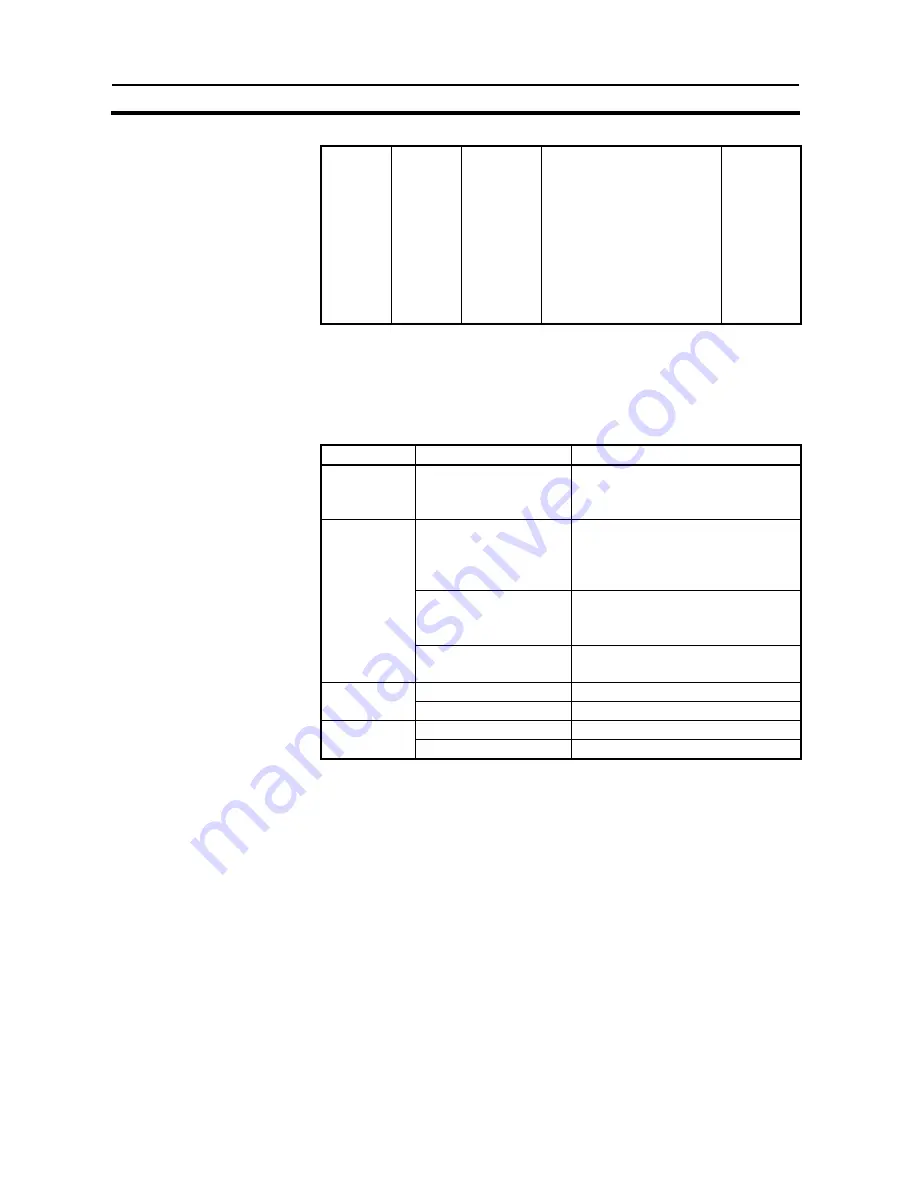
Communication, Counter and Pulse
SECTION 4
DM 6642
08 to 15 High-speed
counter
setting
00: Do not use.
01: Use as high-speed
counter
02: Use as synchronized
pulse control (10 to 500 Hz).
03: Use as synchronized
pulse control (20 Hz to 1
kHz).
04: Use as synchronized
pulse control (300 Hz to 20
kHz).
Either 00
or 01
If absolute pulses are specified with PULS(65), be sure to set the absolute
coordinate system (1).
Synchronized pulse control cannot be used simultaneously.
The settings will go into effect when the mode is changed (from PROGRAM
to MONITOR/RUN) or when the power supply is turned ON to the PLC.
Ladder Diagram
The following table shows the instruction operations related to pulse outputs
Programming
without acceleration and deceleration (fixed duty ratio).
Instruction Control
Operation
(@)PULS(65)
Set number of pulses
Sets the number of pulses to be
output
in independent mode.
Set frequency and start
pulse outputs
Sets the frequency for outputs in the
independent mode or continuous
mode,
and starts the pulse outputs.
Change frequency
Changes the frequency for outputs in
the independent mode or continuous
mode.
(@)SPED(64)
Stop pulse outputs
Stops the pulse outputs (by changing
the speed to a frequency of 0 Hz).
Stop pulse outputs
Stops the pulse outputs.
(@)INI(61)
Change pulse output PV
Changes the pulse output PV.
Read pulse output PV
Reads the pulse output PV.
(@)PRV(62)
Read pulse output status
Reads the pulse output status.
50
Summary of Contents for 3G3MV-P10CDT-E
Page 2: ...3G3MV P10CDT PLC Option Unit User s Manual Revised June 2003 ...
Page 38: ...Unit Components and Specifications SECTION 2 2 1 4 Dimensions 68 128 55 25 ...
Page 43: ......
Page 85: ...Example Programs Appendix B 72 ...
Page 86: ...Example Programs Appendix B 73 ...
Page 87: ...Example Programs Appendix B 74 ...
Page 88: ...Example Programs Appendix B 75 ...
Page 90: ...Example Programs Appendix B 77 ...
Page 91: ...Example Programs Appendix B 78 ...
Page 97: ...Example Programs Appendix B B 4 9 Programs User_Parameter_Init 84 ...
Page 98: ...Example Programs Appendix B 85 ...
Page 99: ...Example Programs Appendix B User_Application Pos_Loop 86 ...
Page 100: ...Example Programs Appendix B 87 ...
Page 101: ...Example Programs Appendix B 88 ...
Page 102: ...Example Programs Appendix B 89 ...
Page 103: ...Example Programs Appendix B 90 ...
Page 104: ...Example Programs Appendix B 91 ...
Page 105: ...Example Programs Appendix B 92 ...
Page 106: ...Example Programs Appendix B 93 ...
Page 107: ...Example Programs Appendix B Pos_Home_Sequence 94 ...
Page 108: ...Example Programs Appendix B 95 ...
Page 109: ...Example Programs Appendix B 96 ...