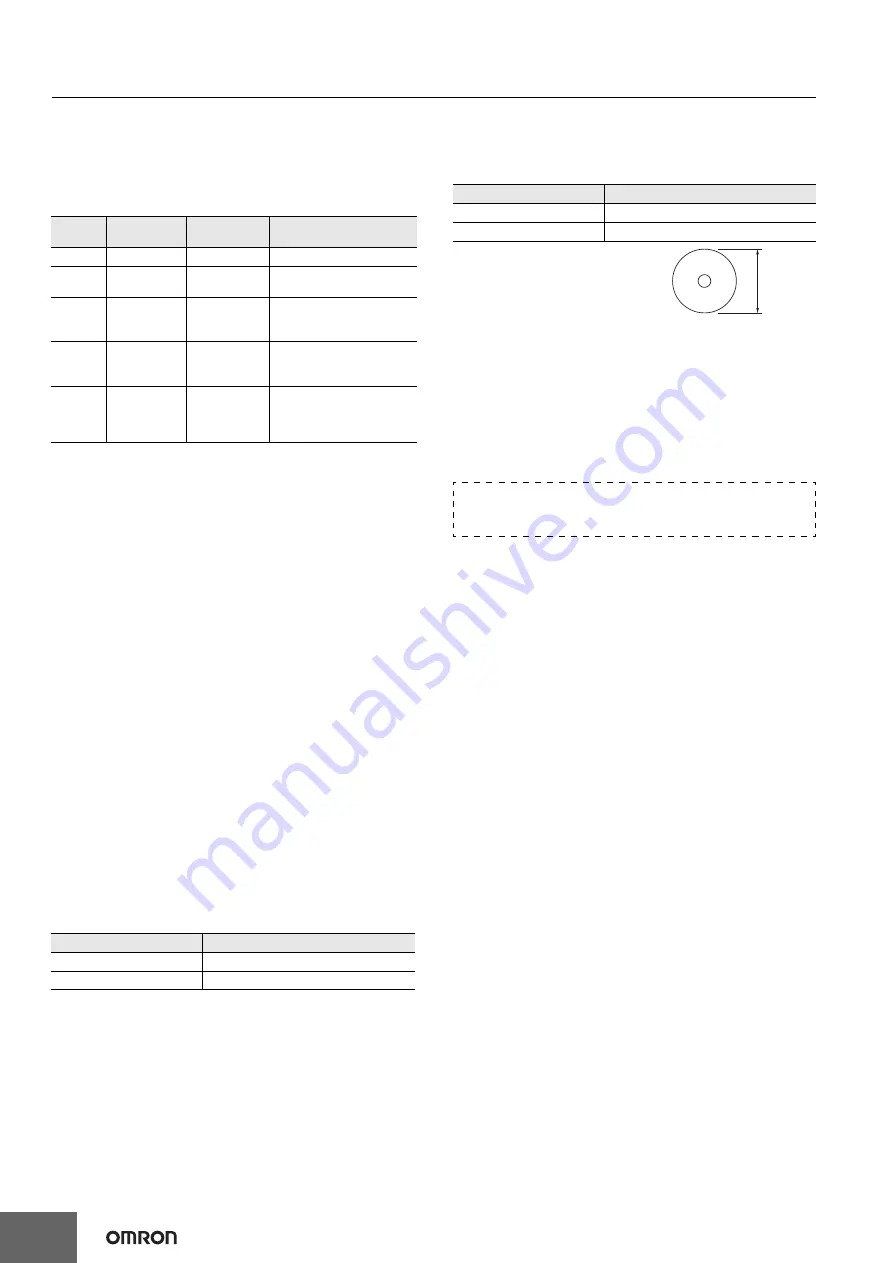
34
H7CC-A
@
tachometer
Explanation of Functions
Tachometer Operation
Tachometer Input Mode (
tinm
)
Set the count input mode to one of the following: 1 input (
F1
), 2 inputs
(
F2
), error (
F3
), absolute ratio (
F4
), or error ratio (
F5
).
Tachometer Output Mode (
totm
)
Set the output method for control output based on the comparison
value. Upper and lower limit (HI-LO), area (AREA), upper limit (HI-HI),
and lower limit (LO-LO) can be set.
