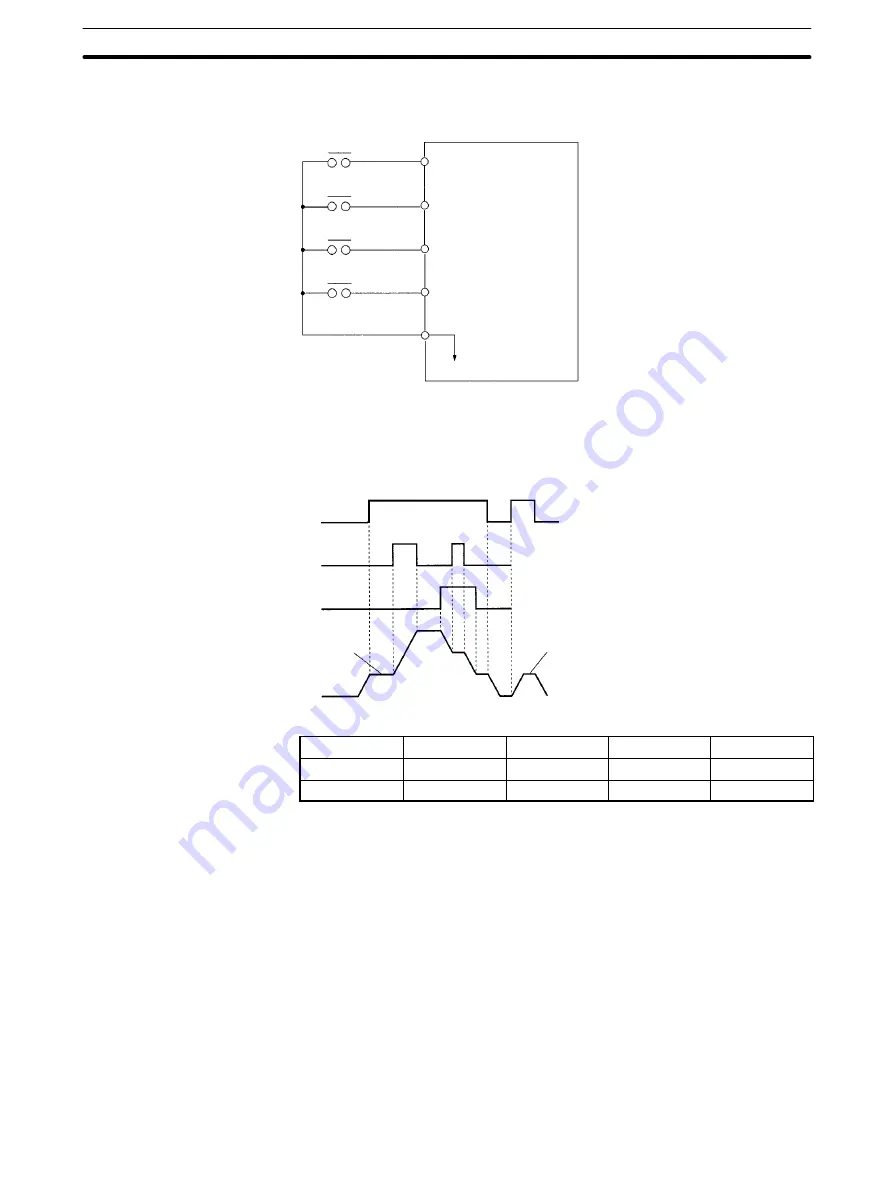
54
This command is used to increase or decrease the Inverter’s fre-
quency using the sequence input.
FWD/STOP
REV/STOP
UP
DOWN
Note
When No. 33 is set to ”14” UP/DOWN command, the UP command
will be allocated to terminal 4 and the settings of No. 32 will be
ignored.
Run command
(FWD/STOP, REV/STOP)
UP command
(terminal 4)
DOWN command
(terminal 5)
Output frequency
Acceleration and decel-
eration follow the time
set as acceleration time
or deceleration time.
(See note)
(See note)
Terminal 4
ON
OFF
OFF
ON
Terminal 5
OFF
ON
OFF
ON
Accelration
Deceleration
Hold
Hold
Note
Once the Run command is input, rotation starts from either the
minimum frequency or the lower frequency limit, whichever is
higher.
UP/DOWN Command
Description of Functions and Constants
Section 2-8