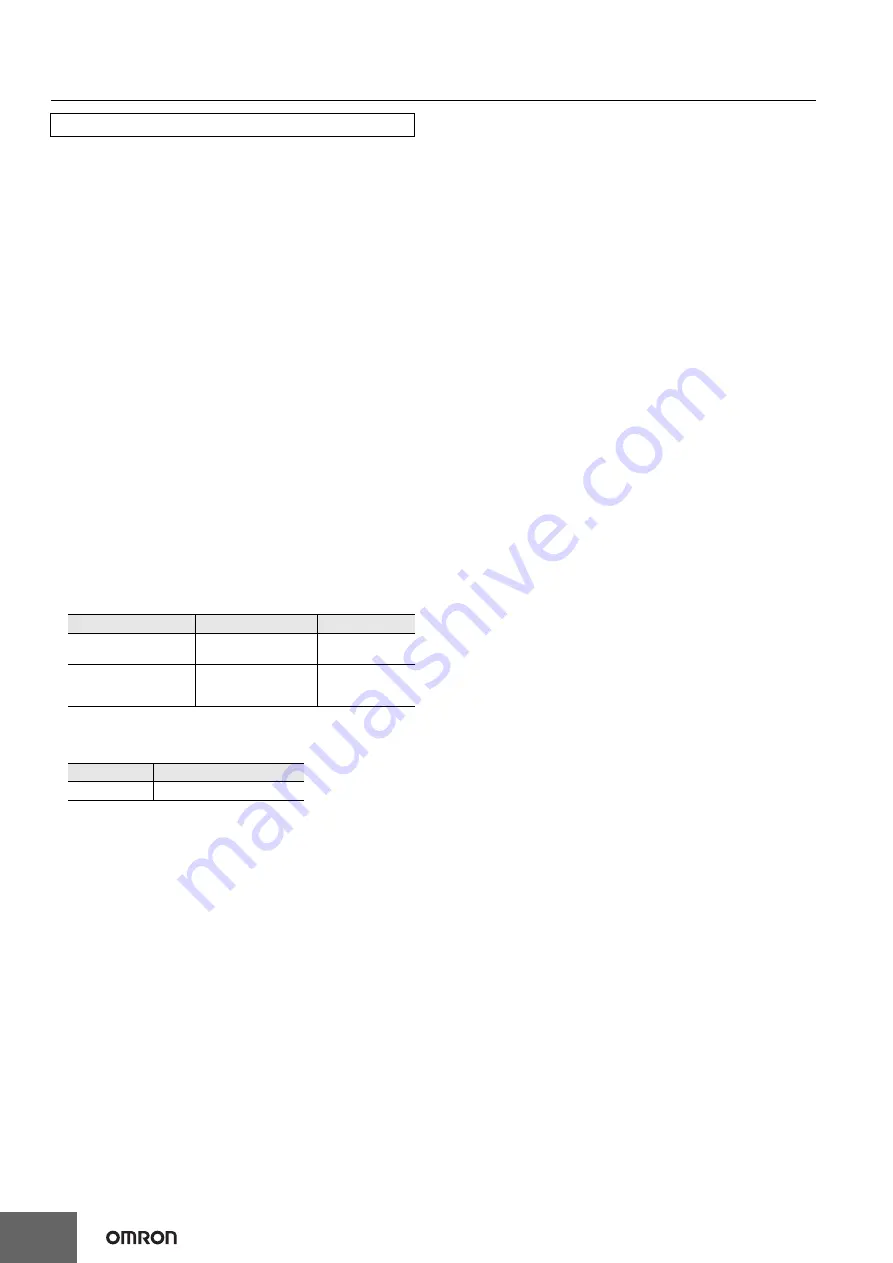
E5CD/E5ED
44
Be sure to observe the following precautions to prevent operation
failure, malfunction, or adverse affects on the performance and
functions of the product. Not doing so may occasionally result in
unexpected events. Do not handle the Digital Temperature Controller
in ways that exceed the ratings.
1.
The product is designed for indoor use only. Do not use or store
the product outdoors or in any of the following places.
• Places directly subject to heat radiated from heating equipment.
• Places subject to splashing liquid or oil atmosphere.
• Places subject to direct sunlight.
• Places subject to dust or corrosive gas (in particular, sulfide gas
and ammonia gas).
• Places subject to intense temperature change.
• Places subject to icing and condensation.
• Places subject to vibration and large shocks.
2.
Use and store the Digital Temperature Controller within the rated
ambient temperature and humidity. Gang-mounting two or more
Digital Temperature Controllers, or mounting Digital Temperature
Controllers above each other may cause heat to build up inside the
Digital Temperature Controllers, which will shorten their service
life. In such a case, use forced cooling by fans or other means of
air ventilation to cool down the Digital Temperature Controllers.
3.
To allow heat to escape, do not block the area around the Digital
Temperature Controller. Do not block the ventilation holes on the
Digital Temperature Controller.
4.
Always check the terminal names and polarity and be sure to wire
properly.
5.
To connect bare wires, use copper stranded or solid wires.
To prevent smoke emission and fire in the wiring material, check
the rating of the wire and use the wire in the table below.
