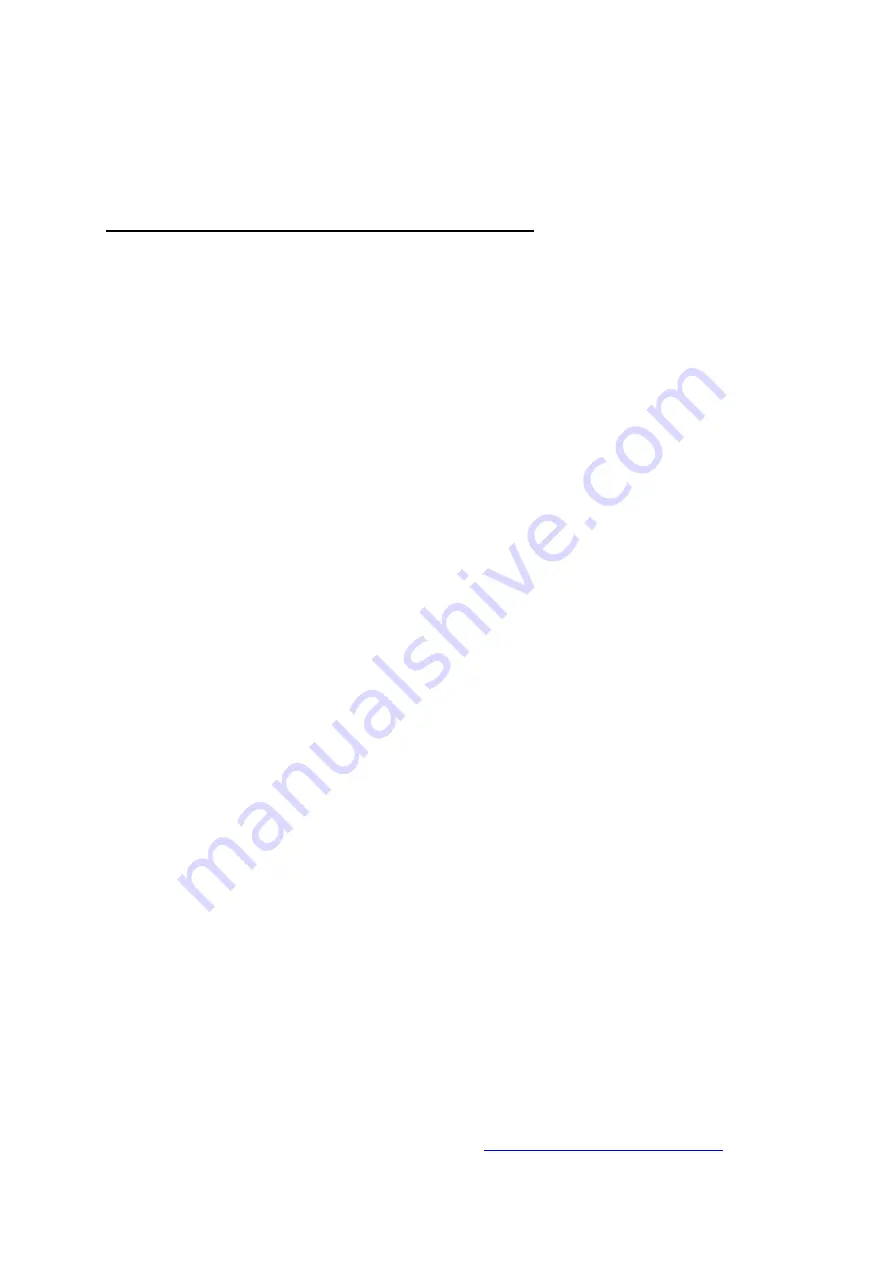
ORION PACKAGING SYSTEMS INC.
SEMI-AUTOMATIC SPECIFICATIONS - EFFECTIVE SEPTEMBER 1st, 2000
REVISED APRIL 2001
ORION MODEL MPA66
Medium Duty Automatic Rotary Tower System (conveyorless)
Maximum Load Size
48”W x 48”L x 80”H
Minimum Load Size
30”W x 30”L x 26”H
Weight Capacity
Unlimited (Floor Loaded)
Production Capacity
Contact Orion for a Throughput Calculation Specific to your application
Utilities
115/1/60 30 Amp Service
3 CFM Compressed Air @ 80 PSI
Rotary Tower
20” Diameter Precision Ring Bearing Tower Support
Structural Steel Tube Design
Easy Access to all components
Tower Drive
Heavy Duty ANSI Chain & Sprocket Drive
0 - 12 RPM Variable Tower Speed
Electronically Adjustable Acceleration/Deceleration (Soft Start)
Variable Speed Drive Motor
Positive Home Position Alignment Feature
Control Features
Free Standing, CSA Approved, NEMA 12 Control Panel
State-of the-Art Allen Bradley Programmable Logic Control for maximum
Flexibility
User Friendly Controls with Non-Proprietary Pushbuttons and Switches
Load / Personnel Safety Stop Photocell System
Electronic Film Tension Control Adjustment on the Panel
End of Cycle Film Force Release
Separate Top and Bottom Wrap Count Selectors
Variable Speed & Separate Film Carriage Up/Down Controls
Photocell for Automatic Load Height Detection
Rewrap Pushbutton for Rewrapping Load After Film Roll Replacement, E-Stop, Etc.
Tower Jog Pushbutton
Current Overload Protection
Film Delivery
20” Orion Insta-Thread Powered Prestretch Film Delivery System
Precision Ground, Polyurethane Pre-Stretch Rollers for Consistent, Maximum Film Yield
245% Standard Pre-Stretch Ratio (Adjustable from 100% to 425%)
Easy & Safe to Operate Self-Threading Carriage Design
Electronic Film Tension Control Adjustment on the Panel
Full Authority Film Dancer Bar with Variable Speed Output (Non-Wearing Sensor)
Heavy Duty ANSI Chain & Sprocket Ratio Control
Insta-Sense Film Broken/Out Sensing Logic with Indicator Light
Ultra-Low Wrap (Film Web to within 2” of Floor Dependent Upon Film Type/Tension)
Film Carriage Drive
Heavy Duty ANSI Chain Carriage Lift
Variable Speed Drive Motor
Multi-Point UHMW Precision Carriage Guidance System
6’ High Expanded Metal Safety Fence on Non-Operating side of System
Visit our Distributor Support Website at
www.support.orionpackaging.com