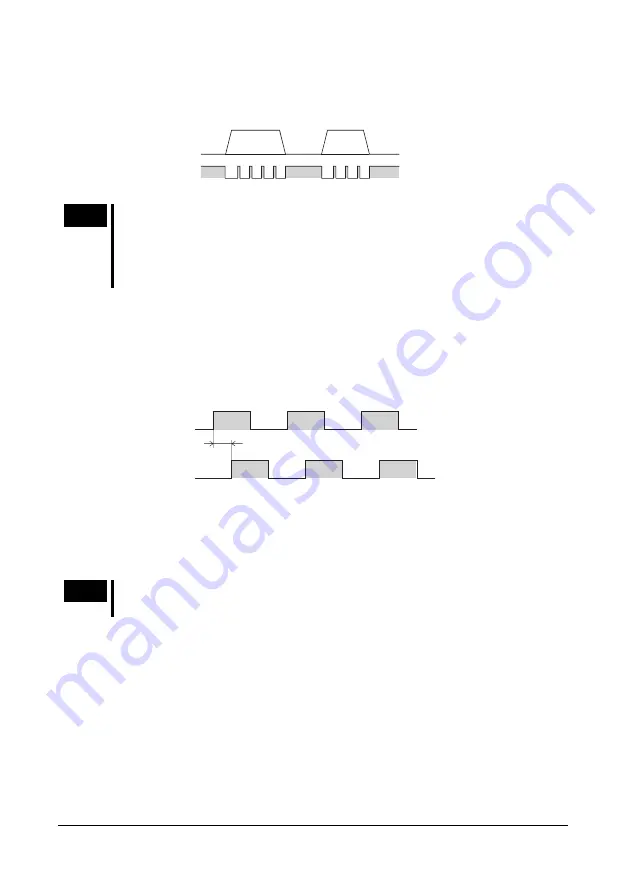
6 Connection
-
38
-
•
TIM.1 (timing) output
TIM.1 output turns “ON” whenever the output table rotates 0.4°.
Actuator movement
TIM.1 output
(Timing)
ON
OFF
Movement
Stop
Movement
Stop
Note
If TIM.1 output is to be detected, set the pulse speed at 500 Hz or less.
Use the ×10 input to switch the resolution only when TIM.1 output is in the
“ON” state and the actuator stops. If the resolution is switched under any
other conditions, TIM.1 output may not turn “ON” even when the output
table has rotated 0.4°.
•
ASG1 output and BSG1 output
ASG1 and BSG1 outputs are available in transistor open-collector output.
The output-pulse resolution will be the same as the motor resolution at the time
power is supplied to the driver (as set by the resolution select switch).
The resolution of the output table is 18 times the motor resolution. Counting the
ASG1 output pulses allows the motor position to be monitored.
ASG1 output
ON
OFF
ON
OFF
BSG1 output
90°
ASG1 output: Outputs pulse while the actuator operates.
BSG1 output: Detects the direction of actuator rotation. It has a 90° phase
difference with regard to ASG1 output. The level of BSG1 output at
the rise time of ASG1 output indicates the direction of actuator
rotation.
Note
The pulse-output delays behind actuator rotation by up to 1 ms.
The output may be used to verify the actuator’s stop position.
Summary of Contents for ASD10A-K
Page 51: ......