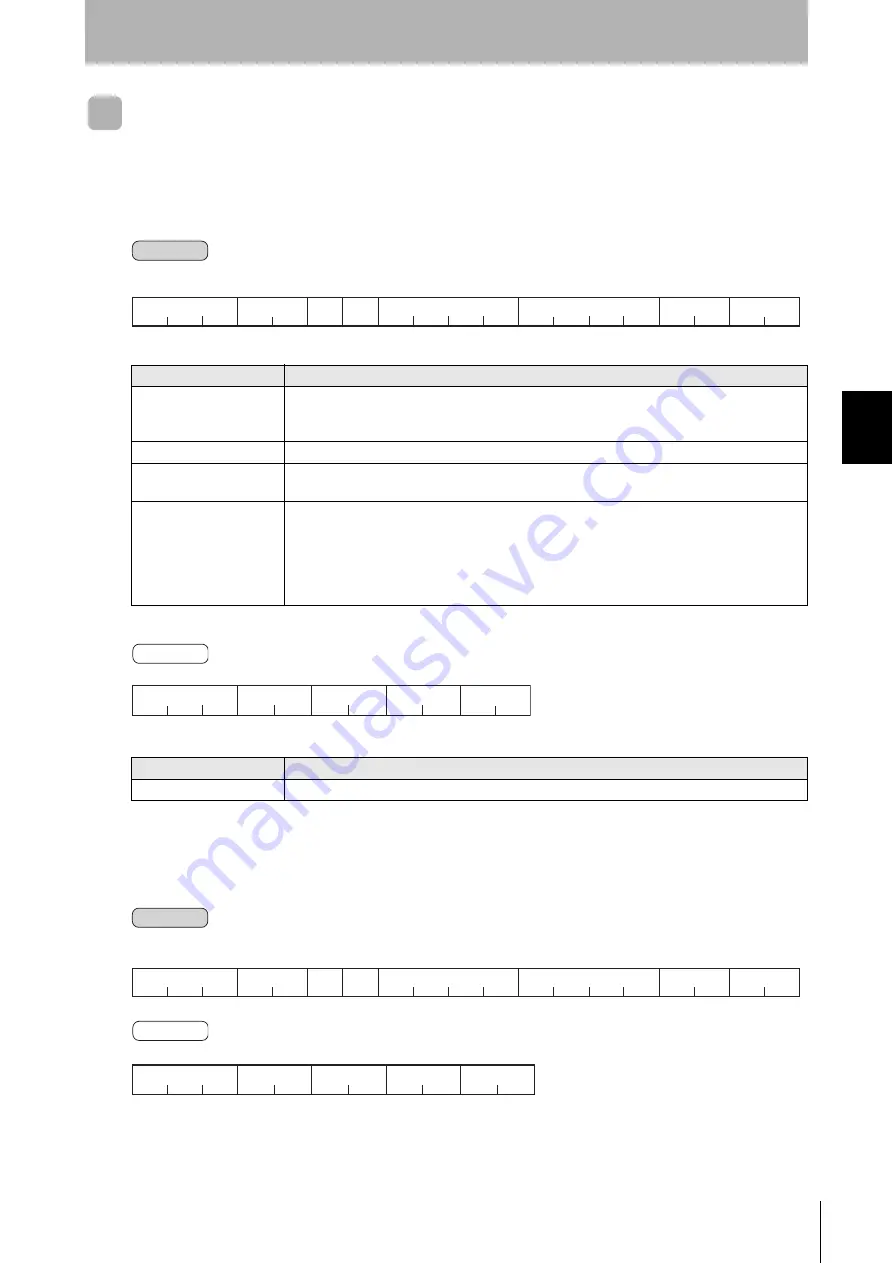
65
Heat-resistive RFID System
User's Manual
S
e
c
tion 4
Communic
a
tions
Comma
nds
Section 4
Reading from/Writing to Tags
AUTO WRITE (AW)
This command writes data to the Tag when the Tag enters the communications area. The Controller
returns a response when communications between the Controller and Tag has been completed. The
host device cannot send other commands until either a response is received or processing is aborted
using the COMMAND PROCESSING ABORT (AA) command.
• Example
Writing two bytes of data “1122” (hexadecimal code) from address 0010h of the Tag in the communica-
tions area to Controller No. 2.
Name
Details
Data type
Specifies the code format for sending the write data to the Tag.
A: ASCII
H: Hexadecimal code
Antenna designation
Always 1
Start address
Specifies the start address of the area to which data is to be written in 4-digit hexadecimal code.
Setting range: 0000h to 03E7h
Write data
Contains the data to be written to the Tag.
The number of bytes that can be written at one time is as follows:
Setting range
ASCII: 256 bytes (256 characters)
Hexadecimal code: 128 bytes (256 characters)
* When hexadecimal code is designated, specify two characters for each byte.
Name
Details
End code
Indicates the execution result for the command.
Command
×
×
A
W
×
×
×
×
A/H
1
×
×
2
1
1
4
2
@
×
×
3
*
CR
2
×
×
n
Data
type
Antenna
designation
Start address
Write data
FCS
Controller No.
Terminator
Command
code
Response
A
W
×
×
0
0
2
2
2
@
×
×
3
*
CR
2
End code
FCS
Terminator
Command code
Controller No.
Command
1
1
A
W
2
C
1
0
H
1
0
0
2
1
1
4
2
@
0
2
∗
CR
2
2
2
3
Data
type
Antenna
designation
Start address
Write data
FCS
Controller No.
Terminator
Command
code
Response
A
W
5
4
0
0
2
2
2
@
0
2
3
*
CR
2
End code
FCS
Terminator
Command code
Controller No.