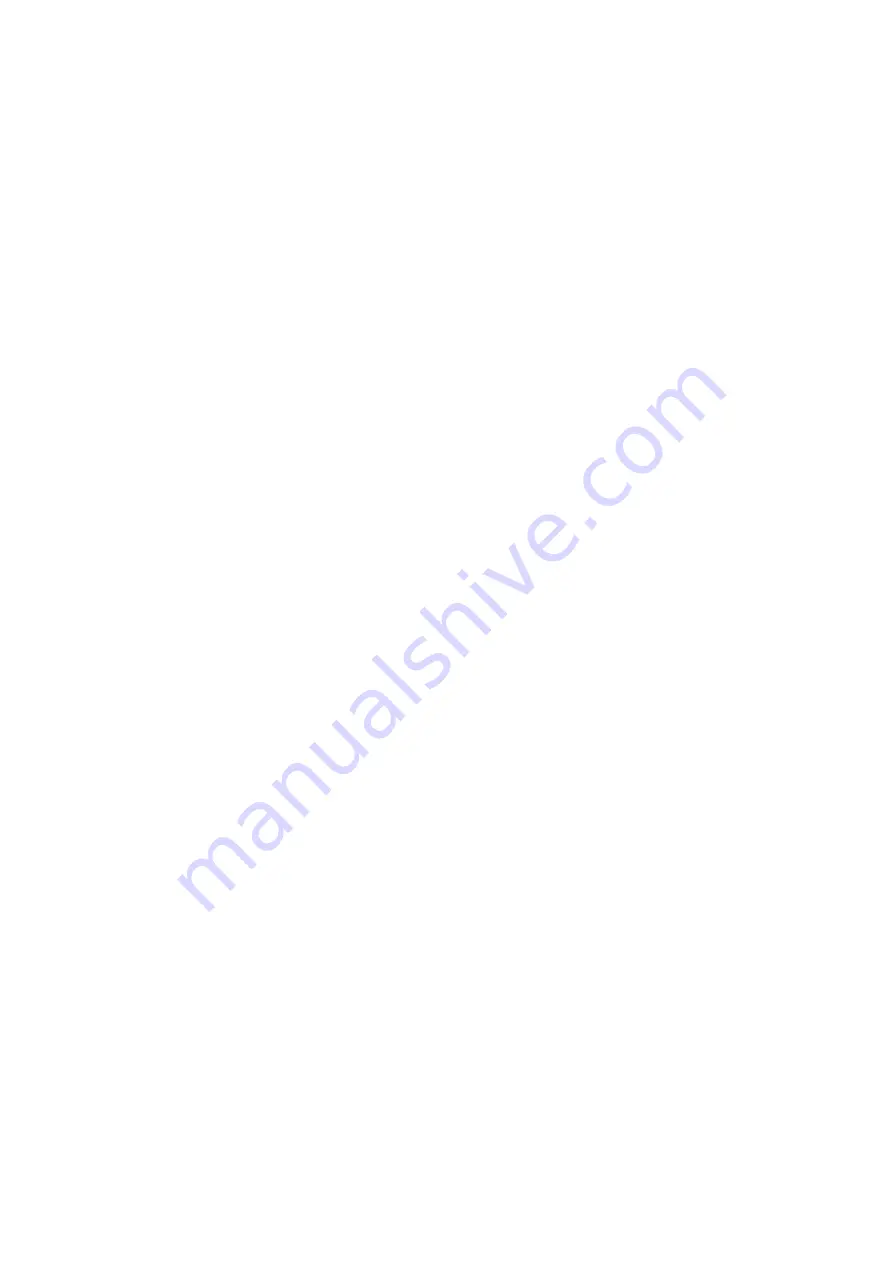
MACHINE MAINTENANCE
All general information about machine maintenance is based on normal machine working conditions:
indoor, moderate dust and low moisture environment, and maximum rotation of 32 RPM of
turntable/rotary arm. They should be regarded as guidelines, reviewed and corrected according to
requirements of actual use and conditions.
MOTOR MAINTENANCE
An occasional inspection of the brushes should be made in order to establish a wear rate.
Replacement brushes should be installed before old brushes wear to 9/16” long, measured on the
long side. After replacing brus hes run the motor near rated speed for at least 1/2 hour with no load to
seat the new brushes.
Failure to properly seat the new brushes may cause commutator damage and rapid wear of the new
brushes. If the commutator becomes rough, scored or out of shape, a competent motor shop should
disassemble it and resurface the commutator.
With every third brush change, have a competent motor shop resurface the commutator and blow the
carbon dust out of the motor.
REDUCER OIL CHANGE
All external cap screws and plugs on the reducing transmission should be checked for tightness after
the first week. It is recommended to change the oil every six months or at least 1800 hours of
operation, whichever comes first. When adding or changing oil, the transmission should never be
filled above the oil level mark indicated, because leakage and overheating may occur. Below is the
list of the type of lubricant that should be used.
List of recommended reducer oils
Manufacturer Lubricant
American Oil Co American Cyl Oil no: 196-L
Cities Service Oil Co. Citgo Cyl Oil 100-5
Gulf Oil Corp. Gulf Senate 155
Mobil Oil Corp. Mobil 600 W Suer-r Cyl. Oil
Philips Oil Corp. Andes S 180
Texaco Inc. 624 + 650T Cyl.Oil
Shell Oil Co. Velvata Oil J82
Union Oil of Cal. Red Line Worm Gear Lube 140
RING BEARING MAINTENANCE (when applicable)
The ring bearing (located under the turntable) s hould be re-lubricated internally and externally.
Internally:
by injecting grease into all the lubrication nipples in succession until a collar of fresh
grease appears around the perimeter of the ring. The re -lubrication interval suggested for these
bearings, used in Stretch Wrapping Machinery is 750 hours, with a maximum period of 6 months. The
lubricant should be fresh and applied in sufficient quantities to make sure all surfaces are lubricated.