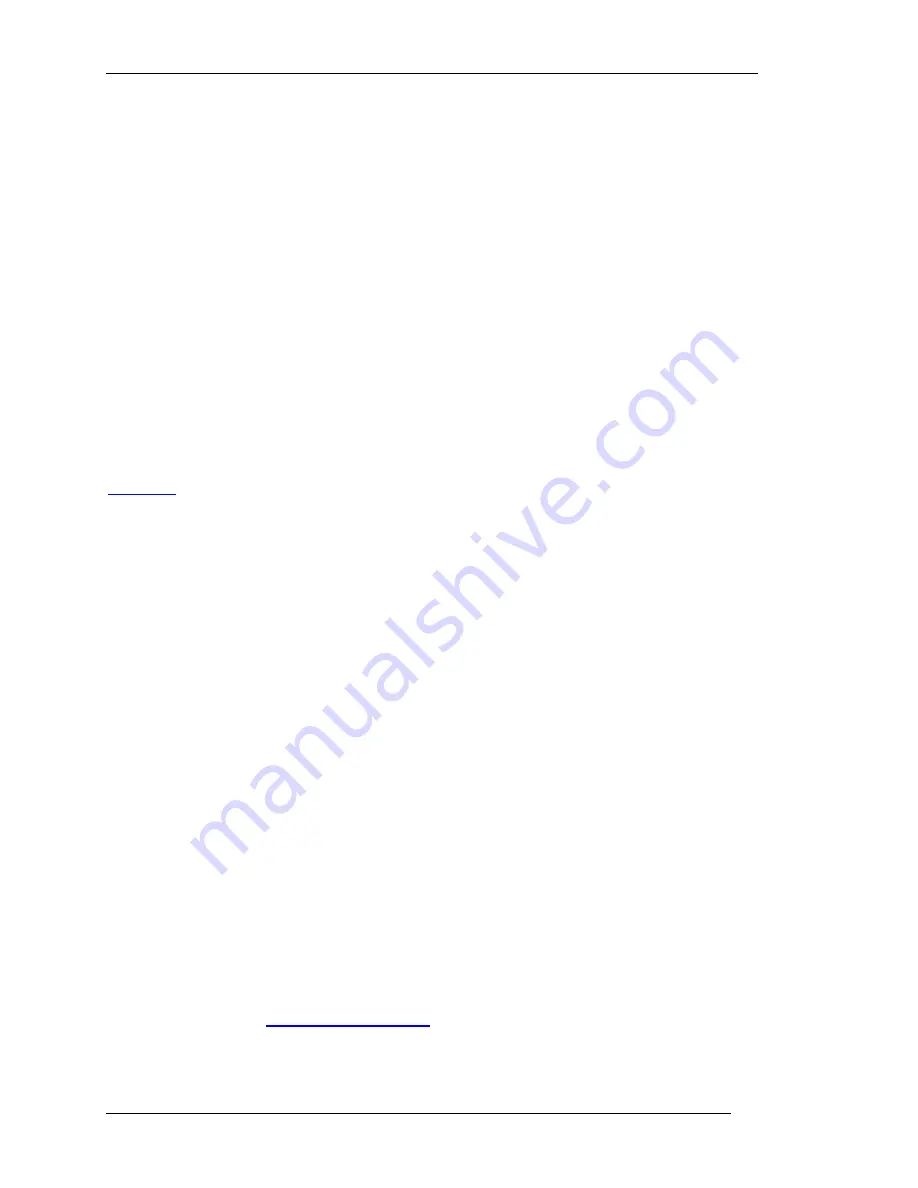
CONTROL SIGNAL INTERFACE
HOME PROCEDURES
MAXnet User’s Manual
4-6
4.7. ENCODER
FEEDBACK
Incremental encoder feedback is provided for all axes. Encoder feedback is required for each
servo axis. Its use is optional for stepper axes. The MAXnet encoder feedback accepts
quadrature pulse inputs from high resolution encoders at rates up to 16 MHz (after quadrature
detection). When used with stepper motors, the encoder monitors the actual position through the
encoder pulse train. On servo axes it continuously provides input to calculate the position error,
adjust for it through the PID filter, and change the output accordingly. The stepper axes can
monitor the error and correct and maintain the position after the move is finished.
The encoder input can also be used as an independent feedback source or, in the encoder
tracking mode, to mimic an activity. All modes are capable of slip or stall detection and encoder
tracking with electronic gearing. These options are selectable by the user through software
commands.
The MAXnet is compatible with virtually any incremental encoder which provides quadrature
outputs. Times four quadrature detection is used to increase resolution. This means that an
encoder rated for 1000 counts (or lines) per revolution will result in 4000 counts of quadrature
encoded input for each encoder shaft revolution. The inputs are compatible with encoders, that
have single ended or differential TTL outputs. The MAXnet has differential line receivers to
accommodate encoders with differential outputs. Encoders with single-ended outputs can wire
the signals to the plus(+) side of the differential line receiver and ground the minus(-) side (see
4.8. HOME
PROCEDURES
Two logical input functionalities are provided to synchronize the physical hardware with the
MAXnet controller; i.e. put the controlled motor in the home position.
The home switch input is a TTL level input signal. If current limiting is required, it should be done
externally to the board. Contact OMS Motion, Inc. technical support for assistance.
The MAXnet home switch input can be used to physically home a mechanical stage. When this
functionality is used the axis position counter will be reset to a selected value when the switch is
activated. At this point the MAXnet can either ramp the axis to a stop or stop the axis
immediately. The control of the direction of travel, the logic active state and the response to the
active switch are controlled through commands.
The other homing method on the MAXnet uses the home switch and the encoder signals to home
a motor. When using the Home Encoder Index (HI) mode, the homing logic is used with these
input signals. The home position consists of the logical AND of the encoder index pulse, the
home switch input, and a single quadrant from the encoder logic. The home switch and encoder
should be positioned relative to each other in such a way that there is only a single location in the
entire travel of the axis that creates a true condition for the defined home logic. The HT and EH
commands can be used to create different patterns for the home logic, including the option to
ignore an encoder phase signal. The default home logic expressed in Boolean terms is:
Home = Phase +A * Phase -B * Index * Home Switch (Default)
It is necessary that the above quadrant occur within the index pulse as provided by the encoder
for this logic to function properly. It may be necessary with some encoders to shift the phase of
this quadrant by inverting one or both of the phases. Inverting one phase or swapping Phase A
for Phase B will also reverse the direction. The encoder counter (read by a RE/PE commands)
must increase for positive moves or the system will oscillate due to positive feedback. For other
options, please contact
Summary of Contents for MAXnet
Page 4: ...TABLE OF CONTENTS MAXnet User s Manual ii This page is intentionally left blank ...
Page 46: ...STAND ALONE COMMANDS MAXnet User s Manual 6 2 This page intentionally left blank ...
Page 48: ...SERVICE MAXnet User s Manual 7 2 This page intentionally left blank ...
Page 58: ...LIMITED WARRANTY APPENDIX A MAXnet User s Manual This page intentionally left blank ...
Page 60: ...RETURN FOR REPAIRS APPENDIX B MAXnet User s Manual This page intentionally left blank ...