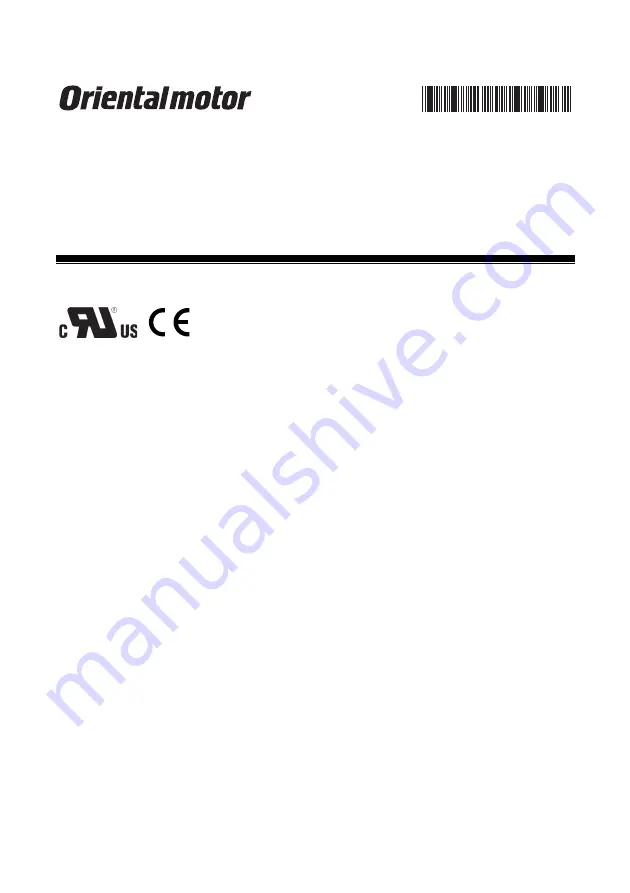
HP-7445-4
2-Phase Stepping Motor Unit
!
RBK
Series
OPERATING MANUAL
Thank you for purchasing an Oriental Motor product.
This Operating Manual describes product handling procedures and safety precautions.
!"
Please read it thoroughly to ensure safe operation.
!"
Always keep the manual where it is readily available.
Table of contents
1
Introduction .................................. 2
2
Safety precautions ....................... 4
3
Precautions for use ...................... 7
4
Preparation................................... 8
4.1
Checking the product ..................... 8
4.2
Combinations of motors and
drivers ............................................ 8
4.3
Names and functions of parts......... 9
5
Installation ...................................11
5.1
Location for installation................. 11
5.2
Installing the motor ....................... 12
5.3
Installing a load ............................ 13
5.4
Permissible overhung load and
permissible thrust load ................. 14
5.5
Installing the driver ....................... 14
5.6
Installing and wiring in compliance
with EMC Directive....................... 18
6
Connection ................................. 21
6.1
Connection example .................... 21
6.2
Connecting the power supply ....... 24
6.3
Connecting and grounding
the motor ...................................... 25
6.4
Grounding the driver .................... 29
6.5
Connecting the I/O signals ........... 30
6.6
About input/output signals............ 31
6.7
Timing chart.................................. 35
7
Settings .......................................36
7.1
Smooth drive function................... 36
7.2
Anti-resonance function................ 37
7.3
Third harmonic waveform
correction function........................ 37
7.4
Step angle .................................... 38
7.5
Motor current................................ 38
8
Protective functions.....................40
8.1
Descriptions of protective functions
and numbers of LED blinks .......... 40
8.2
How to clear a protective
function ........................................ 40
9
Inspection....................................41
10
Troubleshooting and remedial
actions ........................................42