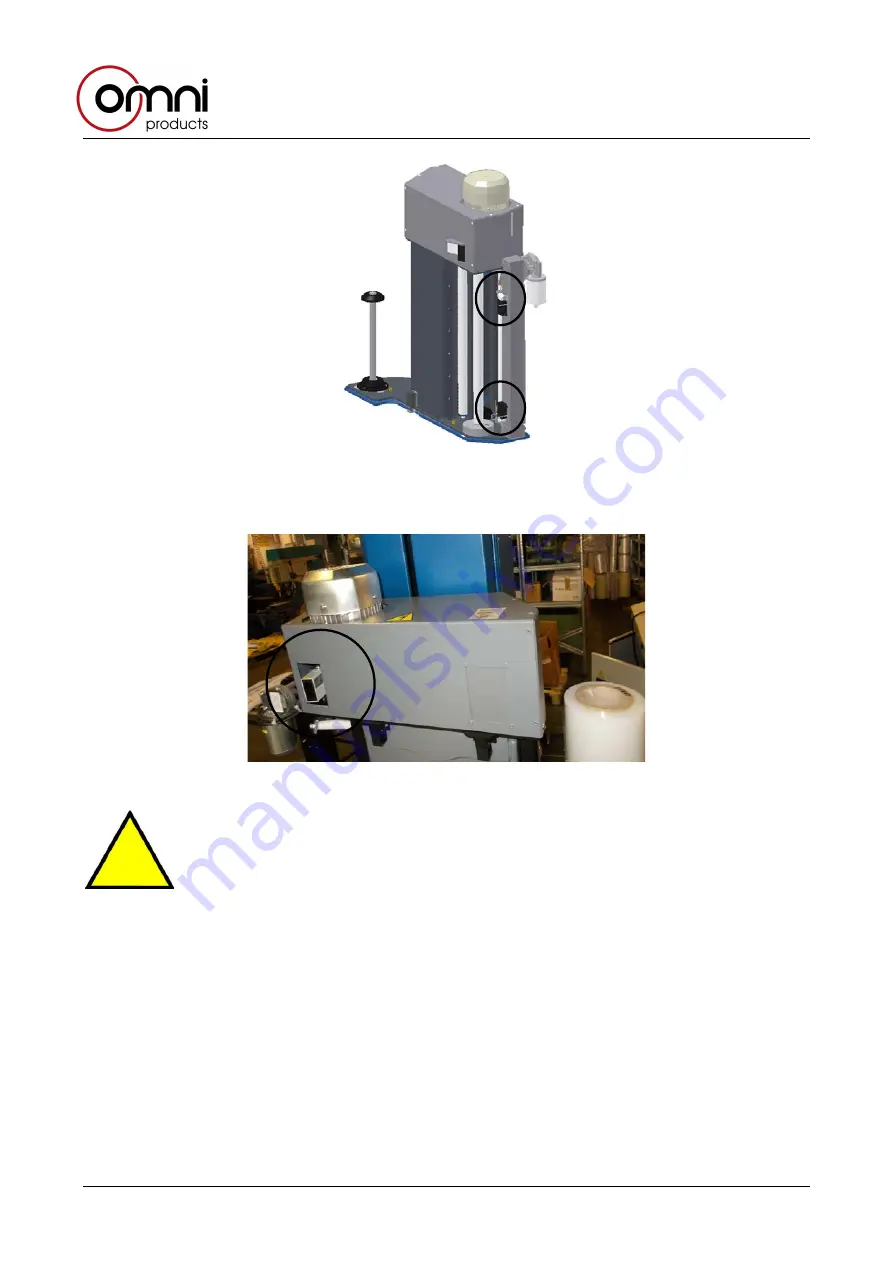
About every month or every 200 working hours, check that the photocell reading the pallet height is
centered and that any support brackets are tightened.
5.4 PNEUMATIC PARTS MAINTENANCE
About every month or every 200 working hours, the following checks must be carried out:
-
a periodic check of the tube coupling / rapid connection of all electro-valves; before carrying out
this operation, depressurize the pneumatic plant and disconnect the machine from the power
supply;
-
a pressure check
(the machine must be under controlled risk conditions, in EMERGENCY
STOP);
-
check the tightening of the operating coils of the electro-valves; before carrying out this
operation, depressurize the pneumatic plant and disconnect the machine from the power
supply
.
Omni
SUPERPLUS EN IGM_REV6
43