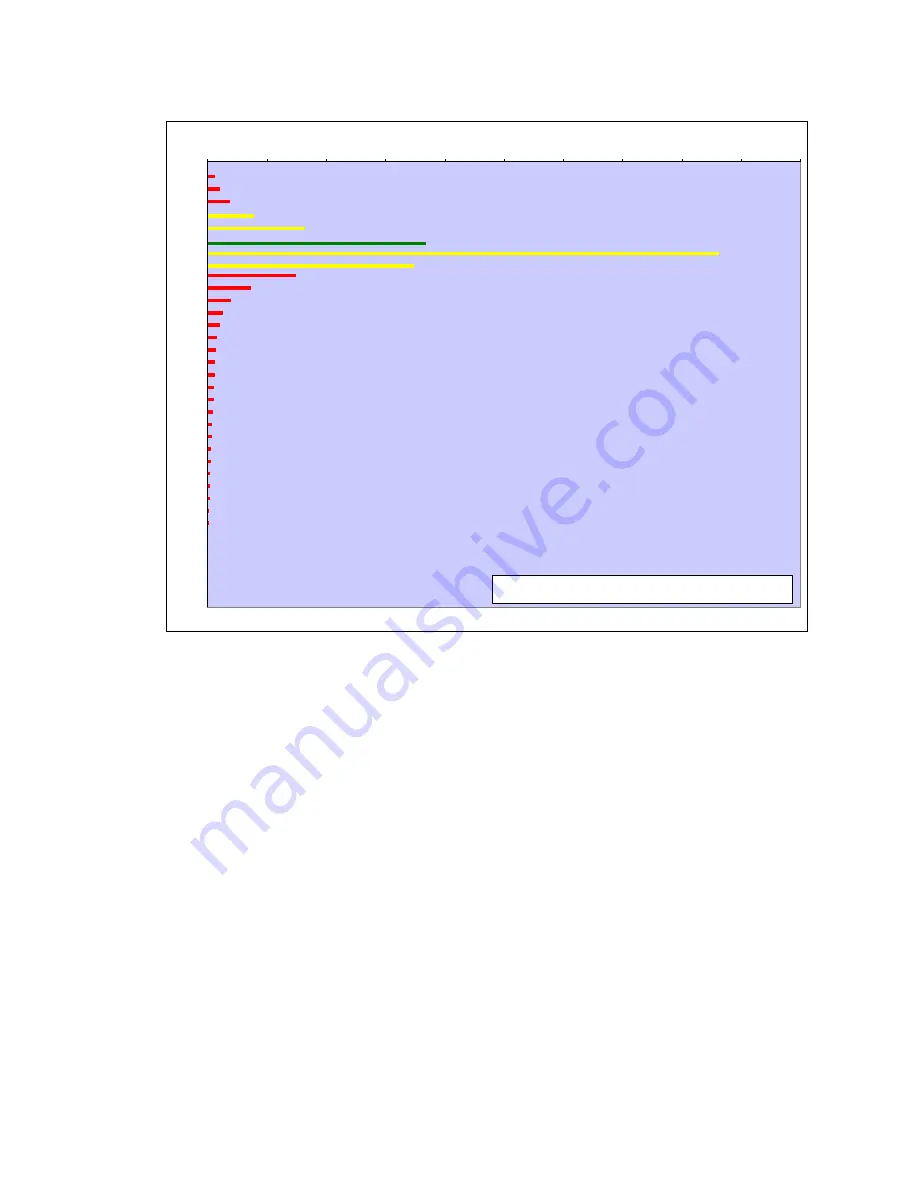
6212C Manual Version 15_22 Rev 07-19.docx
Page 19 of 53
Sample Alignment Aid Graph
Lasercheck Alignment Data
0.0
0.2
0.4
0.6
0.8
1.0
1.2
1.4
1.6
1.8
2.0
0
1
2
3
4
5
6
7
8
9
10
11
12
13
14
15
16
17
18
19
20
21
22
23
24
25
26
27
28
29
30
31
32
33
34
35
D
e
te
c
to
r N
u
m
b
e
r
Detector Voltage
HORIZONTAL ALIGNMENT VALUE = 4.609