Recommended Wires
Use the specified size of crimped terminals to wire the E5CD or
E5ED.
Crimp Terminal Sizes
For the E5
@
D-B (Push-In Plus model), connect only one wire to
each terminal.
For the E5CD/E5ED (Screw model), up to two wires of same size
and type, or two crimp terminals, can be inserted into a single
terminal.
6.
Do not wire the terminals that are not used.
7.
To avoid inductive noise, keep the wiring for the Digital
Temperature Controller's terminal block away from power cables
that carry high voltages or large currents. Also, do not wire power
lines together with or parallel to Digital Temperature Controller
wiring. Using shielded cables and using separate conduits or ducts
is recommended.
Attach a surge suppressor or noise filter to peripheral devices that
generate noise (in particular, motors, transformers, solenoids,
magnetic coils or other equipment that have an inductance
component).
When a noise filter is used at the power supply, first check the
voltage or current, and attach the noise filter as close as possible
to the Digital Temperature Controller.
Allow as much space as possible between the Digital Temperature
Controller and devices that generate powerful high frequencies
(high-frequency welders, high-frequency sewing machines, etc.)
or surge.
8.
Use the Digital Temperature Controller within the rated load and
power supply.
9.
Make sure that the rated voltage is attained within 2 seconds of
turning ON the power using a switch or relay contact. If the voltage
is applied gradually, the power may not be reset or output
malfunctions may occur.
10.
Make sure that the Digital Temperature Controller has 30 minutes
or more to warm up after turning ON the power before starting
actual control operations to ensure the correct temperature
display.
11.
When using adaptive control, turn ON power for the load (e.g.,
heater) at the same time as or before supplying power to the
Digital Temperature Controller. If power is turned ON for the Digital
Temperature Controller before turning ON power for the load,
tuning will not be performed properly and optimum control will not
be achieved.
12.
During tuning,* ensure that the power for the load (e.g., heater) is
ON. If the power supply to the load (e.g., heater) is not turned ON
during tuning, tuning results will not be calculated correctly and it
will not be possible to achieve optimum control.
* “Tuning” refers to the following functions: AT, adaptive control, automatic
filter adjustment, and water-cooling output adjustment.
13.
A switch or circuit breaker must be provided close to Digital
Temperature Controller. The switch or circuit breaker must be
within easy reach of the operator, and must be marked as a
disconnecting means for Digital Temperature Controller.
14.
Wipe off any dirt from the Digital Temperature Controller with a soft
dry cloth. Never use thinners, benzine, alcohol, or any cleaners
that contain these or other organic solvents. Deformation or
discoloration may occur.
15.
Design the system (e.g., control panel) considering the 2 seconds
of delay in setting the Digital Temperature Controller’s output after
the power supply is turned ON.
16.
The output will turn OFF when you move to the Initial Setting
Level. Take this into consideration when performing control.
17.
The number of non-volatile memory write operations is limited.
Therefore, use RAM write mode when frequently overwriting data,
e.g., through communications.
18.
Always touch a grounded piece of metal before touching the
Digital Temperature Controller to discharge static electricity from
your body.
19.
Use suitable tools when taking the Digital Temperature Controller
apart for disposal. Sharp parts inside the Digital Temperature
Controller may cause injury.
20.
Install the DIN Track vertically to the ground.
21.
Observe the following precautions when drawing out the body of
the Digital Temperature Controller.
• Follow the procedure given in
Drawing Out the Interior Body of
the Digital Temperature Controller to Replace It
on page 47.
• Turn OFF the power supply before you start and never touch nor
apply shock to the terminals or electric components.
When you insert the interior body of the Digital Temperature
Controller, do not allow the electronic components to touch the
rear case.
• When you insert the interior body into the rear case, confirm that
the hooks on the top and bottom are securely engaged with the
case.
• If the terminals are corroded, replace the rear case as well.
22.
For the power supply voltage input, use a commercial power
supply with an AC input. Do not use the output from an inverter as
the power supply. Depending on the output characteristics of the
inverter, temperature increases in the product may cause smoke
or fire damage even if the product has a specified output frequency
of 50/60 Hz.
23.
Do not continue to use the Digital Temperature Controller if the
front surface peels.
24.
Do not exceed the communications distance that is given in the
specifications and use the specified communications cable. Refer
to the
E5
D Digital Temperature Controllers User's Manual
(Cat.
No. H224) for information on the communications distances and
cables for the E5
D.
25.
Do not turn the power supply to the Digital Temperature Controller
ON or OFF while the USB-Serial Conversion Cable is connected.
The Digital Temperature Controller may malfunction.
Precautions for Safe Use
Model
Recommended wires
Stripping length
E5CD/E5ED
(Screw Terminal Blocks)
AWG24 to AWG18
(0.21 to 0.82 mm
2
)
6 to 8 mm
E5
@
D-B (Push-In Plus
Terminal Blocks)
0.25 to 1.5 mm
2
(equivalent to AWG24 to
AWG16)
Ferrules not used:
8 mm
Model
Crimp terminal size
E5CD or E5ED
M3, Width: 5.8 mm max.
Summary of Contents for E5CD
Page 54: ...MEMO 54 ...