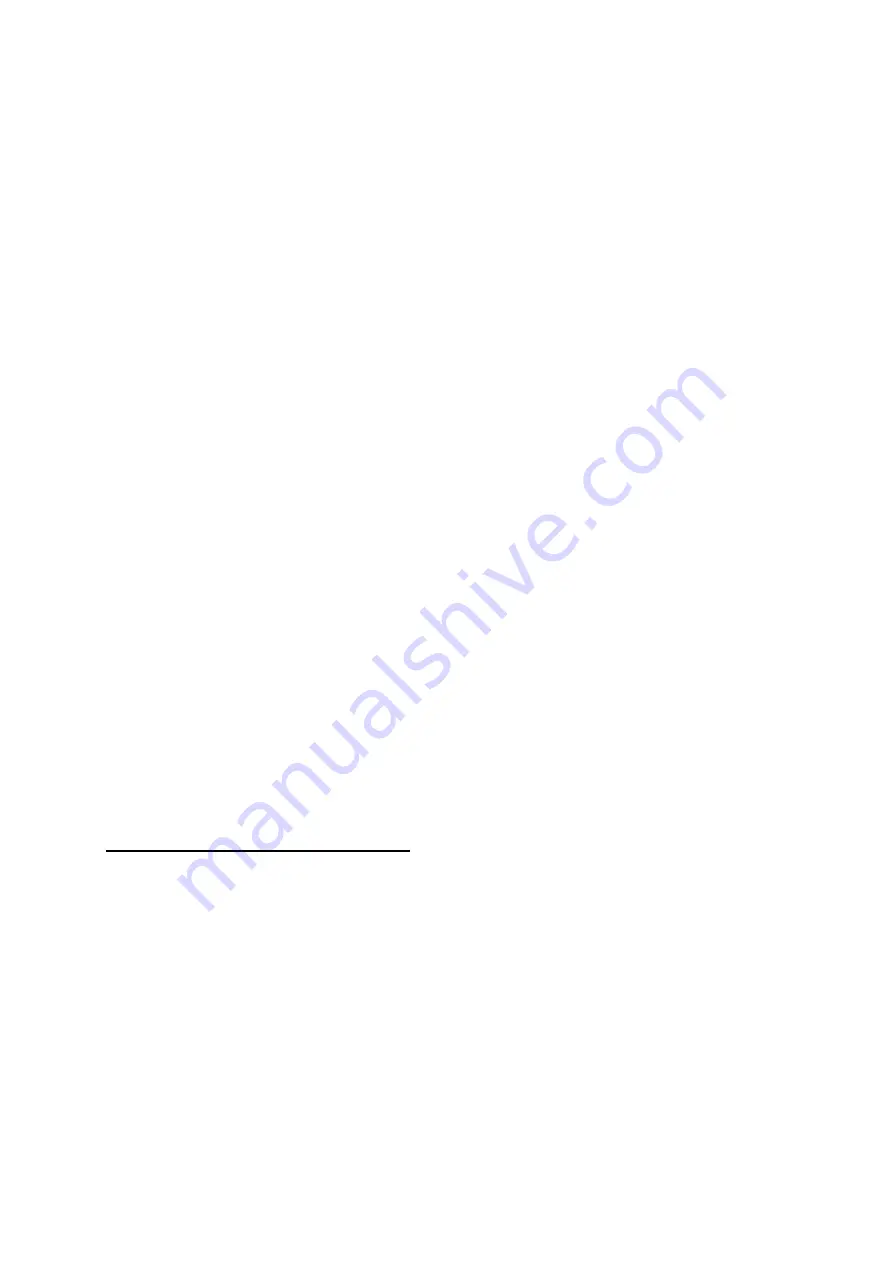
PROXIMITY SWITCH
Proximity Switch
is located under the turntable next to the lock, or on the perch (“MA” type
machine). Its purpose is to monitor the turntable or rotary arm position, and to signal the
controller every time the turntable or rotary arm passes the home position. The proximity
switches proper adjustment ensures that turntable or rotary tower will stop in the correct
position for the lock to be activated (only turntable machine).
CAUTION:
The Proximity Switch is factory adjusted and should not need any further
adjustment unless it has been disturbed.
SYSTEM START -UP
Notice: It is advisable to test-run the equipment with several pallet loads before make the
attempt to wrap with film. Please position a worker at the EMERGENCY STOP push button.
Start up of the machine (system) may determine the need for the adjustment of:
- Pallet sensor eyes (automatic systems only)
- Load height stop photoswitch (on the carriage)
- Conveyor acceleration/deceleration
- Turntable speed &jog speed
- Turntable speed acceleration/deceleration
- Turntable home position (rotary tower home position)
- Film tail treatment devices (automatic systems).
MACHINE WRAPPING TEST
Before the test procedure adjust the wrapping cycle parameters i.e. top
wraps, bottom wraps, height photocell o n/off, film tension, carriage speed
(those two parameters may be adjusted during the wrapping cycle).
When there is no photocell, verify the top limit switch position.
Film Cutter
Film Cutter Temperature Adjustment
Note:
The temperature of the Film Cutter is factory preset at -250°F (12O’C). Under normal
conditions, the temperature of the Film Cutter should
not require
field adjustment.
However, when additional adjustment is needed the following should be observed:
To increase temperature turn the adjus tment screw of the thermal switch counterclockwise.
The thermal switch is accessible from the bottom of the Film Cutter.