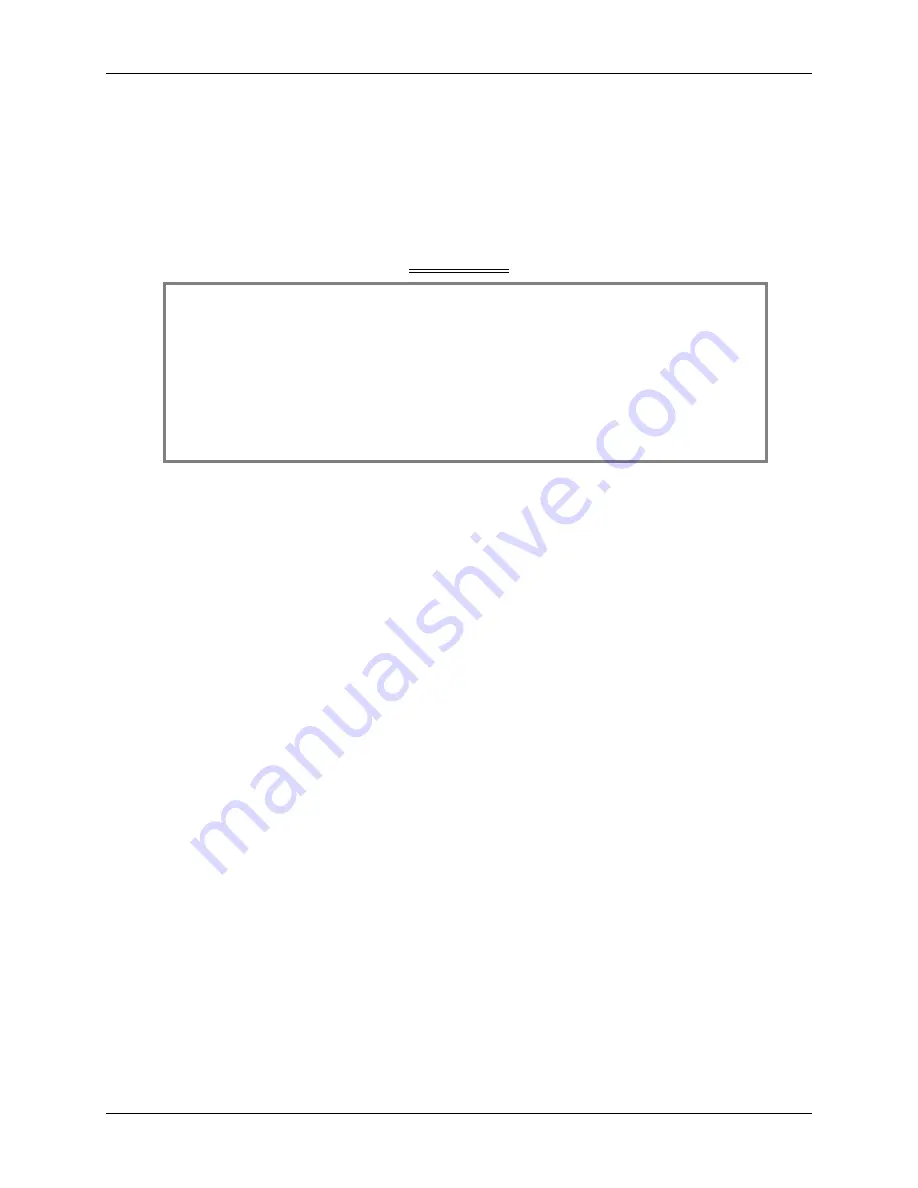
CONNECT AND CHECKOUT THE SERVO SYSTEM
GETTING STARTED
MAXnet User’s Manual
2-9
2.6.
CONNECT AND CHECKOUT THE SERVO
SYSTEM
Servo systems tend not to respond gracefully to connection errors. You can reduce the chance of making
connection errors by following a step-by-step procedure:
Caution
2.7.
CONNECT AND CONFIGURE THE
MOTOR/AMPLIFIER
1) Connect and configure your amplifier per the manufacturer’s instructions for “Torque” or “Open-
Loop” mode.
2) With the motor and amplifier power turned off, connect the MAXnet to the amplifier.
3) Balance your motor:
a) Configure the axis as a servo axis by sending the “PSM” command.
b) Using a voltage meter, verify that the command signal from the MAXnet is less than 500mV.
If it is not, send the command “KO0;” to the MAXnet and recheck the voltage. If the voltage is
still too high, contact OMS Motion, Inc.’s Technical Support department for guidance.
c) Turn on power to the amplifier and then to the motor.
d) Adjust the balance setting of your amplifier (if equipped) until the motor stops moving.
e) If the motor continues to revolve or your amplifier has no balance adjustment:
i) Send the command “KO100;” to the MAXnet.
ii) If the motor spins faster, reduce the command parameter and resend the command, e.g.
“KO50;”
iii) If the motor spins slower but does not stop, increase the command parameter and resend
the command, e.g. “KO150;”
iv) Continue adjusting and resending the KO command until the motor comes to rest. Write
down the final KO value for later reference as your “zero” setting.
4) Maximize your system’s usage of the MAXnet’s DAC (this method works only with incremental
encoders, skip it if you use absolute encoder only on that axis):
a) Connect the servo encoder to the MAXnet. (See section 4.4 on incremental encoder
feedback)
The servo motor may jump or spin at a very high velocity during connection
and configuration. The motor should be restrained by some means before
beginning this procedure. Keep hands and clothing clear of the motor and
any mechanical assemblies while performing this procedure.
It is recommended that the motor shaft not be connected to the physical
system until you are sure you have control over the motor.
Summary of Contents for MAXnet
Page 4: ...TABLE OF CONTENTS MAXnet User s Manual ii This page is intentionally left blank ...
Page 46: ...STAND ALONE COMMANDS MAXnet User s Manual 6 2 This page intentionally left blank ...
Page 48: ...SERVICE MAXnet User s Manual 7 2 This page intentionally left blank ...
Page 58: ...LIMITED WARRANTY APPENDIX A MAXnet User s Manual This page intentionally left blank ...
Page 60: ...RETURN FOR REPAIRS APPENDIX B MAXnet User s Manual This page intentionally left blank ...