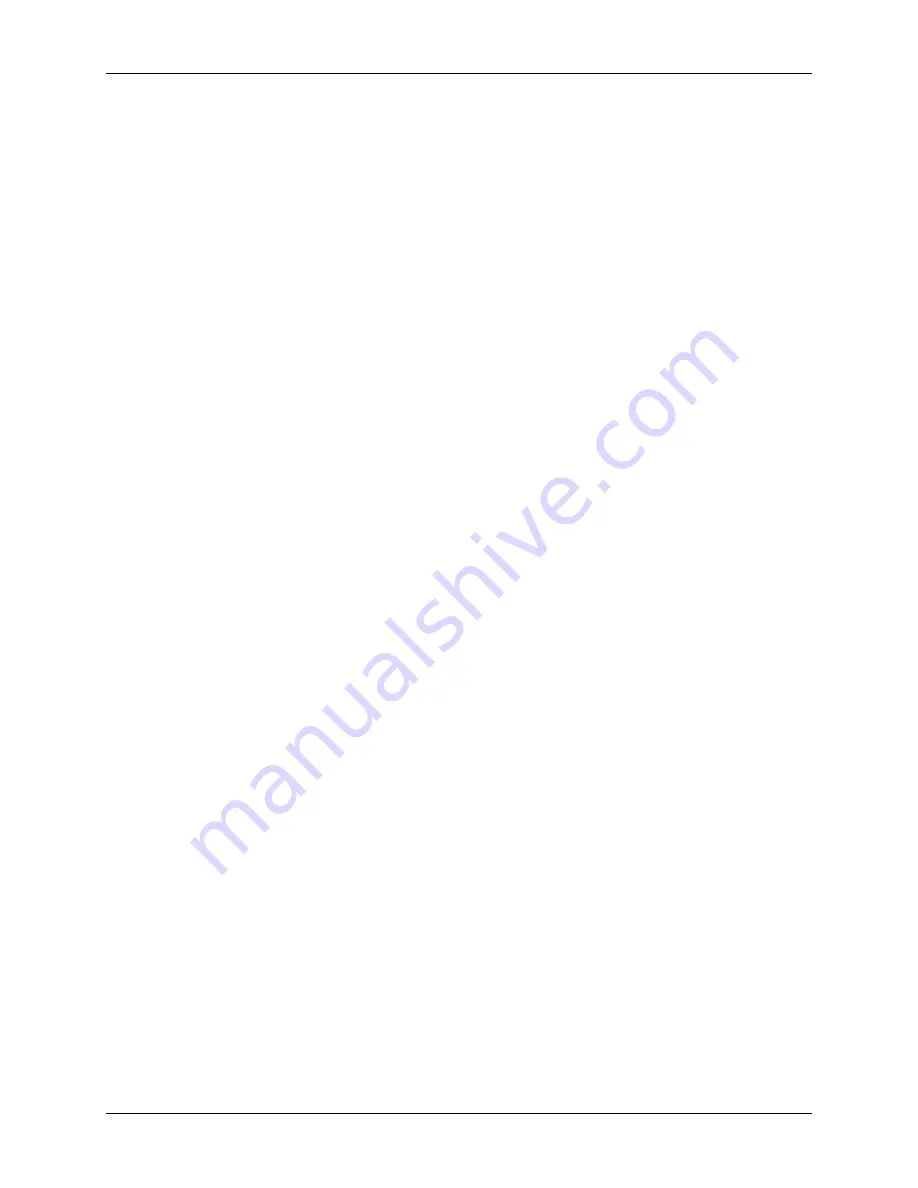
GETTING STARTED
TUNE THE SYSTEM
2-10
MAXnet User’s Manual
b) Set the signal/command gain of your amplifier to its minimum setting.
c) Send the “KO3277;” command to the MAXnet and observe the velocity of the motor. The
output of MAXnet will be near 1VDC.
d) If the motor does not move at all, your amplifier does not work well at a low velocity. In this
case, adjust the signal/command gain of the amplifier to approximately 20% of maximum or
until the motor begins to move.
e) Using a frequency meter, measure the pulse rate of Phase A of the encoder. The frequency
measured is ¼ of the actual pulse rate.
f) Adjust the signal/command gain of the amplifier until the pulse rate of Phase A is
approximately 10% of your desired peak operational velocity. If the pulse rate is already
greater than 10% of peak, your amplifier is not designed for low velocity motion and you will
likely have some difficulty tuning your motors.
g) Send the “KO-3277;” command to the MAXnet and recheck the velocity. You may need to
readjust your amplifier. If so, do not reduce the signal/command gain – only increase the
setting as needed. Increasing the gain will not impair the forward peak velocity but reduction
will.
h) Send the KO command with the “zero” value to the MAXnet.
5) Verify the direction of your servo encoder:
a) Send the “LP0; KO2000;” command to the MAXnet.
b) Send the “RE;” command to the MAXnet and observe the response.
c) If the response is positive, no further action need be taken; go to step 6.
i) If the response is negative, your encoder or analog output must be reversed use one of
the methods below.
ii) Use EDI/EDN to invert/normalize encoder direction or
iii) Use SVP-/SVP+ to invert/normalize PID analog output (inverts values of KO and KOD) or
iv) if your incremental encoder produces a differential signal, swap Phase B+ with Phase B-
and repeat from step (a.) above.
v) If your incremental encoder produces a single-ended (or TTL) signal, swap Phase A with
Phase B and repeat from step (a.) above.
d) If the RE response is still negative, contact OMS Technical Support for assistance.
6) Repeat from step 1 for the other servo axes.
7) Remember to set KO for each axis at every power-up unless you store the values in Flash.
NOTE: Most encoder problems are caused by lack of power or incorrect connections. If the encoder
position changes by only 1 count, this is an indication that one of the phases is not connected.
Do not proceed until you perform all the steps in this procedure, ensure that the outputs of the MAXnet
are as described, and ensure that the encoder is operating correctly.
Do not proceed until you perform all the steps in this procedure, ensure that the outputs of the MAXnet
are as described, and ensure that the encoder is operating correctly.
Summary of Contents for MAXnet
Page 4: ...TABLE OF CONTENTS MAXnet User s Manual ii This page is intentionally left blank ...
Page 46: ...STAND ALONE COMMANDS MAXnet User s Manual 6 2 This page intentionally left blank ...
Page 48: ...SERVICE MAXnet User s Manual 7 2 This page intentionally left blank ...
Page 58: ...LIMITED WARRANTY APPENDIX A MAXnet User s Manual This page intentionally left blank ...
Page 60: ...RETURN FOR REPAIRS APPENDIX B MAXnet User s Manual This page intentionally left blank ...