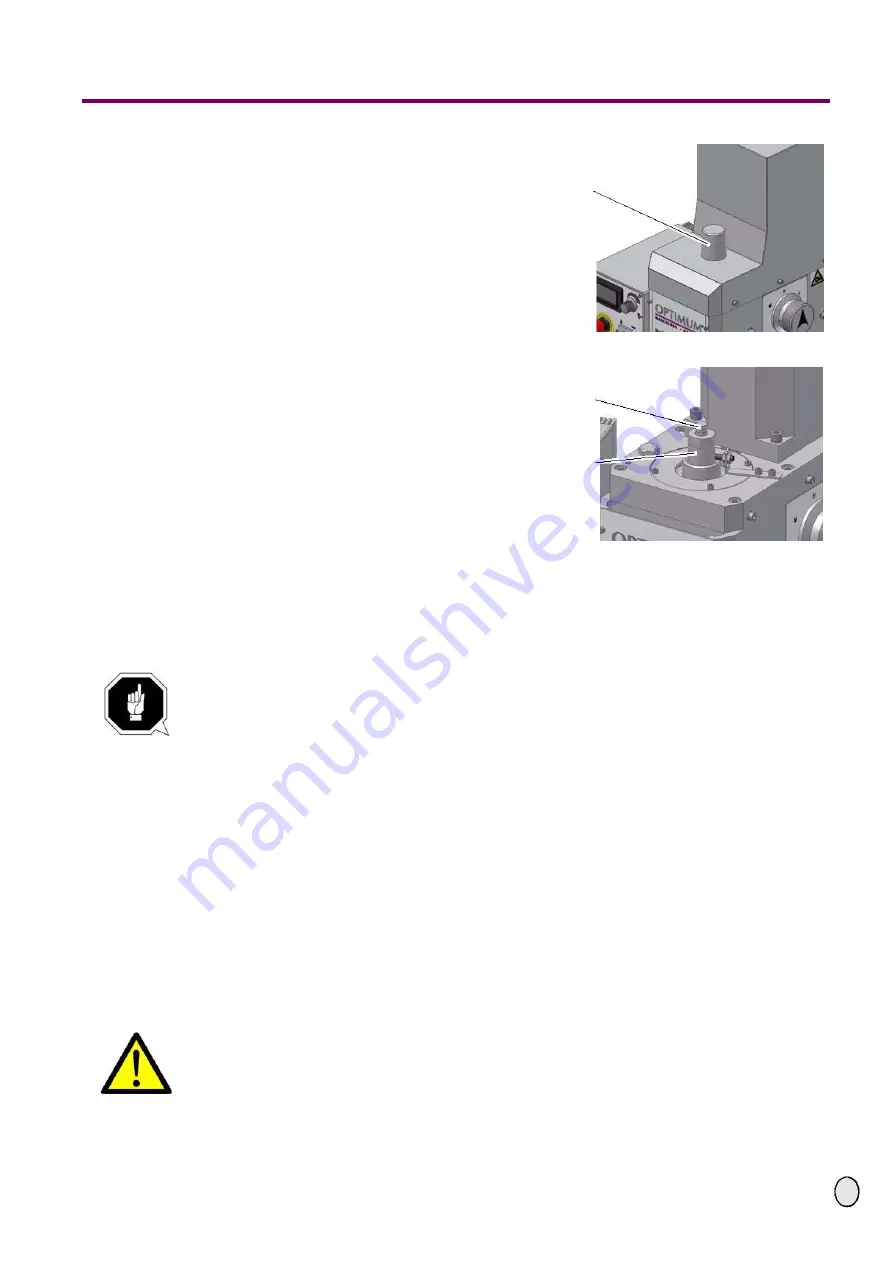
OPTIMUM
Operation
M A S C H I N E N - G E R M A N Y
Remove the cover.
Clean the seat in the milling spindle
/ spindle sleeve.
Clean the taper of your tool.
Insert the tool into the holding fixture
/ spindle sleeve.
Cover
Illustr. 4-3: Drill-Mill head
Screw the draw-in rod into the tool.
Tighten the tool with the draw -in rod
and hold the spindle onto the end
sup-port with a key.
Draw-in rod
End support /
thrust bearing
Illustr. 4-4: Drill-Mill head without hood
4.5.2
Disassembly
Hold the spindle thrust bearing with a wrench and loosen the draw-in rod. Turn the draw-
in rod further, so that the tool is squeezed out from the cone admission.
ATTENTION!
When using an MT 3 spindle.
When installing a cold morse taper into a heated-up machine those MT seats tend to
shrink on the morse taper contrary to the quick-releaser tapers.
4.5.3
Use of collet chucks
When using collet chucks for the reception of milling tools, a higher operation tolerance can be
achieved. The exchange of the collet chucks for a smaller or larger end mill cutter is performed
simply and rapidly and it is not necessary to disassemble the complete tool. The collet chuck is
pressed into the ring of the swivel nut and must rest there by itself. The milling cutter is clamped
by fastening the swivel nut on the tool.
Make sure that the correct collet chuck is used for each milling cutter diameter, so that the mil-
ling cutter may be fastened securely and firmly.
„Optional accessory“ on page 20
4.6
Clamping the workpieces
CAUTION!
Injury by flying off parts.
The workpiece is always to be fixed by a machine vice, jaw chuck or by another
appro-priate clamping tool such as for the clamping claws.
Page 24
Drilling-Milling machine
BF 30 Vario
Version 1.0.3
Stand 16 / 09 / 2008
2008
GB