(For details on the output modes, refer to
Output Mode Settings and
Operation
on page 38.)
Counting Speed (
cnts
)
Set the maximum counting speed (30 Hz/10 kHz) for CP1 input.
If contacts are used for input signals, set the counting speed to 30 Hz.
Processing to eliminate chattering is performed for this setting.
Decimal Point Position (
dp
)
Decide the decimal point position for the measurement value, OUT1
set value, and OUT2 set value.
Prescale Value (
pscl
)
It is possible to display the rate of rotation or the speed of a device or
machine to which the H7CC is mounted by converting input pulses to
a desired unit.
If this prescaling function is not used, the input frequency (Hz) will be
displayed.
It is also possible to specify time (seconds) as the display value. Refer
to
Display Unit
on page 35 for details.
The relationship between display and input is determined by the
following equation. Set the prescale value according to the unit to be
displayed.
Displayed value = f
×
α
f: Input pulse frequency (number of pulses in 1 second)
α
: Prescale value
(1) Displaying Rotation Rate
N: Number of pulses per revolution
Example: To display the rate of rotation for a machine that outputs 5
pulses per revolution in the form
@@
.
@
rpm:
1. Set the decimal point position to 1 decimal places.
2. Using the formula, set the prescale value (
α
) to 1/N
×
60 = 60/5 = 12.
(2) Displaying Speed
N: Number of pulses per revolution
d: Diameter of rotating body (m)
π
d: Circumference (m)
• Observe the following points when setting a prescale value.
Set the set value to a value less than {Maximum countable value
−
Prescale value}.
Example: If the prescale value is 1.25 and the counting range is
0.000 to 999.999, set the set value to a value less than 998.749 (=
999.999
−
1.25).
If the set value is set to a value greater than this, output will not turn
ON.
• Output will turn ON, however, if a present value overflow occurs
(FFFFFF}.
Averaging Method (
avgt
)
A simple average or moving average can be selected for the
averaging. With the moving average method, the average of the
measurement values is displayed each sampling cycle, in contrast to
a simple average, with which the the average of the set number of
samples is displayed.
Number of Averaging Times (
avgn
)
Flickering display and output chattering can be prevented using
average processing. Average processing can be set to one of four
levels: no average processing, 2 times (i.e., the average of 2
measurement values), 4 times, 8 times, or 16 times.
The measurement cycle will be equal to the sampling cycle multiplied
by the average processing setting (i.e., the number of times).
Average processing enables stable displays even for fluctuating input
signals. Set the optimum number of times for the application.
Auto-zero Time (
auto0
)
The display can be force-set to 0 if there is no pulse for a certain
period of time. This time is called the auto-zero time. Set the auto-zero
time to a time slightly longer than the estimated interval between input
pulses. Accurate measurement is not possible if the auto-zero time is
set to a time shorter than the input pulse cycle. Setting a time that is
too long may also result in problems, such as a time-lag between
rotation stopping and the alarm turning ON. The auto-zero time is not
applied to pulse width measurements.
Input
mode
Input
Internal
processing
Application
1 input
Count 1
None
Operation with only one input.
2 inputs
Counts 1 and 2 None
Operation with two
independent inputs.
Error
Counts 1 and 2
Count 1 input
−
Count 2 input
Measuring the difference
between two inputs (error in
number of revolutions).
Absolute
ratio
Counts 1 and 2
Count 1 input
÷
Count 2 input
Measuring the ratio of two
inputs (ratio of number of
revolutions).
Error ratio Counts 1 and 2
(Count 1 input
−
Count 2 input)
÷
Count 2 input
Measuring the ratio of error
for two inputs (measuring the
error ratio of number of
revolutions).
Display unit
Prescale value (
α
)
rpm
1/N
×
60
rps
1/N
Display unit
Prescale value (
α
)
m/min
π
d
×
1/N
×
60
m/s
π
d
×
1
/N
d: Diameter
of rotating
body (m)
Note:
If the prescale value setting is incorrect, a counting error will
occur. Check that the settings are correct before using this
function.